Анализ состояния станочной системы токарной обработки при интеллектуальном управлении
Секция: Технические науки
лауреатов
участников
лауреатов


участников


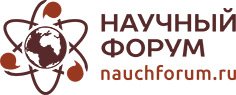
V Студенческая международная научно-практическая конференция «Технические и математические науки. Студенческий научный форум»
Анализ состояния станочной системы токарной обработки при интеллектуальном управлении
Аннотация: в статье изложено состояние вопроса и обобщены основные результаты научных работ, посвященных проектированию информационно-измерительных подсистем, а также исследованию в области получения, обработки, представления и использования измерительной информации в различных классах систем управления металлорежущими станками.
Annotation: the article describes the state of the issue and summarizes the main results of scientific works on the design of information-measuring subsystems, as well as research in the field of obtaining, processing, presentation and use of measurement information in various classes of control systems of machine tools.
Ключевые слова: токарное оборудование, токарная обработка, интеллектуальные системы, автоматизированные системы, многофункциональность.
Keywords: turning equipment, turning processing, intelligent systems, automated systems, multifunctionality.
Основная часть
Современные тенденции развития токарного оборудования сосредоточены в многофункциональности и гибридности инновационных решений согласно трендам новой организации цифровых производств.
Токарная технология вместе с фрезерной составляет базовую основу металлообработки, поэтому все станкостроительные лидеры развивают токарное направление, создавая многофункциональные станочные комплексы в различных конфигурациях. Востребованные производством решения достигаются за счет технических инноваций, высокой автоматизации, опционного дооснащения, комбинирования обрабатывающих технологий и кинематики [1. c, 43]. При этом трудность внедрения технологических инноваций в токарных станках проявляется в том, что их основными рабочими характеристиками является производительность, конструктивная компактность и точность, противоречивые по своей сути, когда улучшение одной из них ведет к ухудшению другой.
Особенность токарных инноваций – они в большинстве своем не прорывные, а гибридные, состоящие из ряда известных решений и опций, но их новая конфигурация дает новый производственный эффект, не известный ранее [3, с. 61].
Современный этап развития этого вида оборудования основывается на таких закономерностях инноватики [1, с. 90]:
-закон согласования ритмики обеспечивает оптимальную синхронизацию пространственно-временной, кинематико-энергетической, упруго-силовой и информационно-преобразовательной подсистем станка;
-закон повышения степени идеальности системы приводит к миниатюризации техники при одновременном повышении уровня технологических возможностей – компактная многофункциональность;
-закон неравномерности развития частей системы отражает ее сложность, а значит, диспропорции в функциональности и ресурсоемкости.
К современным тенденциям развития токарного оборудования можно отнести следующие:
I. Тотальная автоматизация и комплексирование решений для цифрового производства.
1) Многоцелевые системы.
2) Автоматы.
3) Опционное комплексирование на единой несущей платформе.
II. Новые токарные технологии.
1) Полигональное точение для многогранников.
2) Тангенциальное («бреющее») точение.
III. Уникальные станочные решения.
1) Револьверность.
2) Центральный привод.
3) Крупногабаритность.
4) Интеллектуальность.
5) Компактность и полнота использования рабочей зоны.
В качестве примера системного подхода к развитию технологического оборудования премиум-класса приведем токарные решения фирмы EMAG, которая комплексно развивает этот сегмент продукции в следующих продуктовых направлениях [4, с. 82]:
-модульные станки;
-многофункциональные;
-для крупных деталей серии modular;
-адаптируемые станки серии для мелкосерийного производства;
-производственные ячейки;
-многошпиндельные станки.
Каждый из продуктов EMAG разработан для оптимизации машиностроительного производства с учетом концепции Industrie 4.0 и предназначен для системного решения производственных задач, в числе которых:
-подготовка производства (наладки, инструменто-оснащения, программы ЧПУ);
-контроллинг (встроенные измерительные щупы, датчики, средства контроля);
-управление (оптимизация подготовки цикла, обработки и контрольных функций);
-сервисное обслуживание и техническое послепродажного сопровождения (рис. 1).
Рисунок 1. Комплексный подход к созданию продуктовых решений в рамках концепции Industrie 4.0
Узнаваемость бренда определяется следующими функциональными признаками станочных систем:
-вертикальная обработка деталей (шестерни коробок передач, звездочки, муфты, детали клиноременных вариаторов, корпуса шарниров, шатуны, кольца подшипников, детали типа диск, вал, фланец, гильза, вал-шестерня и др.) обеспечивает условия для падения стружки и упрощает обработку без использования СОЖ;
-многоцелевая система объединяет в себе токарную обработку, твердое точение, сверление, шлифование, фрезерование, зубофрезерование, лазерную обработку;
-«Pick-Up»-шпиндель обеспечивает автоматическую загрузку-выгрузку деталей;
-объединение в станке комплекса операций: загрузка/выгрузка заготовок (автоматизация), непосредственную обработку и измерение;
-технология тангенциальной токарной обработки с минимальным припуском («бреющий» принцип), позволяющая получать высокое качество обработанной поверхности, когда происходит движение «обкатки» инструмента с наклонной режущей кромкой из CBM по вращающейся детали (скорость резания создается за счет вращения заготовки). Налагающиеся друг на друга движения инструмента и заготовки позволяют обеспечить постоянное перемещение точки резания. Этот динамичный процесс примерно в 5–6 быстрее, чем уже существующие процессы твердой обработки, и в 2–3 раза быстрее, чем шлифование;
-конфигурация технологических модулей и индивидуальная адаптация станка под конкретные производственные задачи. Наличие разнообразных компонентов систем автоматизации обеспечивает легкость встраивания станка в любые автоматические линии (рис. 2).
Рисунок 2. Варианты конфигурирования технологических модулей под производственные задачи
Например, вертикальный токарный центр VTC 200-4 ведет обработку деталей типа «вал» длиной до 630 мм и диаметром до 200 мм, для чего предусмотрены две револьверные головки, на каждой из которых имеется по 11 гнезд для установки инструмента [4, с. 32]. Это позволяет обрабатывать заготовки одновременно с двух сторон по четырем осям ЧПУ, что значительно сокращает время цикла. В то время как один грейфер (автооператор) токарного центра забирает готовую деталь из рабочей зоны и укладывает ее на ленту транспортера, второй грейфер захватывает следующую заготовку из накопителя, находящегося с другой стороны станка, и перемещает ее в позицию обработки.
Соединение нескольких модулей в одну систему (мод. VSC TWIN, VSC TRIO) дает вдвое/втрое большую производительность на одной и той же производственной площади за счет одновременной синхронной обработки двух/трех деталей по одинаковой технологии [4, с. 43].
Важнейшей проблемой современного автоматизированного производства является повышение точности изготовления деталей. В современных условиях эта проблема приобретает особое значение. Несмотря на существующие достижения в области исследования металлорежущих станков, обеспечение точности механической обработки по-прежнему остается актуальной проблемой [6, с. 53].
Точностные возможности при использовании станков с числовым программным управлением (ЧПУ) реализуются на 50-70%, потери времени, возникающие из-за технологических отказов, к примеру, размерный брак приводят к значительной потери производительности и увеличению себестоимости выпускаемой продукции.
Для решения проблемы связанной с максимальным использованием точностных возможностей станков с ЧПУ создаются информационно-управляющие комплексы, с помощью которых возможно осуществлять текущий контроль за ходом процесса обработки деталей и коррекцию режимов обработки для обеспечения требуемой точности изготовления деталей.
Состояние любой системы, и системы СПИД (станок, приспособление, инструмент, деталь) в частности, характеризуется определенным уровнем ее энтропии. Энтропия есть величина, характеризующая неопределенность состояния системы – ее структуры и значений ее параметров. Условимся, что под неопределенностью системы будем понимать нечеткость значений множества ее наблюдаемых параметров.
В случае применения метода прямых измерений информация, получаемая при этом равна:
где – априорная энтропия параметра
до процедуры измерения;
– апостериорная энтропия параметра
измеряемого непосредственно.
Для определения величины некоторых параметров применяется метод косвенных измерений. Поэтому необходимо оценивать величину получаемой информации о параметрах при косвенных измерениях. Выражение для информации имеет вид:
где – априорная энтропия параметра до процедуры измерения;
– совместная энтропия параметров, определяемая степенью их взаимосвязи;
– апостериорная энтропия параметра измеряемого непосредственно.
Энтропия дискретного множества определяется по формуле:
где – плотность распределения вероятностей элементов множества
;
– совместная плотность распределения вероятностей для прямого произведения множеств
и
.
Для непрерывного множества это выражение принимает вид:
где ,
– интервал времени измерения.
Условная энтропия может быть определена следующим образом:
Таким образом, учитывая, что о величине косвенно измеряемого параметра можно судить по параметрам, то количество информации о его величине, содержащееся в измеряемых параметрах определяется системой:
Полученные уравнения позволяют сделать следующие заключения о способах повышения информативности.
Первый способ – поиск таких источников измерительной информации, которые обладают достаточно низкой дифференциальной энтропией относительно оцениваемого параметра, т.е. находятся с ним в наиболее тесной связи. В словосочетании «достаточно низкая условная энтропия» заключена возможность варьирования предельным значением условной энтропии в зависимости от различных факторов. Это такие факторы как аппаратные и программные возможности, максимально допустимая стоимость реализации, требуемая точность измерений и др.
Второй способ – совершенствование средств и методов измерения с целью минимизации энтропии множества измеряемых параметров.
Третий способ – привлечение аппарата нечеткой логики для оценки информативности измеряемых параметров в связи с невозможностью определения и формирования характеристик распределения вероятности в процессе выполнения измерений.
