Методика разработки режимов термической и химико-термической обработки математическим моделированием процессов
Секция: Технические науки
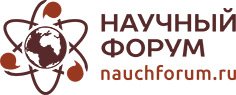
VII Студенческая международная научно-практическая конференция «Технические и математические науки. Студенческий научный форум»
Методика разработки режимов термической и химико-термической обработки математическим моделированием процессов
Methods of development of modes of thermal and chemical-thermal processing by mathematical modeling of processes
Boris Maslov
master's student of Lipetsk state technical University, Russia, Lipetsk
Elena Nemtseva
master's student of Lipetsk state technical University, Russia, Lipetsk
Anna Sheveleva
master's student of Lipetsk state technical University, Russia, Lipetsk
Igor Tsyganov
scientific supervisor candidate of technical Sciences, associate Professor of Lipetsk state technical University, Russia, Lipetsk
Аннотация. Разработка режимов термической обработки для улучшения механических, физических и технологических свойств углеродистых сталей осуществлялась математическим моделированием процессов.
Abstract. The development of thermal treatment modes to improve the mechanical, physical and technological properties of carbon steels was carried out by mathematical modeling of processes.
Ключевые слова: термообработка, сталь, математическая модель, расчет, режим, химический состав, структура, размеры деталей, твердость.
Keywords: Key words: heat treatment, steel, mathematical model, calculation, regime, chemical composition, structure, dimensions of parts, hardness.
Для разработки математических моделей использованы положения теории фазовых превращений и физики прочности сплавов, результаты экспериментальных исследований закономерностей формирования структуры и свойств сталей при термической и химико-термической обработке.
Разработано математическое описание влияния химических элементов на критические точки фазовых превращений в конструкционных сталях. Разработана математическая модель нагрева деталей в промышленных печах, учитывающая массу садки, размеры и форму деталей.
Предложены принципы автоматизированного проектирования режимов операций закалки и отпуска конструкционных сталей.
В качестве входной используется следующая информация: химический состав сталей, размеры и форма деталей, расположение деталей в печи, требуемая структура и твердость стали. Выходными данными являются параметры термообработки Тн и Тв во время нагрева под закалку, закалочная среда, ТН отпуск и τвыдотпуск.
Разработана математическая модель диффузии углерода при газовой цементации сталей, учитывающая исходный химический состав стали, углеродный потенциал и скорость перемещения насыщающей среды, температуру цементации. Разработана математическая модель, устанавливающая связь распределения углерода в диффузионном слое и содержащихся в стали легирующих элементов с распределением твердости по глубине диффузионного слоя до и после заключительной операции термообработки (закалка и низкий отпуск).
Предложены алгоритмы автоматизированного расчета режимов газовой цементации конструкционных сталей, обеспечивающих получение необходимой глубины цементованного слоя, заданной твердости на поверхности и в сердцевине изделия.
Входными параметрами расчета режимов и операций газовой цементации конструкционных сталей являются: химический состав стали, углеродный потенциал насыщающей среды, размеры и форма деталей, расположение деталей в печи, требуемая глубина диффузионного слоя, твердость поверхности и сердцевины детали. Выходными данными являются параметры термообработки цементации: Тц и τц, Тн2 и τвыд при последующем нагреве цементованных деталей под закалку, охлаждающая среда, Тотп и τвыдотп.
График термообработки, поверхностная твердость, положение критических точек А1 и А3 критических точек, до и после газовой цементации были рассчитаны на ЭВМ. С помощью математического моделирования на ЭВМ изучено влияние различных факторов на процесс газовой цементации стали, являющейся наиболее распространенным процессом химико-термической обработки.
Вопросы совершенствования технологии термообработки стальных изделий ‒ это по существу вопросы повышения качества машин и аппаратов современной техники.
Математическое моделирование позволяет разработать технологию термической обработки с минимальными затратами.
Конечной целью работы по созданию технологии термообработки является создание системы автоматизированного проектирования режимов термической обработки и химико-термической обработки низко и средне-легированных конструкционных сталей.
Управление макро и микроструктурой, происходит при разработке оптимальных технологий базирующихся на математических моделях фазовых и структурных изменениях происходящих при термообработке стали.
Разработка математических моделей требует рассмотрения превращений происходящих при термической обработке и химико-термической обработке сталей, а также при нагреве, выдержке, закалке и отпуске.
Температура нагрева под закалку для большинства сталей определяется положением критических точек А1 и А3. Для углеродистых сталей температура закалки может быть определена по диаграмме железо-углерод.
Доэвтектоидные стали нагревают до температуры на 30–50 оС выше точки А3 [1, с. 9‒12]. В этом случае сталь с исходной структурой перлит плюс феррит при нагреве приобретает аустенитную структуру, которая при последующем охлаждении со скоростью выше критической превращается в мартенсит.
Температура закалки для углеродистых заэвтектоидных сталей составляет Асм плюс 50‒70 оС, а повышение температуры выше этой температуры увеличивает размер зерна, что приводит затем снижает предел прочности. Интервал изменения температур закалки для большинства заэвтектоидных сталей невелик (15–20 оС) [1, с. 10].
Если для заэвтектоидных сталей в огромном большинстве случаев превышение указанных температур недопустимо в силу отмеченных причин, то для доэвтектоидных сталей в ряде случаев применяется “высокая закалка”, т.е. закалка от температур, превышающих А3 более, чем на 30‒50 оС
Действительно перегрев (не очень значительный) наследственно мелкозернистой стали выше А3 не вызовет роста зерна, тогда как более высокой закалкой можно достигнуть гомогенизации твердого раствора (а отсюда повышение механических свойств), углубления закалки и других желательных результатов. Однако, перегрев при закалке допустим лишь для наследственно-мелкозернистых сталей. В наследственно-крупнозернистой стали перегрев приводит к росту зерна, а в связи с этим и к увеличению внутренних напряжений [1, с. 11].
В среднелегированных сталях, получающийся в результате закалки и отпуска низколегированный легированный феррит в сочетании с низколегированными и поэтому более крупными частицами карбидов понижает механические свойства [1, с. 9‒12].
Температура закалки легированных конструкционных сталей также определяется положением критических точек А1 и А3, определяемых при помощи диатермического метода, методом закалки или другим путем.
Зная значение критических точек, температуру закалки выбирали по правилу:
для доэвтектоидной стали
tзак = А3 + (30‒50) оС (1)
для заэвтектоидной стали
tзак = А1 + (50‒70) оС (2)
Для высоколегированной стали, а также для некоторых специальных случаев термической обработки малолегированных сталей температура закалки определяется требованиями получения определенной структуры или свойства закаленной стали.
Добавка в сталь дополнительно легирующие элементы изменяет температурные границы протекания процессов фазовых превращений при нагревании. Легирующие элементы вызывают в основном сдвиг критических точек по температуре по отношению к их положению . на диаграмме Fe‒Fe3C.
Не карбидообразующие элементы (Ni, Co, Mn, Cu) их понижают, а карбидообразующие (Cr, Mo, W, V, Si, Ti, Al, B, Nb, Zr) повышают критические толчки.
Если сталь содержит элементы с противоположным влиянием на критические точки, то конечный эффект зависит от количественного соотношения элементов.
Сдвигаются критические точки не только по температуре, но и по концентрации химических элементов. Легирующие элементы Cr, Mo, W, Si, Ni) cнижают содержание углерода в эвтектоиде, и сдвигают эвтектоидную точку в сторону меньших концентраций.
Нагрев стали до заданной температуры желательно проводить быстро, т. к. это увеличивает производительность нагревательных устройств, а следовательно уменьшает количество и размер печей и другого оборудования, требующихся для выполнения заданной программы, уменьшает количество требуемой рабочей силы и т.д.
Для практического проведения того или иного вида термической обработки нужен не только нагрев до необходимой температуры, но и нужна выдержка для окончания превращений.
Общее время пребывания изделий в печи слагается из двух величин:
tобщ = tн + tв (3)
Первый член определяется способом нагрева, свойствами материала, размерами и формой изделия; второй ‒ скоростью превращений на достигнутой температуре.
Обработка холодом применима к сталям, температура точки Mк которых находится ниже комнатной температуры, и у которых содержится большое количество остаточного аустенита (более 20 %) после закалки. Глубокое охлаждение проводят с целью повышения твердости, режущих свойств, износостойкости в термически улучшенном состоянии, а иногда для исключения распада очень стабильного остаточного аустенита вплоть до охлаждения с температуры отпуска, иногда в процессе эксплуатации. Целесообразность такого дорогого вида необходимо, прежде всего, проанализировать с экономической точки зрения.
Температура обработки холодом не должна быть значительно ниже, чем температура Mк, с тем, чтобы не возникали избыточные термические напряжения. По этой же причине стали обычно не подвергают обработке холодом с температуры аустенизации.
Для предупреждения стабилизации остаточного аустенита обработку холодом стали проводят сразу же после закалки, а устройство для криогенной обработки устанавливают в закалочной линии между участками закалки и отпуска. В том случае, когда существует опасность задержки обработки холодом закаленной стали перед ее отпуском и стабилизации аустенита, ее можно заменить ступенчатой закалкой в сочетании с обработкой холодом. Но это повышает хрупкость закаленной стали вследствие меньшего содержания остаточного аустенита в закаленной стали и отсутствия самоотпуска мартенсита при закалке.
Скорость охлаждения после отпуска, как правило, не лимитируется. Обычно изделия охлаждаются на воздухе.
Быстрое охлаждение после отпуска применяют лишь для предотвращения развития отпускной хрупкости второго рода. Развитие отпускной хрупкости для многих сталей подавляется при охлаждении в масле.
На этапе математического описание задачи "Закалка ‒ отпуск" были сформулированы задачи и круг решаемых вопросов, математическое обозначение всех переменных; осуществлена запись уравнений задачи, описывающих физические процессы, определены ограничения на условия задачи, выявлены исходные и искомые величины.
Критические точки A1 и A3, а также содержание углерода в эвтектоиде легированной стали S зависят от содержания легирующих элементов в стали. На температуру нагрева, время нагрева и время выдержки также влияет среда и размеры изделий.
Охлаждающую среду определяли сравнивая диаметр образца с критическим диаметром закалки. При определении температуры обработки холодом исходили из условия что содержание Аост не должно превышать 15‒20 %, а если более то обработка холодом целесообразна ниже точки конца мартенситного превращения Mк.
Моделирование газовой цементации осуществляли на изделиях из сталей, в которых исходное содержание углерода не превышает 0,25 %. Цементованные изделия приобретают улучшенные свойства после правильной закалки и последующего отпуска. Термическая обработка цементованных изделий имеет ряд характерных особенностей. Продолжительный нагрев при цементации способствует значительному росту зерна. Термическая обработка должна исправить этот дефект цементации.
Математическое моделирование технологических процессов цементации выполняли в две стадии. На первой стадии разрабатывали математическую модель, на второй проводили её исследование с целью решения тех или иных технологических задач [2, с. 70‒72].
Математические модели технологии газовой цементации были реализованы в виде программы под названием "CEMENT.EXE", предназначенной для определения режимов цементации и последующей термообработки цементованных сталей [3, с. 124‒127].
Разработанная математическая модель нагрева деталей в промышленных печах, учитывает массу садки, размеры и форму деталей.
