Основные этапы процесса проектирования универсально-сборного приспособления с использованием CAD-систем
Секция: Технические науки
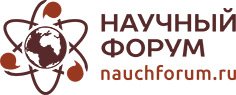
L Студенческая международная научно-практическая конференция «Молодежный научный форум: технические и математические науки»
Основные этапы процесса проектирования универсально-сборного приспособления с использованием CAD-систем
Универсально-сборные приспособления достаточно широко используются на машиностроительных предприятияхв условиях единичного и мелкосерийного производства, а так жепри освоении новой продукции в серийном производстве.Проектирование компоновкиУСП включает в себя разработку комплекса технической документации содержащей расчеты, чертежи, технико-экономические обоснованиеи завершается созданием конструкторской рабочей документации [2].
Первым этапом проектирования компоновки УСП является выбор исходных данных.
Исходными данными для проектирования компоновок УСП являются:
· рабочий чертеж обрабатываемой заготовки со всеми техническими условиями;
· 3D-модель детали, выполненной в программе AutodeskInventor;
· описание технологической операции, содержание переходов;
· операционный эскиз обрабатываемой заготовки с указанием схемы ее установки;
· используемые технологические базы и их установочные размеры;
· применяемый инструмент, его размеры, траектория движения и материал режущей части;
· режимы резания: скорость, подача, сила резания;
· программа выпуска деталей;
· дополнительные указания технолога;
· вид зажимных устройств;
· проектная норма штучного времени;
· время, отводимое для установки, закрепления и снятия заготовки;
· библиотека компоновок УСП, применяемых на предприятиях;
· размеры присоединительных мест, размеры и расположение Т-образных пазов оборудования, на котором будет выполняться технологическая операция.
Компоновки универсально-сборных приспособлений собираются при необходимости из имеющегося на предприятии комплекта стандартных или нормализованных деталей. После выполнения на них обработки партии деталей компоновки разбираются и при необходимости собираются новые компоновки, которые затем используют для обработки другой партии деталей. Срок службы элементов комплекта УСП при достаточно интенсивной эксплуатации до 25 лет. Количество элементов в комплекте УСП определяет число компоновок, которое можно одновременно собрать из комплекта в течение года [4; 5].
В формализованном виде проектирование компоновки технологической оснастки на основе УСП с использованием CAD-систем можно представить в виде алгоритма (рисунок 1).
Этап 1 – ввод исходных данных. На этом этапе вводятся в систему рабочий чертеж обрабатываемой заготовки; 3D-модель детали; формализованное описание технологической операции (характеристики применяемого инструмента, последовательность и содержание переходов, используемые технологические базы и их размеры, режимы резания (скорость резания, подача инструмента, сила резания)); программа выпуска деталей; паспортные данные станка, на котором производится операция (размеры присоединительных мест, размеры и расположение Т-образных пазов и др.).
Рисунок 1. Блок-схема алгоритма проектирования универсально-сборных приспособлений с использованием CAD-системы
Этап 2 – выбор установочных элементов (блок 2) из библиотеки установочных элементов УСП (блок 3). Положение базовых поверхностей заготовки в пространстве должно быть определенно и не иметь возможности сдвига и (или) вращения относительно трех координатных осей. Расстояние между опорами принимают, возможно, большим, чтобы под действием сил не возникал опрокидывающий момент [1].
Этап 3 – расчет погрешности базирования (блок 4). Погрешность базирования во многом определяет точность обработки на проектируемой технологической оснастке. Выполняется с помощью подпрограммы «Расчет погрешности базирования» реализуемой в Microsoft ® Excel и связанной макросом в Autodesk Inventor.
Этап 4 – выбор корпусных элементов (блок 5) из библиотеки корпусных элементов (блок 6).Выбор типа корпусных элементов определяется размерами и формой обрабатываемой заготовки, типом станка, особенностями компоновки отдельных элементов УСП и др. Выбранный элемент должен удовлетворять следующим основным требованиям: удобство установки и снятия заготовок и очистки УСП от стружки; достаточная прочность, жёсткость и устойчивость, удобство его крепления на столе станка; и что особенно важно при эксплуатации на станке с ЧПУ – свободный подход и выход режущего инструмента [3].
Этап 5 – расчет усилия закрепления обрабатываемой детали (блок 7). Выполняется с помощью подпрограммы «Расчет усилия закрепления» реализуемой в Microsoft ® Excel и связанной макросом с Autodesk Inventor.
Этап 6 – выбор конструкции зажимных элементов (блок 8) предназначенных для обеспечения надежного контакта обрабатываемой детали с установочными элементами и предотвращение ее смещения, а также вибрации в процессе обработки. Выбор производится из библиотеки зажимных элементов (блок 9).
Этап 7 – выбор направляющих элементов (кондукторные втулки, копиры) (блок 10) применяемые для устранения упругих отжатий инструмента и придания ему определенного положения относительно заготовки. Выбор производится из библиотеки направляющих элементов (блок 11).
Этап 8 – выбор типа и конструкции силового привода (блок 12) предназначенного для создания исходной силы, необходимой для закрепления заготовки. Как правило, в компоновке УСП применяется силовой привод, приводимый в действие непосредственно рабочим (винтовой, эксцентриковый и.т.п.). Выбор производится из библиотеки силовых приводов (блок 13).
Этап 9 – Расчет погрешности закрепления детали (блок 14). Выполняется с помощью подпрограммы «Расчет погрешности закрепления» реализуемой в Microsoft ® Excel и связанной макросом с Autodesk Inventor.
Этап 10 – оценка возможности использования и выбор сборочных единиц (блок 15), служащих для ускорения сборки компоновок УСП (поворотные головки, фиксаторы, центровые бабки и пр.). Выбор производится из библиотеки сборочных единиц.
Этап 11 – оценка необходимости применения разных элементов (шайбы стопорные и упорные, кольца, рукоятки, пружины и пр.) (блок 18). Если они необходимы, то выполняется их выбор (блок 19) из библиотеки разных элементов (блок 20).
Этап 12 – выбор базовых элементов УСП (блок 21) применяемые в качестве основания для сборки компоновки УСП. Выбор производится из библиотеки базовых элементов (блок 22).
Этап 13 – выбор крепежных элементов УСП (блок 23), предназначенных для соединения между собой элементов УСП при сборке компоновки. Выбор производится из библиотеки крепежных элементов (блок 24).
Этап 14 – расчет точности компоновки УСП (блок 25). Выполняется с помощью подпрограммы «Расчет точности компоновки УСП» выполняемой в Microsoft ® Excel и связанной макросом с Autodesk Inventor.
Этап 15 – проверка обеспечения точности обработки на спроектированной компоновке УСП (блок 26). Если условие выполняется, то далее выполняется этап 16, если же нет, то происходит возврат на (блок 1) для корректировки исходных данных, на (блок 2) для изменения выбранных установочных элементов или на (блок 10) для изменения выбранных или направляющих элементов.
Этап 16 –создается необходимая конструкторская документация (чертеж сборки УСП и спецификация) (блок 27).
