Подъемное оборудование и его модернизация
Секция: Технические науки
лауреатов
участников
лауреатов


участников


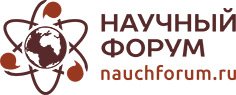
XLI Студенческая международная заочная научно-практическая конференция «Молодежный научный форум: технические и математические науки»
Подъемное оборудование и его модернизация
Подъемное оборудование и её история возникла еще в древности. Устройство первого грузоподъемника состояло из рычагов, наклонных плоскостей и катков (рисунок 1). Древнегреческий подъемник имело название «журавль» (рисунок 2) с немецкого языка «краних», в нашей стране его называли – «кран». Использовался «журавль» в V веке до нашей эры.
Рисунок 1. Первый подъемник
Рисунок 2. Древнегреческий подъемник
Для орошения земленных угодиев воду на востоке и Индии. До нашей эры в Китае применялись вертикальные и горизонтальные подъемники (вороты) с ручным приводом (рисунок 3).
Рисунок 3. Вертикальный и горизонтальный подъемник с ручным приводом
Согласно записям в России применялись различного рода подъемные средства. Например, Царь-колокол, который составлял массой 130 тонн подняли в Кремле Московии в VII веке. Поднимая его использовали различные приспособления (рычаги, противовесы, лебедки).
Рисунок 4. Подъем Царь-колокола
Использовали в те времена различного рода энергию для подъемного оборудования. В VXIII веке – это была сила воды, то есть водяное колесо, а так же использовали тягу человека и животного.
Удивительным фактом являлась установка цоколя памятника Петру I, которая была осуществлена в 1769 году. Материал который использовали для этого сооружения составлял массой 1000 пудов, его транспортировали к объекту строительства при использовании следующих подъемных средств: лебедки, полисмпастов и катков огромного диаметром расстояния.
Рисунок 5. Воздвижение Цоколя Петру I
В России до периода революции на Костромском механическом заводе было было внедрено и производилось в производство подъемных кранов.
В конце XIX века многие крупные машиностроительные заводы России производили выпуск подъемного оборудования Сормовский, Брянский, Путиловский и Коломенский заводы-изготовители
Техническая оснащенность предприятий автосервиса является неотъемлемой частью наличия подъемного оборудования.
В настоящее время используют четыре вида привода подъемного оборудования автомобилей при техобслуживании и ремонте.
Далее пойдет речь о этих видах привода подъемного оборудования
Это оборудование, как известно, может быть трех типов − с электро-, гидро- и пневмоприводом. Причем каждый из них обладает своими достоинствами и недостатками (табл. 1). Кроме того, может быть подвижным и стационарным. Наконец, одно-, двух- и даже многостоечными. В связи с этим возникает вопрос: какому из типов отдавать предпочтение?
Таблица 1.
Типы привода подъемного оборудования
Сравниваемый показатель |
Тип привода подъемника |
||
электрический |
гидравлический |
пневматический |
|
Возможность работы в области больших нагрузок |
− |
+ |
− |
Возможность работы при больших скоростях подъема и спускания автомобиля |
− |
+ |
+ |
Возможность дистанционного управления |
+ |
− |
− |
Способность запасать (аккумулировать) энергию |
− |
+ |
+ |
Стоимость |
+ |
− |
− |
Массогабаритные размеры |
+ |
− |
− |
Пожаро- и взрывобезопасность |
− |
+ |
− |
Экологичность |
− |
− |
+ |
Ремонтопригодность |
+ |
− |
− |
Фиксация автомобиля в поднятом состоянии |
+ |
− |
− |
Начнем с того, что подавляющее большинство выпускаемых подъемников − двухстоечные стационарные. Они, по сравнению, с передвижными обладают тем преимуществом, что обеспечивают большую устойчивость поднятого автомобиля и тем самым повышают безопасность и удобство выполнения работ исполнителем. Тем не менее передвижные подъемники также находят применение, поскольку не требуют выполнения монтажно-установочных работ и устройства фундамента, позволяют использовать их на любой ровной площадке, в том числе и вне помещений. После выполнения работ такие подъемники могут быть удалены с занимаемого ими места, которые потом используются для других работ или оборудования. Маневренность передвижных подъемников позволяет при необходимости изменить технологический маршрут ТО и ТР автомобилей, что нередко используется на малых СТОА или в стесненных производственных площадей [1].
Одностоечные подъемники тоже вполне применимы, так как обладают рядом несомненных достоинств.
Во-первых, такой подъемник дает исполнителю большую, чем, скажем, двухстоечный подъемник, свободу передвижения вокруг автомобиля, обеспечивает свободный доступ к нижним его частям. Во-вторых, автомобиль очень легко въезжает на такой подъемник. В-третьих, для одностоечного подъемника не требуется специального фундамента, значит, он дешевле двух- и многостоечного.
Однако у одностоечного подъемника есть два существенных недостатка: сила F веса (подъема) автомобиля прикладывается к одной стойке, что заставляет делать ее довольно массивной и стабилизации автомобиля на нем (в одной точке) всегда менее надежна, чем на двухстоечном подъемнике. Значит, и ниже уровень безопасности работ. Поэтому предприятия автосервиса отдают предпочтение подъемникам двухстоечным.
Теперь обратимся к табл. 1, что позволит сориентироваться в достоинствах и недостатках электро-, гидро- и пневпомодъемников.
Как видим, каждый из приводов действительно имеет свои преимущества и недостатки. Поэтому в настоящее время большинство малых СТОА оснащаются подъемниками с электромеханическим приводом: они дешевле.
Модернизация заключается в снижении грузоподъемности двухстоечного стационарного подъемника с 30 до 20 кН, что позволяет уменьшить высоту профиля балок подхвата и, в итоге позволяет уменьшить минимальную высоту клиренса автомобилей заезжающих на обслуживание, что особенно важно для легковых автомобилей.
В ходе модернизации определяем силы и моменты возникающие в приводе при работе подъемника с целью подбора оптимального по энергопотреблению электродвигателя, а также производим расчет силовых элементов подхватов.
Все начинается с подбора электродвигателя – первый этап.
Определим крутящий момент потребный для вращения грузового винта по формуле №1 при максимальной нагрузке в соответствии с методикой [1, с 25–34]. Далее определяется тангенс угла по формуле №2. Для однозаходной резьбы формула №3. Вертикальная осевая нагрузка на грузовой винт определяется по зависимости №4. Определим потребный крутящий момент электродвигателя формула №5. Определим частоту вращения грузового винта по формуле №6. Определяем частоту вращения вала двигателя по формуле № 7. Определяем потребную мощность двигателя по формуле №8. Согласно ГОСТ 19523-81 выбираем электродвигатель мощностью N ≥ Nэд с частотой вращения вала близкой к n'. Данным требованиям удовлетворяет асинхронный двигатель 4А100L6 мощностью N = 2,2 кВт и частотой вращения вала nдв = 950 мин-1.
Следующий этап расчет балки выдвижной
Расчет производим в соответствии с методикой [2, с 67–83].
Материал изготовления сталь 45. Расчет сечения короба балки производим из условия прочности на изгиб по формуле №9. Крутящий момент на изгиб определяется по формуле №10.
Предполагаем, что масса, приходящаяся на ведущую ось поднимаемого автомобиля составляет 60% от общей массы. Тогда осевую нагрузку принимаем из условия №11.
Расчет винта опорного.
Расчет производим в соответствии с методикой [1, с 25–34]. Средний диаметр резьбы d2 винта из условия на сжатие формула № 12. По справочнику принимаются параметры резьбы грузового винта, средний диаметр которой имеет ближайшее большее значение к расчетному. Выбираем резьбу со следующими параметрами: тип - однозаходная, трапецеидальная (ГОСТ 9894-73), угол профиля 30о, угол наклона рабочей грани профиля γ = 15о; диаметр средний d2=14 мм, диаметр наружный d=16 мм, диаметр внутренний d1=11,5 мм, шаг резьбы S=4 мм
Расчет гайки направляющей Расчет производим в соответствии с методикой [1, с 25–34].
Материалом для изготовления направляющей гайки выбираем сталь 45.
Параметры резьбы гайки принимаем: диаметр наружный d'=16,5 мм, диаметр внутренний d'1=12 мм.
Определяем минимальное число витков, находящихся в зацеплении
В предположении равномерного распределения нагрузки по виткам, число витков гайки определяется из условия прочности витков на срез по формуле №13.
Тогда по формуле №14 определим Z. Определение наружного диаметра гайки.
Наружный диаметр гайки D определяется из условия прочности гайки на растяжение силой Fx по формуле №15. Диаметр определим по формуле №16. Минимальная толщина стенки должна составлять не менее 5 мм. Тогда принимаем наружный диаметр гайки направляющей D1 = 30 мм. Высоту гайки принимаем равной высоте короба балки выдвижной – H = 50 мм.
Следующий этап расчет балки поворотной
Расчет производим в соответствии с методикой [2, с 67–83]. Произведем расчет короба балки поворотной. Материал изготовления сталь 45. Расчет сечения производим из условия прочности на изгиб по формуле №17. Крутящий момент на изгиб определяется по формуле № 18.
Следующий этап расчет оси
Материал изготовления сталь 45.
Расчет производим в соответствии с методикой [2, с 67–83]
В оси изгибающий момент Миз вызывает деформацию сдвига (среза) по двум плоскостям и деформацию смятия. Обычно сопротивление стали деформации сдвига ниже, чем среза. Поэтому, последней пренебрегают и ось рассчитывают только на срез.
Из условия прочности на срез имеем формула №19. Сила на срез определяется по формуле № 20. Момент на изгиб определяется по зависимости №21. Сила на срез определяется по формуле №21.
Расчет плиты опорной балки поворотной
Расчет производим в соответствии с методикой [2, с 67–83]
Материал изготовления сталь 45.
В плите сила растяжения Fр, возникающая от действия изгибающего момента – вызывает деформацию растяжения.
Из условия прочности на растяжение имеем №22.
Наиболее опасным сечением плиты является сечение, проходящее через центр отверстия, предназначенного для установки поворотной оси. Сила растяжения возникающая в данном сечении равна силе среза оси Fр = Fср.
Таблица 2.
Модернизация двухсточного стационарного подъемника
№ фор- мулы |
Формула |
Примечания |
1 |
|
Fх – вертикальная осевая нагрузка на грузовой винт; d – средний диаметр резьбы грузового винта. В соответствии с паспортными данными подъемника П-157 /10/ d = 39 мм; ηпк – КПД опорных подшипников качения. ηпк =0,99; ψ - угол подъема винтовой линии; ρ – приведенный угол трения |
2 |
|
d – средний диаметр резьбы грузового винта; ρ - приведенный угол трения |
3 |
|
f – коэффициент трения. Для пары трения сталь-бронза f = 0,1;
|
4 |
|
Fmax – грузоподъемность одной стойки. Gк – масса каретки и подхватов подъемника. |
5 |
|
ηцп=0,92 – кпд цепной передачи; ηцп=0,95 – кпд ременной передачи |
6 |
|
V – скорость перемещения каретки; P – шаг резьбы. |
7 |
|
u – передаточное число ременной передачи. Принимаем параметры ременной передачи подъемника-прототипа, тогда u = 3,6 |
8 |
|
- |
9 |
|
Миз – изгибающий момент, действующий в сечении балки; W – осевой момент сопротивления сечения. [σи] – предел прочности материала трубы на изгиб. Для стали 45 [σи]=170 МПа |
10 |
|
Fmax' – осевая нагрузка, действующая на винт; l – расстояние от оси приложения нагрузки до наиболее нагруженного сечения. |
11 |
|
Fmax – грузоподъемность подъемника, H |
12 |
d2 = |
[σ]сж – предел прочности материала винта на сжатие; Для стали 45 [ |
13 |
|
Кр – коэффициент полноты резьбы. Для трапецеидальной резьбы Кр=0,4; [τср] – допускаемое напряжение среза материала витков гайки. Для стали 45 [τср]= 150 МПа. |
14 |
|
- |
15 |
|
к=1 – коэффициент, учитывающий скручивание гайки; [σр] – допускаемое напряжение на растяжение материала гайки. Для стали 45 [σр]=170 МПа |
16 |
|
- |
17 |
|
- |
18 |
|
l – расстояние от оси приложения нагрузки до наиболее нагруженного сечения трубчатой части балки |
19 |
|
Fср – сила среза; d – диаметр оси. [τср] – допускаемое напряжение среза материала витков гайки. Для стали 45 [τср]= 150 МПа |
20 |
|
e – плечо максимального действия силы относительно освой линии балки поворотной. l = 45 мм |
21 |
|
l – максимальное расстояние от оси балки поворотной до оси приложения нагрузки |
22 |
|
Fр – сила растяжения; [σр] =170 МПа – предел прочности материала на растяжение; Sсеч – площадь поперечного сечения плиты в наиболее опасном сечении. |
