Современная концепция управления качеством жизненного цикла наукоемкой продукции
Конференция: VII Международная заочная научно-практическая конференция «Научный форум: экономика и менеджмент»
Секция: Менеджмент
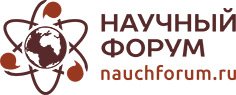
VII Международная заочная научно-практическая конференция «Научный форум: экономика и менеджмент»
Современная концепция управления качеством жизненного цикла наукоемкой продукции
The modern concept of quality management of life cycle of high technology products
Julia Reshetnikova
specialist, JSC Moscow Mechanical Engineering Plant AVANGARD, Russia, Moscow
Аннотация. Статья посвящена исследованию существующих систем управления качеством ЖЦ наукоемкой продукции в России с целью разработки приоритетной концепции управления качеством ЖЦ наукоемкой продукции, отвечающей современным требованиям и способствующей повышению конкурентоспособности изделий.
Abstract. The article is devoted to the existing systems of quality management of life cycle of high technology products in Russia with the aim of developing a priority of the concept of quality management of the life cycle of high-tech products that meet modern requirements and contribute to improving the competitiveness of products.
Ключевые слова: управление качеством, НИОКР, жизненный цикл изделия, н СМК, цикл качества, конкурентоспособность изделия, реинжиниринг процессов, бизнес-роль, система сбалансированных показателей.
Keywords: quality management, scientific research, the life cycle of products, reengineering processes, business role, Balanced scorecard.
В современных условиях приоритетным направлением для промышленного предприятия является повышения конкурентоспособности выпускаемой продукции, которое не может быть достигнуто без эффективного управления качеством продукции, являющегося лидирующим направлением функционирования промышленного предприятия.
Согласно ГОСТ Р 52104-2003 «Ресурсосбережение. Термины и определения» конкурентоспособность продукции – это предположительная рыночная характеристика продукции, определяемая как привлекательность, выражаемая в потенциальной возможности товара удовлетворять требованиям конкретного покупателя по показателям качества, экологичности, безопасности, ресурсопотребления и затратам на приобретение данного товара. При оценке конкурентоспособности изделия может быть использована модель, включающая стратегические аспекты, выражаемые в баллах через эмпирическое соотношение:
(1)
Согласно представленной формуле, увеличение показателя качества способствует повышению конкурентоспособности изделия.
Согласно данным всемирно-экономического форума в рейтинге глобальной конкурентоспособности за 2016–2017 г. Россия в сравнении с 2015 г. поднялась на 2 позиции и занимает 43 место. Рассматривая машиностроительную отрасль, согласно данным Минэкономразвития за 2011–2015 гг., наблюдается отрицательная тенденция снижения динамики промышленного производства, структура машиностроительного комплекса за 2011–2015 гг. представлена на рисунке 1.
Рисунок 1. Структура объема отгруженных товаров собственного производства машиностроительного комплекса
Согласно данным, представленных на рисунке 1, наблюдается отрицательная тенденция снижения доли производства машин и оборудования за 2009–2015 гг. на 9 %, и положительная тенденция роста производства транспортных средств и оборудования на 5,7% и производства электрооборудования на 3,4 %. Снижение доли производства машин и оборудования обусловлена затруднительным доступом страны к зарубежным технологиям, нехваткой финансовых ресурсов на проведение НИОКР.
Рисунок 2. Инновационная активность организаций России за 2010–2015 гг.
Анализ данных, представленных на рисунке 2, показывает, что наблюдается отрицательная тенденция снижения инновационной активности организаций в 2015 г. в сравнении с 2014 г. на 0,6% и снижение удельного веса инноваций на 0,3 %, следствием которого является снижение эффективности управления.
В государственной программе РФ «Развитие промышленности и повышение ее конкурентоспособности» утвержденной 15 апреля 2014 № 328 для машиностроения стоит задача повышения конкурентоспособности изделий путем стимулирования инновационного развития отрасли и инвестиций в научно-исследовательские и опытно-конструкторские работы.
В связи с поставленной задачей следует отметить важность совершенствования управления СМК в области научно-исследовательских и опытно-конструкторских работ (НИОКР) как этапа жизненного цикла наукоемкого изделия. Выполнение требований заказчика и удовлетворение его потребностей за счет выпускаемой продукции должно также сопровождаться непрерывным контролем функционирования каждого этапа жизненного цикла продукции, поскольку поэтапный контроль соответствия установленным требованиям позволяет обеспечить выпуск качественной продукции, обеспечивающий эксплуатацию изделия с требуемыми показателями надежности, следовательно, повышение качества должно сопровождаться сокращением производственного цикла, снижением затрат на изготовление и эксплуатацию изделия [4].
С целью развития системы менеджмента качества в России были разработаны системы управления качеством, представленные в таблице 1.
Таблица 1.
Характеристика российских систем управления качеством
№ |
Наименование системы управления качества |
Описание |
Основной критерий эффективности |
---|---|---|---|
1 |
Система бездефектного изготовления продукции (БИП) (1995 г. Саратовский авиационный завод) |
Создание условий производства, обеспечивающих изготовление изделий без отступлений от технической документации. |
Процент сдачи продукции с первого предъявления |
2 |
Система бездефектного труда (1950–1960 г.г. г.Львов) |
Обеспечение выпуска продукции отличного качества путем стимулирования каждого работника предприятия. |
Коэффициент качества труда |
3 |
Система КАНАРСПИ (1958 г. г.Нижний Новгород) |
Управление качеством на стадии изготовления продукции, система же КАНАРСПИ - на то, чтобы уже в процессе проектирования и технологической подготовки производства обеспечить изготовление надежных и высококачественных изделий. |
Показатели надежности |
4 |
Система НОРМ (1963 г. г.Ярославль) |
Комплексный подход к управлению качеством на стадиях проектирования, изготовления и эксплуатации двигателей. |
Наработка в часах до первого капитального ремонта |
5 |
Система КС УКП (1978 г. Госстандарт) |
Совокупность мероприятий, методов и средств, при помощи которых целенаправленно устанавливается, обеспечивается, поддерживается на основных стадиях жизненного цикла (планирование, разработка, производство, эксплуатация или потребление) уровень качества продукции, соответствующий потребностям народного хозяйства и населения. |
Уровень качества продукции, соответствующий потребностям народного хозяйства и населения. |
Согласно таблице 1 для управления качеством ЖЦИ применима система КАНАРСПИ, которая предусматривает управление качеством на стадии производства и обеспечение качества на этапе проектирования, в настоящее время существует основанная на этой системе концепция КАНАРСПИ 21 века, предусматривающая управление ЖЦИ Качеством, Надежностью, Ресурсом с первых изделий) [2], основанная на применении системного подхода к управлению качеством.
Согласно ГОСТ Р 57189-2016 «Системы менеджмента качества-Руководство по применению ИСО 9001:2015» СМК включает процессы деятельности (предназначенные для производства продукции) и процессы системы (проведение внутреннего аудита и анализа со стороны руководства). В свою очередь любой процесс представляет собой последовательность операций, элементов или подпроцессов.
В качестве процессов деятельности выступаю процессы, необходимые для реализации этапов ЖЦ изделия, к ним относятся:
· основные процессы (в качестве основного процесса выступает производство продукции или оказание услуги);
· вспомогательные процессы (ориентированы на обеспечение функционирования основных процессов);
· управленческие процессы (планирование деятельности и организация производства);
· процессы – сети, обеспечивающие взаимодействие с потребителем и поставщиками.
В качестве процессов системы выступает цикл качества (планирование, реализация, контроль, устранение причин отклонений в качестве (корректирование), схематично отображенное на рисунке 3 с использованием процессного подхода.
Согласно данным, представленных на рисунке 3, управление качеством осуществляется на всех этапах ЖЦИ путем планирования качества согласно требованиям заказчика, анализу показателей надежности.
Рисунок 3. Управление качеством продукции ЖЦИ с использованием цикла качества
Согласно представленной схеме процесса ЖЦИ на этапе НИОКР формируется задание на изделие согласно полученным в ходе маркетинговых исследований данным и требованиям заказчика, на выходе этапа 1 имеются требования заказчика, которые на этапе 3 (проектирование) необходимы для идентификации части изделия, проектирования техпроцессов. На выходе этапа 3 появляется план по качеству, который является входным ресурсом для планирования производства. На выходе этапа 4 «Планирование производства» имеем план по качеству и листы контроля качества техпроцессов. В процессе производства (этап 5) происходит контроль качества техпроцессов установленным требованиям и устранение выявленных несоответствий, на выходе (этапа 5) имеем информацию о фактическом качестве и сопоставляем фактические данные с плановыми показателями. На схеме указаны действия цикла качества (планирование (этапы ЖЦИ №1, №2, №3), действие (этапы ЖЦИ №3,4,5,6), контроль (этапы № 5, №6), корректирование (на всех этапах ЖЦИ по мере выявления несоответствий требованиям плана по качеству). На этапе эксплуатация (этап №6) осуществляется повторение цикла качества в случае выявления несоответствий, которые необходимо учитывать на этапе НИОКР для предотвращения повторения их возникновения в ходе эксплуатации. Система отслеживания несоответствий должна быть четко отлаженной, т.к. производимые в ходе эксплуатации корректирующие действия значительно снижают длительность этапа эксплуатации, т.к. требуется время на разработку мероприятий по устранению скрытых несоответствий (скрытых дефектов). Выявление скрытых дефектов в ходе эксплуатации неизбежно приведет:
· к разработке мероприятий по их устранению производителем, что потребует дополнительное время и сокращения ЖЦИ на этапе эксплуатации,
· снижению показателей надежности, следствием которого является снижение конкурентоспособности изделия,
· увеличение затрат заказчика на техническое обслуживание и ремонт изделия.
С целью предотвращения вышеперечисленных проблем предлагается концепция управления СМК ЖЦИ, основанием которой служит выполнение цикла качества на всем ЖЦИ и на каждом этапе в отдельности согласно ГОСТ Р ИСО 9001-2015 «Система менеджмента качества. Требования» и интеграцию системного и процессного подходов (КАНАРСПИ 21). Реализация современной концепции управления СМК включает основные этапы:
1. Определить состав процессов в предприятии исходя из идентификации процессов, используя информацию о характеристике продукции, используя показатели качества: технико-эксплуатационные, нормативно-правовые, экономичности исполнения, и распределить процессы по этапам ЖЦИ.
2. Определить бизнес-роли (назначить ответственных за функционирование процессов), используя правило «один процесс – одно подразделение – один бюджет – один руководитель процесса» [4].
3. Определить «входы» (материальные ресурсы, информация) и «выходы» (продукция и информация) процессов. При идентификации процессов необходимо уточнить обязанности бизнес-ролей, этапы и взаимосвязи в процессах.
4. Определить ресурсы процессов: персонала, оборудования и технологических материалов, технологий и методик, средств измерений и т. д.
5. Определить показатели процесса, которые характеризуют выполнение требований стандарта ISO 9001, выполнение стандартов предприятия.
Наиболее важным этапом является определение бизнес-роли, ответственного за процесс, ввиду возникновения конфликта между процессным подходом и функциональным управлением. В рамках процессного подхода каждая бизнес-роль кроме ответственности за функционирование управляемого подразделения, владелец процесса также несет ответственность за результативность процесса. Владелец процесса должен системно управлять своим процессом, выявлять и устранять недостатки в функционировании в рамках своего процесса для обеспечения выхода качественного продукта процесса. Для обеспечения функционирования СМК в соответствии с современными требованиями необходимо проведение реинжиниринга процессов и сопровождения функционирования системы сбалансированных показателей (BSC) Balanced Scorecard [3], основанной на доведении до персонала стратегических целей и задач предприятия, способной обеспечить повышение и поддержание конкурентоспособности продукции в современных условиях.
Список литературы:
