ДВУХУРОВНЕВЫЙ МЕХАНИЧЕСКИЙ АНАЛИЗ ЭЛЕКТРОННОГО ОБОРУДОВАНИЯ
Конференция: LXXV Международная научно-практическая конференция «Научный форум: технические и физико-математические науки»
Секция: Технология материалов и изделий текстильной и легкой промышленности
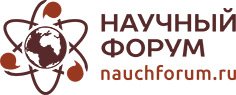
LXXV Международная научно-практическая конференция «Научный форум: технические и физико-математические науки»
ДВУХУРОВНЕВЫЙ МЕХАНИЧЕСКИЙ АНАЛИЗ ЭЛЕКТРОННОГО ОБОРУДОВАНИЯ
Аннотация. В статье представлены исследования математического моделирования электронного оборудования и эффективного метода выполнения широкого спектра задач механического анализа (статическое ускорение, вибрации, удары). Данная модель и метод позволяют с достаточной точностью получить требуемые механические характеристики деформированных конструкций для всех собираемых элементов (включая шасси, печатные платы и электронные компоненты). Модель совместима с вычислительным оборудованием класса рабочей станции. Основная задача анализа разделена на два уровня: задача верхнего уровня для шасси и печатных плат с упрощенными компонентными моделями и несколько задач нижнего уровня для отдельных компонентных моделей. Нижнеуровневые задачи используют результаты верхнеуровневых задач в качестве граничных условий и условий нагрузки. Такая методика расчета позволяет решать задачи нижнего уровня только для наиболее деформированных компонентов и значительно экономить время, пропуская другие. В статье также рассматривается способ установления граничных условий и условий нагрузки для задач нижнего уровня и критерии необходимости проведения анализа нижнего уровня для отдельных компонентов.
Abstract. The article presents studies of mathematical modeling of electronic equipment and an effective method for performing a wide range of tasks of mechanical analysis (static acceleration, vibrations, shocks). This model and method make it possible to obtain with sufficient accuracy the required mechanical characteristics of deformed structures for all assembled elements (including chassis, printed circuit boards and electronic components). The model is compatible with workstation-class computing equipment. The main task of the analysis is divided into two levels: an upper-level task for chassis and printed circuit boards with simplified component models and several lower-level tasks for individual component models. Lower-level tasks use the results of upper-level tasks as boundary conditions and load conditions. This method of calculation allows us to solve lower-level problems only for the most degraded components and significantly save time by skipping others. The article also discusses a way to establish boundary conditions and load conditions for lower-level tasks and criteria for the need for a lower-level analysis for individual components.
Ключевые слова: бортовое электронное оборудование; механическая надежность; Метод конечных элементов (МКЭ).
Keywords: on-board electronic equipment; mechanical reliability; Finite element method (FEM).
I. ВВЕДЕНИЕ
Процесс создания новых образцов технического оборудования включает в себя различные этапы: проектирование, инженерно-конструкторские разработки и экспериментальные испытания различных узлов и агрегатов в целом.
Электронное оборудование авиакосмического и военного назначения отличается высокой сложностью и жесткими требованиями к надежности. Поэтому расходы, связанные с тестированием, становятся намного выше, чем расходы на проектирование.
Совершенствование инструментов моделирования физических процессов позволяет решать различные задачи надежности, начиная с экспериментального уровня и заканчивая проектным. Это позволяет сократить время разработки и сократить общие расходы. В то же время механическое моделирование поведения детализированной модели требует высокой вычислительной мощности. Таким образом, задача нахождения подходящей методики для быстрого расчета параметров механической надежности остается актуальной.
В настоящее время мы располагаем различными методами расчета и программными продуктами для моделирования таких механических нагрузок, как статическое ускорение и смещение, гармонические и широкополосные вибрации, удары. Возможность их использования с минимальными корректировками вместо разработки и внедрения новых методов и программного обеспечения для решения всей задачи [1,2]. Например, Метод конечных элементов (МКЭ) реализуется в следующих случаях.
II. ДВУХУРАВНЕВЫЙ ПОДХОД
A. Основные допущения
Решение статического случая нагрузки в составе конечных элементов сводится к построению матрикс жесткости, ее инверсии и расчету узловых перемещений и вращений для каждого элемента. Для случаев динамических нагрузок часто используемые методы основаны на сочетании собственных режимов.
Использование детальной геометрии для всех компонентов в модели устройства требует высокой вычислительной мощности и представляется не очень эффективным. С другой стороны, использование упрощенных моделей не позволяет с достаточной точностью рассчитать их механические параметры надежности. В этом контексте естественным путем является разделение основной вычислительной задачи на подуровни: уровень несущей структуры, состоящей из шасси и печатных плат и компонентный уровень. Целесообразно использовать прототипы компонентов, максимально упрощенные на верхнем уровне анализа, а на нижнем уровне - детализированные.
Существует два основных предположения о природе взаимного влияния между этими двумя уровнями в обсуждаемом методе:
1) Предполагается, что на верхнем уровне (шасси и печатные платы) роль электронного компонента заключается в повышении жесткости и массы соответствующей области печатной платы.
2) Предположение для нижнего уровня заключается в том, что напряженно-деформированное состояние электронной компоненты как в случае статической, так и динамической нагрузки определяется не ее собственными режимами, а деформацией печатной платы и эквивалентным статическим ускорением.
Первое предположение подтверждается хорошим согласием результатов моделирования и экспериментальных данных, где в модели прибора были использованы прототипы плоских и массовых компонентов [3-6].
B. Граничные условия
Для подтверждения второго предположения и выбора наилучшего способа задания граничных условий и условий нагрузки на нижнем уровне был проведен следующий численный эксперимент.
В анализе нижнего уровня использовалась подробная геометрия детали (рис. 1). Корпус компонента был склеен гибкими контактами, где к печатной плате припаивалась часть размером 30 × 30 мм. Эталонная модель имела идентичную структуру и была интегрирована непосредственно в верхний уровень КЭ-модели. Таким образом, для эталонной модели перенос граничных условий не требовался. Гармоническая вибрационная нагрузка с ускорением 25 G была смоделирована на высоком уровне. Статический анализ с эквивалентным ускорением проводился на нижнем уровне.
Рисунок 1. Геометрия нижнего уровня КЭ-модель
Были сопоставлены четыре случая:
1 - анализ исходного верхнего уровня;
2 - анализ нижнего уровня с узловым смещением и передачей данных вращения по краям модели печатной платы;
3 - анализ нижнего уровня с переносом данных о смещении и вращении узлов на всю область модели печатной платы;
4 - анализ нижнего уровня с смещением узлов, и передача данных о вращении в область контакта печатной платы с компонентом.
Результаты расчетов показывают, что наилучшим согласованием с эталонным случаем является анализ нижнего уровня, при котором передача пограничных данных осуществляется по краям модели печатной платы. Таким образом, можно получить 0,4% отклонение от референтных результатов. Другие варианты передачи граничных условий приводят к значительным ошибкам при расчете механических напряжений (рис. 2 и 3).
Рисунок 2. Максимальные значения напряжений в паяльных соединениях
Рисунок 3. Максимальное значение напряжений в гибких контактах
Эта ситуация связана с ошибками, возникающими при интерполяции данных от грубой к тонкой сетке. Во втором случае ошибки интерполяции применяются на границе локальной модели печатной платы и сглаживаются в области крепления компонентов. В третьем и четвертом случаях те же ошибки применяются непосредственно к монтажной поверхности детали.
C. Расчет экономии времени и ресурсов
Задача подтверждения механической надежности электронного устройства не обязательно требует расчета параметров напряженно-деформированного состояния всех его компонентов на нижнем уровне. В большинстве случаев необходимый вывод можно сделать на самом высоком уровне, проанализировав напряженно-деформированное состояние модели печатной платы и параметры реакции. Можно использовать следующие критерии:
- an – нормальное ускорение на поверхности крепления;;
- aτ – касательное ускорение на поверхности крепления;
- kb – некоторые характеристики изгиба поверхности крепления..
Значения an и aτ могут быть получены непосредственно из результатов анализа верхнего уровня. Параметр kb может быть принят за разницу между углами вращения узловой поверхности крепления. В случае, если элементы модели печатной платы не поддерживают степень свободы вращения, вторая пространственная производная узловых перемещений может быть приблизительно оценена.
Методика подтверждения механической надежности электронного устройства состоит из следующих этапов:
a) Построены компонентные модели нижнего уровня для статического анализа и рассчитаны критерии an, a, kb. Эти модели и значения критериев сохраняются для дальнейшего использования.
b) Построена модель устройства верхнего уровня и решены все необходимые задачи анализа.
c) Для каждой задачи анализа верхнего уровня рассчитываются параметры an, aτ, kb на площадях крепления компонентов для принятия решения о необходимости проведения анализа нижнего уровня.
d) Для получения более точной оценки надежности при необходимости выполняются задачи анализа нижнего уровня.
Такая методика расчета позволяет решать задачи нижнего уровня только для наиболее деформированных деталей и значительно экономить время, пропуская "безопасные".
III. МЕТОДИКА ПРИМЕНЕНИЯ
A. Автоматизация задач предварительной/последующей обработки
Кроме того, еще одним ресурсом экономии времени является автоматизация задач пре/постобработки. Программный модуль ANSYS® Mechanical APDL™ позволяет осуществлять взаимодействие в пакетном режиме, которое используется для автоматизации. Внешний вариант программного обеспечения для автоматизации показан ниже (рис. 4).
Рисунок 4. Внешний вид программного обеспечения для автоматизации предварительной/ последующей обработки
Данное программное обеспечение имеет пользовательский интерфейс, который настраивается специально для целей электронного проектирования. Это минимизирует прямое взаимодействие с базовым решающим устройством. База данных программного обеспечения включает в себя FE-шаблоны для элементов шасси, печатных плат и электронных компонентов. Реализованы все необходимые инструменты для импорта геометрии CAD и создания новых КЭ-шаблонов.
Для оценки времени, необходимого для полного цикла механического анализа, см. таблицу ниже (Таблица 1). Все указанные значения были измерены на компьютере платформы Intel Core i7 950 3,06 ГГц. Поскольку все аналитические критерии нижнего уровня хранятся в прикладной базе данных, соответствующие задачи могут быть также автоматизированы.
B. Составление модели верхнего уровня
Для упрощения процесса построения модели верхнего уровня из числа простейших шаблонов используется следующая методика:
a) Каждый шаблон имеет специальные узлы или группы элементов, которые определяются на этапе создания шаблона. Для ANSYS® Mechanical APDL™ модуля эти группы называются "компонентами". Само название группы состоит из типа связи и номера счета (например “parents_1”, “childs_3”, “siblings_10”). Таким образом, это имя отражает шаблонные отношения в иерархии моделей. В случае, если все дети установлены на одной и той же поверхности, то родительский шаблон может иметь только одну группу "childs_", которая покрывает эту поверхность.
b) Для каждого уровня иерархии модели сначала загружается родительский шаблон. Затем все его дети загружаются и подключаются с помощью предопределенных групп "родительские_" и "childs_". Также создаются контакты для групп "siblings_" в дочерних шаблонах.
c) На верхнем уровне иерархии моделей граничные условия и условия нагрузки применяются к соответствующим названным группам (например, "фиксированный_1", "Force_3", "preassure_10").
Такая методика позволяет унифицировать структуру шаблона и варьировать его сложность без изменения основного алгоритма построения (рис. 5).
Рисунок 5. Пример комбинирования шаблонов различной сложности
C. Проверка и корректировка модели.
Основной метод верификации модели заключается в сравнении полученных результатов с экспериментальными данными. При этом необходимо учитывать, что профиль нагрузки не идеален. Таким образом, необходимо использовать данные таблицы эталонного датчика. Другой способ манипулировать моделью и регулировать ее.
Построение точной модели для нового электронного компонента от 600 до 1800 характеристик без перестройки структуры КЭ приводит к изменению структуры слоя печатной платы. В терминах КЭ-модуля определение многослойного сечения должно быть изменено. Реальное изображение схемы в большинстве случаев не нужно размещать на печатной плате. Толщина соответствующих слоев может быть изменена. Сочетание этих двух методов позволяет достичь хорошего согласия расчетных и экспериментальных данных (рис. 6).
Рисунок 6. Результаты испытаний на гармонические колебания
ЗАКЛЮЧЕНИЕ
Все вышеперечисленные методы позволяют инженерам создавать прибор КЭ-модель, которая может быть использована на всех стадиях проектирования и разработки. На уровне царапин можно проанализировать механическую надежность различных схем шасси. Затем можно протестировать различные схемы печатных плат, чтобы избежать потенциальных конфликтов функциональной и механической надежности
Использование КЭ-шаблонов позволяет вносить необходимые изменения в основную топ-модель с минимальными временными и трудовыми затратами. Компонентные КЭ-шаблоны могут быть использованы для механического анализа других электронных устройств и не нуждаются в повторной сборке.
Наконец, КЭ-модель прибора может быть использована в обоих направлениях:
a) определить оптимальные места установки аппаратуры наблюдения испытательного оборудования (до проверки и регулировки модели);
b) предсказать поведение устройства в условиях нагрузки, которые не могут быть заданы испытательным оборудованием (после проверки и регулировки модели).
