МОРФОЛОГИЧЕСКИЕ ХАРАКТЕРИСТИКИ И ХИМИЧЕСКИЙ СОСТАВ ЭЛЕКТРООСАЖДЕННОГО КРЕМНИЯ
Конференция: LXXX Международная научно-практическая конференция «Научный форум: технические и физико-математические науки»
Секция: Химическая технология
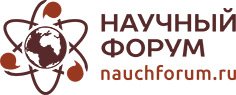
LXXX Международная научно-практическая конференция «Научный форум: технические и физико-математические науки»
МОРФОЛОГИЧЕСКИЕ ХАРАКТЕРИСТИКИ И ХИМИЧЕСКИЙ СОСТАВ ЭЛЕКТРООСАЖДЕННОГО КРЕМНИЯ
MORPHOLOGICAL CHARACTERISTICS AND CHEMICAL COMPOSITION OF ELECTRODEPOSITED SILICON
Aleksei Trofimov
Junior Researcher, Ural Federal University, Russia, Ekaterinburg
Ekaterina Starkova
Research engineer, Ural Federal University, Russia, Ekaterinburg
Ekaterina Zyryanova
Research engineer, Ural Federal University, Russia, Ekaterinburg
Аннотация. В работе представлены результаты исследования морфологических свойств и состава кремния, полученного методом электрохимического осаждения из расплавленных солей KCl-K2SiF6-SiO2, а также влияние последующей обработки с использованием планетарной мельницы на примесный состав. Электроосаждение позволяет варьировать форму и размер частиц в диапазоне от 160 до 340 нм. Для получения наименьшего диаметра частиц необходимо использовать расплав без добавления SiO2.
Abstract. The paper presents the results of a study of the morphological properties and composition of silicon obtained by electrochemical deposition from molten salts KCl-K2SiF6-SiO2. The results of subsequent processing using a planetary mill on the impurity composition are presented. Electrodeposition allows varying the shape and size of particles in the range from 160 to 340 nm. To obtain the smallest particle diameter, it is necessary to use a melt without adding SiO2.
Ключевые слова: кремний, электроосаждение, волокна, иглы, морфология.
Keywords: silicon, electrodeposition, wires, needles, morphology.
Введение
Кремний (Si) является одним из наиболее перспективных материалов для применения в анодах литий-ионных аккумуляторов (ЛИА) благодаря своей высокой емкости (4200 мАч/г) [2], что в десять раз превосходит ёмкость традиционных графитовых анодов. Однако, использование кремния в коммерческих батареях ограничено рядом проблем, связанных с его низкой проводимостью, высоким коэффициентом расширения при литировании (до 400%) и вызванным этим разрушением его структуры в процессе циклирования.
Исследования показывают, что основной проблемой является именно механическая неустойчивость структуры кремниевых анодов при циклах зарядки и разрядки. При интеркаляции лития кремний увеличивается в размерах, что приводит к образованию трещин и потере электрического контакта между активным материалом и электродом, что, в свою очередь, снижает эффективность и емкостные характеристики аккумулятора. Современные подходы к решению данных проблем включают использование наноструктурированных форм кремния, композитных материалов [4], а также добавление полимерных связующих для улучшения механической прочности анодов. Одним из способов получения кремния субмикронных размеров является электроосаждение из расплавленных солей [1].
В данной статье представлено исследование морфологических свойств и химического состава кремния, полученного методом электрохимического осаждения из расплавленных солей, а также влияние последующей обработки с использованием планетарной мельницы на химический состав.
Экспериментальная часть
Для электроосаждения кремния использовали расплав KCl-K2SiF6 (5% мас.) с и без добавления SiO2 (0.5% мас.). Для синтеза использовали герметичную стальную ячейку заполненную высокочистым аргоном. Осаждение кремния проводили на стеклоуглеродном электроде с использованием потенциостата Autolab PGSTAT 302N при постоянном потенциале -0.05, -0.15, -0.25 В относительно кремниевого электрода сравнения, противоэлектрод - кремний. Потенциалы для осаждения выбирали на основе циклической вольтамперограммы.
Морфологию образцов кремния изучали с помощью сканирующего электронного микроскопа Tescan Vega 4. Для анализа химического состав полученных материалов использовали приставку для энергодисперсионного анализа Xplore 30 EDS в составе электронного микроскопа и метод атомно-эмиссионной спектроскопии с индуктивно-связанной плазмой NCS Plasma 300.
Для помола материала использовали планетарную мельницу Powteq BM6 Pro, размольная фурнитура и шары изготовлены из диоксида циркония.
Результаты и обсуждение
На Рис. 1 представлены фотографии синтезированных методом электроосаждения частиц кремния. Добавление в состав расплава SiO2 в небольших концентрациях (0.5 % мас.) приводит к изменению в морфологии и кремний осаждается преимущественно в виде иголок, а без добавки SiO2 образуются спутанные волокна.
Рисунок 1. Микрофотографии образцов кремния электросажденного осажденного из расплава KCl, K2SiF6 (5 % мас.) при а) -0,05В б) -0,15В в) -0,25В; из расплава KCl, K2SiF6 (5 % мас.) с добавлением 0.5% мас. SiO2 при г) -0,05В д) -0,15В е) -0,25В
Определение длины волокон в виду их спутанности невозможно, в качестве характеристического размера выбран диаметр частиц, представленные в таблицы 1 результаты приведены на основании 500-800 измерений для каждого образца.
Таблица 1.
Средние характеристические размеры частиц кремния
Образец |
Условия получения |
Е отн. Si, В |
Размер, нм |
1 |
KCl-K2SiF6 (5% мас.) |
-0,05 |
335±174 |
2 |
-0,15 |
266±103 |
|
3 |
-0,25 |
164±67 |
|
4 |
KCl-K2SiF6 – SiO2 (0.5% мас.) |
-0,05 |
286±132 |
5 |
-0,15 |
263±99 |
|
6 |
-0,25 |
219±102 |
Из данных таблицы 1 видно, что смещение потенциала стеклоуглеродного электрода от -0,05 до -0,25 В приводит к ожидаемому снижению размеров формируемых частиц кремния. Наименьший средний размер формируемых частиц достигается для волокон кремния, полученных из расплава KCl-K2SiF6 без добавления SiO2 при потенциале -0,25В , и составляет 164±67 нм.
С целью анализа примесных компонентов в составе полученного порошка использовали метод атомно-эмиссионной спектроскопии. Результаты анализа представлены в таблице 2.
Таблица 2.
Результаты анализа методом атомно-эмиссионной спектроскопии примесных компонентов электроосажденного кремния до (столбец 2 и 3) и после (столбец 4) измельчения с использованием планетарной мельницы
Элемент |
Содержание примесей, ppm |
||
Si KCl, K2SiF6 |
Si KCl, K2SiF6, SiO2 |
Si ПМ KCl, K2SiF6 |
|
Al |
348 |
271 |
311 |
B |
16 |
14 |
22 |
Cr |
351 |
329 |
335 |
Co |
27 |
51 |
41 |
Ni |
1627 |
1247 |
1698 |
Fe |
1674 |
1517 |
1679 |
Mn |
1284 |
879 |
1371 |
K |
1497 |
1792 |
1612 |
Mo |
425 |
411 |
449 |
Ca |
18 |
27 |
38 |
Hf |
- |
- |
486 |
Zr |
- |
- |
9876 |
Как видно из представленных данных, состав расплава не оказывает значительного влияния на содержание примесей. Главным источником примесных элементов Fe, Ni, Cr, Mn является нержавеющая проволока, применяемая для крепления электродов к токоподводам из молибдена. Согласно литературным источникам наличие данных примесей не является препятствием для использование материалов в качестве анодных материалов литий-ионных источников тока [5], однако высокое их содержание может значительно снижать ёмкостные характеристики материала [6].
В связи со слабой циклируемостью синтезируемых материалов в исходном виде [3] и планами по дальнейшему синтезу композитов Si-C с использованием планетарной мельниц проведен помол полученного кремния в течение 1 часа в среде изопропилового спирта при 400 об/мин. Помол оказывает негативное влияние на содержание примесей в составе полученного порошка – компоненты размольной фурнитуры (Zr, Hf) включаются в состав осадка и их содержание может достигать 1% мас.
Выводы
Варьирование размеров частиц в расплаве KCl-K2SiF6 при изменении потенциала электроосаждения возможно только в довольно узких диапазонах и не позволяет добиться получения наноразмерных частиц без использований дополнительной обработки, наименьший средний диаметр полученных частиц составляет 164 нм. Анализ примесей в составе полученных осадков свидетельствует о включении в состав осадка элементов материалов токоподводов - суммарно до 1% мас., что при необходимости получения кремния чистотой выше 99% ведет к необходимости дополнительной кислотной обработки. Дополнительное измельчение с использованием планетарной мельницы и размольной фурнитуры из ZrO2 ведет к включению Zr и Hf в состав осадка в значительном количестве.
Благодарности. Работа выполнена в рамках соглашения №075-03-2024-009/1 от 15.02.2024 (номер темы в ЕГИСУ НИОКТР – FEUZ-2020-0037).
