Технологичность металлов и сплавов при обработке давлением
Конференция: X Международная научно-практическая конференция "Научный форум: технические и физико-математические науки"
Секция: Машиностроение и машиноведение
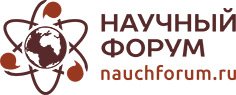
X Международная научно-практическая конференция "Научный форум: технические и физико-математические науки"
Технологичность металлов и сплавов при обработке давлением
The manufacturability of metals and alloys in the processing of pressure
Andrey Udalov
graduate student of the department of metallurgical and rotary machines, FGAOU VO "Ural Federal University named after the first President of Russia B.N. Yeltsin", Russia, Ekaterinburg
Ivan Chukavin
graduate student of the department of materials science and basics of construction, FGBOU VO "Vyatka State University", Russia, Kirov
Alexander Udalov
candidate of technical sciences, associate professor of the department of materials science and basics of construction, FGBOU VO "Vyatka State University", Russia, Kirov
Аннотация. Технологичность и обрабатываемость металла при обработке давлением зависит от многих факторов, что в значительной степени затрудняет использование стандартных механических характеристик для оценки пластичности металла в конкретных условиях деформирования. Данное обстоятельство, вынуждает при проектировании технологических процессов обработки давлением учитывать все факторы, влияющие на пластичность металла. В представленной статье выполнен анализ влияния основных факторов на пластичность металлов, и обозначены направления повышения пластичности в процессах обработки давлением.
Abstract. The manufacturability and workability of metal in the processing by pressure depends on many factors, which greatly complicates the use of standard mechanical characteristics to assess the ductility of the metal under specific deformation conditions. This circumstance forces us to take into account all the factors affecting the plasticity of the metal when designing the technological processes of pressure treatment. In the presented article the analysis of the influence of the main factors on the plasticity of metals is carried out, and the directions of increasing plasticity in the processes of pressure treatment are indicated.
Ключевые слова: металлы; пластичность; напряжения; деформации; показатель пластичности; наклеп; плоскость скольжения.
Keywords: metals; plasticity; stresses; deformations; plasticity index; hardening; sliding plane.
Технологичность материала заготовки, в процессах обработки металлов давлением (ОМД), играет особую роль. Более технологичный металл заготовки позволяет снизить энергосиловые параметры процесса ОМД, повысить его производительность и качество выпускаемой продукции. Технологичность часто заменяют эквивалентным понятием – обрабатываемость, которая устанавливает фактическое изменение свойств металла после обработки давлением. Обрабатываемость в процессах ОМД зависит, прежде всего, от пластичности металла.
Пластичность – способность металла, под действием внешних сил, получать значительные пластические деформации без появления макроразрушений (например, в виде трещин). Количественной характеристикой пластичности, обычно является, предельная степень деформации, накопленная к моменту появления макроразрушений при данных деформационных условиях. Пластическая деформация возникает, когда интенсивность касательных напряжений возникающих в металле заготовки в процессе ОМД достигает значения предела текучести на сдвиг и протекает, в дальнейшем, под действием сдвигающих напряжений.
Поддержание пластичности металла на уровне, обеспечивающем получение деталей требуемой точности и без технологических дефектов, является основной задачей при проектировании процессов ОМД. Такая задача может быть решена, если будут использованы все методы повышения пластичности металла заготовки.
Пластичность металлов не является постоянным свойством, т.к. зависит от многих факторов к числу которых относятся:
- химический состав;
- кристаллическое строение металла;
- схема напряженного состояния металла в очаге деформации при обработке давлением;
- степень деформации и интенсивность упрочнения металла в процессе обработки давлением;
- скорость деформации металла в процессе обработки давлением;
- масштабный фактор;
- температура металла в процессе обработки давлением или эксплуатации.
Пластичность металлов оценивают качественными и количественными характеристиками. Стандартными характеристиками пластичности черных и цветных металлов являются относительное удлинение и относительное сужение
, которые определяют с помощью испытаний на растяжение лабораторных образцов в соответствии с ГОСТ 1497 – 84. Чем больше
и
, тем пластичнее металл и большую степень деформации может получить заготовка, без появления макроразрушений, за одну технологическую операцию.
К характеристикам пластичности относится предел текучести металлов, возрастание которого может иметь положительные и отрицательные последствия. Например, высокие значения предела текучести металла положительно влияют на прочность элементов конструкций. Наоборот, в процессах обработки давлением, высокие значения предела текучести и его возрастание вызванное наклепом металла, приводит к значительному увеличению сил необходимых для осуществления процесса пластической деформации и снижению ресурса пластичности металла.
Основным недостатком стандартных характеристик пластичности (,
и
) является то, что они характеризуют способность металла к пластическому деформированию в процессах обработки давлением, протекающих по схемам напряженного состояния близких к той, при которой они определены. Например, относительное удлинение
образца, полученное при испытании на растяжение, характеризует способность металла к линейному растяжению. Данное обстоятельство в значительной степени затрудняет использование стандартных характеристик для оценки пластичности металла в конкретных условиях деформирования. Поэтому, для каждой группы процессов обработки давлением, протекающих по одной схеме напряженного состояния, целесообразно использовать свой показатель пластичности, а испытания проводить в условиях максимально приближенных к реальному процессу ОМД.
У пластичных металлов для оценки пластичности обычно используют относительное сужение металла. Например, в процессах ковки и объемной штамповки для оценки способности металла получать пластические деформации без разрушения введена технологическая характеристика – ковкость, которая определяется по формуле [7, с. 160],
,
где – ковкость;
– относительное сужение, %;
– предел прочности, соответствующий конкретной температуре нагрева, материала заготовки, МПа.
Ковкость оценивают по пятибальной шкале (табл. 1)
Таблица 1
Пятибальная шкала ковкости [7, с. 160]
Балл |
|
Ковкость |
1 |
Менее 0,01 |
Не куется |
2 |
0,01…0,3 |
Низкая |
3 |
0,31…0,8 |
Удовлетворительная |
4 |
0,81…2 |
Хорошая |
5 |
2,1 и выше |
Отличная |
В процессах ротационной вытяжки пластичность сталей оценивают степенью деформации , которая для данного металла и условий обработки не должна превышать предельного значения [3, с. 64]
,
где – предельная степень деформации;
– степень деформации,
где и
– соответственно, толщина стенки заготовки до и после вытяжки, мм.
Предельную степень деформации при ротационно вытяжке стальных заготовок определяют по эмпирической формуле [3, с.65]
.
В работе [10] предложен способ количественной оценки обрабатываемости металлов по результатам стандартных методов испытаний.
Отсутствие единого общего показателя пластичности затрудняет определение способности металла или сплава к пластической деформации в конкретных деформационных условиях, поэтому необходимо всегда рассматривать комплекс данных по механическим характеристикам.
Влияние химического состава на пластичность сталей. Наибольшей пластичностью обладают химически чистые металлы. Реальные металлы содержат примеси, которые, как правило, снижают пластичность.
Углерод оказывает самое сильное влияние на пластичность сталей (Рисунок 1, а). Повышение содержания углерода в сталях снижает ее пластичность за счет роста в структуре содержания цементита, а прочностные характеристики при этом возрастают, но только до 0,8 % углерода. При увеличении содержания углерода в стали более 0,8 % прочность и пластичность снижаются [9, с.127-128].
Влияние на пластичность постоянных примесей (сера, фосфор, марганец и кремний) на свойства сталей [6, с. 163].
Сера является вредной примесью, т.к. снижает пластичность и вязкость сталей, а также вызывает красноломкость при прокатке и ковке. Содержание серы в сталях допускается 0,06 %. Содержание серы для высококачественных сталей не должно превышать 0,03 %. Сера образует с железом сульфид железа (), который располагается по границам зерен стали и способствует ее красноломкости. Вредное влияние серы компенсируется введением в состав стали марганца. Марганец образует с серой сульфид марганца (
), имеющего высокую пластичность и температуру плавления выше температуры горячей деформации.
Сульфид марганца не влияет на свойства стали в направлении вдоль прокатки, но примерно в 2 раза, снижает пластические свойства поперек прокатки, т. е. увеличивает анизотропию свойств.
Фосфор является вредной примесью, т. к. растворяясь в феррите уменьшает его пластичность и вызывает хладноломкость. Содержание фосфора в сталях, выплавленных в основной мартеновской печи, не превышает 0,04 %, а в электропечах 0,02 %. Стали, выплавленные на первородной шихте без использования скрапа (лома), основного источника примесей, очень чистые по сере и фосфору [6, с. 303].
Марганец и кремний являются полезными примесями.
Марганец вводят в любую сталь для устранения вредных примесей закиси железа () и сернистых соединений железа, в количестве до 0,8 %. Кремний добавляют в сталь в количестве до 0,4 % для раскисления (
) и упрочнения стали. Марганец и кремний, способствуя упрочнению сталей, снижают их пластичность и вязкость.
а) б)
Рисунок 1. Влияние содержания углерода (а) и степени деформации (б) на механические характеристики сталей: – условный предел текучести;
– предел прочности
Влияние на пластичность сталей легирующих элементов [9, с. 179].
Легирование сталей различными элементами (
), в сочетании с термической обработкой, обеспечивает повышение прочности и вязкости по сравнению с углеродистой сталью. При этом, как правило, прочность и твердость повышается, а пластичность падает. Исключением является никель, и в меньшей степени хром, которые наряду с высокой прочностью обеспечивают стали пластичность и вязкость. Интенсивность влияния легирующего элемента, на изменение свойств стали, зависит от того, как сильно различаются атомные размеры железа и легирующего элемента.
Влияние на пластичность сталей скрытых примесей – кислорода, азота и водорода [9, с. 129]. Присутствие скрытых примесей снижает пластичность и вязкость сталей. Эффективным методом снижения влияния скрытых примесей является вакуумирование при выплавке и разливке стали [6, с. 169 – 170].
Влияние типа кристаллической решетки на пластичность металлов.
Существует три типа кристаллических решеток: [6, с. 22 – 25] объемноцентрированная кубическая (), гранецентрированная кубическая (
), гексагональная плотноупакованная (
и редкоземельные металлы).
Пластическая деформация и соответствующие ей сдвиговые деформации в кристаллической решетке осуществляются по плоскостям и в направлениях с наиболее плотной упаковкой атомов. Такие плоскости (направления) называются плоскостями скольжения и зависят от типа кристаллической решетки. Плоскости скольжения и направления скольжения совпадающие с плоскостью наименьшего сопротивления перемещению дислокаций образуют систему скольжения.
У металлов с объемноцентрированной кубической решеткой (Рисунок 2, а) имеются 6 плоскостей скольжения типа (110) и в каждой из них по 2 направления скольжения типа [111]. Число систем скольжения будет равно 6·2=12.
В металлах с гранецентрированной кубической решеткой (Рисунок 2, б) имеется 4 плоскости скольжения типа (111) и в каждой из них по три направления скольжения типа [110]. Число систем скольжения будет равно 4·3=12.
а)
б)
в)
Рисунок 2. Плоскости скольжения и направления скольжения для разных кристаллических решеток: а) объемноцентрированная кубическая; б) гранецентрированная кубическая; в) гексагональная плотноупакованная; – период (параметр) кристаллической решетки
В металлах с гексагональной плотноупакованной кубической решеткой (рис. 2, в) есть только одна плоскость скольжения типа (0001), в которой есть
три направления скольжения типа [1120]. Число систем скольжения будет равно 1·3=3.
Чем больше систем скольжения в кристаллической решетке, тем выше пластичность металла. Холодная пластическая деформация металлов с объемноцентрированной и гранецентрированной кубической решеткой осуществляется, в основном, путем скольжения, а с гексагональной плотноупакованной кубической решеткой двойникованием [1, с. 22].
Влияние на пластичность металлов степени деформации в процессе ОМД. Пластическое формоизменение при степенях деформации не превышающих предельные сопровождается повышением прочности и твердости металла, что объясняется появлением в структуре металла дислокаций. Данное явление называется наклепом металла или нагартовкой. При наклепе пластичность металла в значительной степени снижается. С целью установления влияния наклепа на характеристики пластичности и прочности выполняют построение кривых упрочнения. Для этого, наиболее часто, используют метод двухстадийного нагружения образцов [13]. Примеры графических зависимостей характеристик пластичности и прочности от степени деформации, для стали 20, показаны на рисунке 1, б [13, с. 117].
С целью устранения последствий наклепа и восстановления пластичности металла выполняют межоперационный рекристаллизационный отжиг. Приближенное значение температуры начала (порога) рекристаллизации металлов и сплавов определяют по формуле А. А. Бочвара [12, с. 201]
,
где ,
– соответственно, абсолютные температуры начала рекристаллизации и плавления;
– коэффициент, учитывающий степень чистоты металла, размер зерна до деформации, степень предварительной пластической деформации и т. д.
Ориентировочно коэффициент принимают следующим образом:
– для металлов очень высокой чистоты;
– для технически чистых металлов;
– для твердых растворов.
В процессе рекристаллизации в деформированном металле образуются новые зерна, снимаются внутренние напряжения и восстанавливается пластичность металла.
Влияние напряженного состояния в очаге деформации на пластичность сталей. Различают линейное, плоское и объемное напряженное состояние тела. В технологических процессах ОМД используют схемы напряженного состояния, обеспечивающие металлу наибольшую пластичность. Пластичность металла, в данном случае, оценивают показателем напряженного состояния , который равен отношению среднего нормального напряжения
к интенсивности касательных напряжений
.
Количественной мерой пластичности является предельная степень деформации сдвига , соответствующая моменту разрушения. По результатам испытаний лабораторных образцов строятся диаграммы пластичности (Рисунок 3)
, которые используют для определения предельных степеней деформации металла [1, с. 132]. Из диаграммы пластичности следует, что с ростом отрицательного значения показателя напряженного состояния
предельная степень деформации сдвига
увеличивается. Область диаграммы пластичности, расположенная с левой стороны границы
соответствует неограниченной пластичности стали. Область диаграммы пластичности, расположенная с правой стороны границы
соответствует абсолютной хрупкости стали. Таким образом, наибольшую пластичность металлу обеспечивают схемы объемного напряженного состояния, в которых преобладают напряжения сжатия. Например, схема неравномерного всестороннего сжатия (Рисунок 4, а) присутствует в технологических операциях прокатки, ковки, прессования, выдавливания, ротационной вытяжки по обратному способу, что обеспечивает металлу повышенную пластичность.
Рисунок 3. Диаграмма пластичности металла: – показатель напряженного состояния, соответствующий порогу хрупкости;
– показатель напряженного состояния, соответствующий порогу неограниченной пластичности
а) б)
Рисунок 4. Схемы объемного напряженного состояния: а) схема неравномерного всестороннего сжатия; б) схема с двумя сжимающими и одним растягивающим главными нормальными напряжениями; – главные нормальные напряжения
В таблице 2 представлены показатели напряженного состояния , соответствующие типовым процессам ОМД [2, с.37]. Из таблицы видно, что из представленных процессов наибольшую пластичность металлу могут обеспечить прокатка листа и гидропрессование круглых прутков.
Таблица 2
Значения показателя напряженного состояния
№ пп |
Способ ОМД |
|
1 |
Волочение проволоки |
-1,15…0,50 |
2 |
Волочение труб на оправке |
-1…0,40 |
3 |
Безоправочное волочение труб |
-0,58…0,40 |
4 |
Гидропрессование круглых прутков |
-6…1,15 |
5 |
Валковое редуцирование труб |
-1…-0,58 |
6 |
Прокатка труб на станах ХПТ |
-3,5…0,58 |
7 |
Прокатка листа |
-5…-1 |
Влияние температуры нагрева на пластичность металла в процессе ОМД. Горячая пластическая деформация сопровождается повышением пластических свойств металла, снижением сопротивления деформации и, соответственно, снижением энергетических затрат. При горячем деформировании параллельно протекают два противоположных процесса – упрочнение и разупрочнение. Разупрочнение происходит в результате процессов возврата и рекристаллизации. Температурный интервал горячего деформирования выбирают таким образом, чтобы скорость протекания рекристаллизации превышала скорость упрочняющих процессов. Эффект разупрочняющих процессов усиливается при повышении температуры нагрева, уменьшении скорости и степени деформации. Начальная температура горячего деформирования должна быть ниже температуры плавления металла , а конечная выше температуры рекристаллизации
. Например для углеродистых сталей, верхний предел температуры нагрева ограничивают явлениями перегрева и пережога и устанавливают на 100-150оС ниже линии солидуса на диаграмме состояния, а температуру конца деформирования принимают на 50-100оС выше температуры рекристаллизации [12, с. 500]. Допустимые температурные интервалы горячей обработки давлением для некоторых сталей приведены в таблице 3.
Таблица 3
Температурные интервалы горячей обработки давлением [8, с. 153]
Марка стали |
Температурный интервал, оС |
Ст0, Ст3, Сталь 10 |
1300…750 |
45, 40Х, 35ХГСА, 10Г2, 40ХФА |
1250…800 |
08Х18Н10Т, 20Х23Н18 |
1220…950 |
12Х18Н10Т, 40Х9С2, 08Х13, Р18 |
1200…850 |
У7А, ХГВ, 50ХПА |
1180…800 |
ШХ15, 9ХС, 90ХМФ, 12Х21Н5Т |
1180…800 |
Влияние скорости деформации на пластичность металла в процессах ОМД. Скорость деформации – изменение степени деформации в единицу времени. Влияние скорости деформации, особенно сильно сказывается, при горячей обработке давлением. В практических расчетах влияние скорости деформации учитывают, например, при помощи скоростного коэффициента [5, с. 384], показывающего, во сколько раз увеличивается скорость протекания упрочняющих процессов в процессе формоизменения металла при соответствующем увеличении скорости и температуры деформации (Таблица 4).
Влияние масштабного фактора на пластичность металлов в процессах ОМД. Пластичность металла большой заготовки всегда меньше, чем у маленькой. Данное обстоятельство объясняется значительной неравномерностью напряжений и деформаций в объеме большой заготовки. Поэтому, для оценки пластичности большой заготовки необходимо применять специальные методики учета влияния объема на пластичность [4, с. 279-317; 11, с. 171-184].
Таблица 4
Значение скоростного коэффициента [5, с. 384]
Увеличение скорости деформации |
Относительная температура деформации,
|
|||
˂ 0,3 |
0,3…0,5 |
0,5…0,7 |
> 0,7 |
|
В 10 раз |
1,05…1,10 |
1,10…1,15 |
1,15…1,30 |
1,30…1,50 |
В 100 раз |
1,10…1,22 |
1,22…1,32 |
1,32…1,70 |
1,70…2,25 |
В 1000 раз |
1,16…1,34 |
1,34…1,52 |
1,52…2,20 |
2,20…3,40 |
При переходе от скорости деформации 10-1 с-1 к ударной нагрузке |
1,10…1,25 |
1,25…1,75 |
1,75…2,50 |
2,50…3,50 |
Примечание: |
Таким образом, из представленного обзора видно, что практически любой из рассмотренных факторов может существенно повлиять на пластичность металла в процессе обработки давлением и привести к появлению брака. Поэтому, основным направлением повышения качества металлопродукции при назначении технологических режимов обработки в процессах ОМД является комплексный учет всех факторов, влияющих на пластичность металла.
Список литературы:
1. Богатов А.А. Механические свойства и модели разрушения металлов: учеб. пособие для вузов. – Екатеринбург: ГОУ ВПО УГТУ – УПИ, 2002. – 329 с.
2. Богатов А.А., Мижирицкий О.И., Смирнов С.В. Ресурс пластичности металлов при обработке давлением. – Москва: Металлургия, 1984. – 144 с.
3. Гредитор М.А. Давильные работы и ротационное выдавливание. – Москва : Машиностроение, 1971. – 239 с.
4. Губкин С.И. Пластическая деформация металлов. В 3 т. Т. 1. Физико-механические основы пластической деформации. – Москва: Металлургиздат, 1961. – 376 с.
5. Губкин С.И. Пластическая деформация металлов. В 3 т. Т. 2. Физико-химическая теория пластичности. – Москва: Металлургиздат, 1961. – 416 с.
6. Гуляев А.П. Металловедение. – Москва: Металлургия, 1986. – 544 с.
7. Ковка и штамповка: справочник. В 4 т. Т. 1. Материалы и нагрев. Оборудование. Ковка – 2–е изд., перераб. и доп. / под ред. Е.Н. Семенова. – Москва: Машиностроение, 2010. – 717 с.
8. Мастеров В.А., Берковский В.С. Теория пластической деформации и обработка металлов давлением. – Москва: Металлургия, 1989. – 400 с.
9. Металловедение и технология металлов / Ю.П. Солнцев [и др.]. – Москва: Металлургия, 1988. – 512 с.
10. Орлов Г.А. Инженерная оценка обрабатываемости металлов давлением // Изв. вузов. Черная металлургия. – 2013. – № 3. – С. 11–14.
11. Тарновский И.Я., Трубин В.Н., Златкин М.Г. Свободная ковка на прессах. – Москва: Машиностроение, 1967. – 328 с.
12. Технология металлов / Б.В. Кнорозов [и др.]. – Москва: Металлургия, 1978. – 904 с.
13. Третьяков А.В., Зюзин В.И. Механические свойства металлов и сплавов при обработке давлением: справочник. – Москва: Металлургия, 1973. – 224 с.
