ПЕРСПЕКТИВНЫЙ МЕТОД НЕРАЗРУШАЮЩЕГО КОНТРОЛЯ – КОМПЬЮТЕРНАЯ ТОМОГРАФИЯ
Конференция: XLVII Международная научно-практическая конференция «Научный форум: технические и физико-математические науки»
Секция: Металлургия и материаловедение
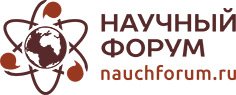
XLVII Международная научно-практическая конференция «Научный форум: технические и физико-математические науки»
ПЕРСПЕКТИВНЫЙ МЕТОД НЕРАЗРУШАЮЩЕГО КОНТРОЛЯ – КОМПЬЮТЕРНАЯ ТОМОГРАФИЯ
COMPARISON OF COMPUTED TOMOGRAPHY WITH ULTRASONIC CONTROL METHOD
Goncharov Vladimir
AO «NPO Lavochkin», Russia, Khimki
Аннотация. Исследованы детали и заготовки, изготовленные из алюминиевых сплавов с использованием ультразвукового контроля и компьютерной томографии. Показан перспективный метод неразрушающего контроля – компьютерная томография и рассмотрены ее преимущества по сравнению с ультразвуковым методом контроля.
Abstract. Details and work pieces made of aluminum alloys were studied using radiographic control and computed tomography. A promising method of nondestructive testing-computed tomography is shown and its advantages in comparison with the ultrasonic method of control are considered.
Keywords: non-destructive testing; computed tomography (CT); tomography; ultrasonic inspection (UT); defectoscope
Ключевые слова: неразрушающий контроль; компьютерная томография (КТ); томограф; ультразвуковой контроль (УЗК); дефектоскоп
Часто при контроле деталей из металлических материалов возникают сложности в определении характера неоднородностей и природы их возникновения.
Цель настоящей работы – показать целесообразность применения томографии как дополнительного источника информации при формировании экспертного мнения по этим неоднородностям на примере алюминиевого сплава АМг6.
Исследования проводили на деталях и заготовках, изготовленных из алюминиевого сплава АМг6, следующими методами контроля: ультразвуковым (УЗК), компьютерной томографией (КТ).
Томографию деталей и заготовок осуществляли промышленным компьютерным томографом V|tome|x m 300 General Electric (Германия) [1, 2].
Факультативно КТ проводилась на четвертом (УЗК поковок) этапе производства деталей, где соответственно сравнивался УЗК с КТ.
Рассмотрим неоднородности в материале изделия, которые помогла выявить КТ на этапе УЗК поковок. По сравнению с другими способами контроля УЗК имеет следующие основные преимущества:
- лучшее выявление плоскостных дефектов;
- высокая скорость контроля;
- безопасность для персонала.
При определенных недостатках УЗК (необходимость разработки специальных методик и ультразвуковых преобразователей для каждой контролируемой детали для изделий с неплоской поверхностью; относительная сложность расшифровки результатов контроля, определения места расположения, размера и характера дефекта) этот метод контроля благодаря высокой производительности и малой стоимости является наиболее распространенным.
Ультразвуковой контроль полуфабрикатов из алюминиевого сплава АМг6 проводили эхо-методом с помощью дефектоскопа УД9812 совместно с преобразователями П111-2,5-14 и П112-2,5-14. Вследствие сложности расположения несплошностей в объекте контроля примененяли преобразователи с частотой 2,5 МГц.
Использование более высоких частот при контроле оказывает влияние на отраженные эхосигналы от несплошностей, расположенных не перпендикулярно к направлению ввода ультразвуковых волн. Согласно требованиям технологической инструкции 023000.25020.00046 [3] для алюминиевых сплавов диаметр контрольного отражателя для регистрации устанавливается на уровне 1,6 мм, что соответствует площади 2 мм2. В связи с этим настройку прибора выполняли по стандартным образцам с искусственным дефектом типа «плоскодонное отверстие» диаметром 1,6 мм.
В качестве поискового был принят уровень эхоимпульса ниже уровня фиксации, указанного в технологической инструкции 023000.25020.00046 [3], на 6 дБ. В процессе контроля в области центра продольной оси поковки были выявлены множественные эхоимпульсы выше поискового уровня, но ниже уровня фиксации. В центральной области наблюдались также множественные эхосигналы ниже поискового уровня.
Снимок экрана дефектоскопа, показывающий А-скан с эхосигналом от возможного дефекта при контроле преобразователем П112-2,5-14 приведен на рисунке 1. На рисунке 1 строб (зона контроля) #1 показывает уровень браковки при ультразвуковом контроле, строб Ф – уровень фиксации, П – поисковый уровень, S – селектор, предназначенный для выбора режима измерений.
#1 – уровень браковки; Ф – уровень фиксации, П – поисковый уровень, S – селектор, предназначенный для выбора режима измерений
Рисунок 1. Снимок экрана дефектоскопа, показывающий А-скан экрана дефектоскопа с эхоимпульсами, наблюдаемыми в процессе контроля
Как видно из рисунка 1, уровень эхосигналов оказался ниже уровня регистрации на 2,2 дБ. Подобный уровень эквивалентного отражения можно получить от несплошности площадью около 1,55 мм2.
Для анализа эхоимпульсов УЗК алюминиевой поковки проводили ее томографию, за один сеанс которой была построена 3D модель (рисунок 2).
Автоматическое определение дефектов осуществляли при помощи дополнительного модуля к программе VGStudio MAX, в котором использовался алгоритм поиска пор VGDefX объемом от 0,01 до 5 мм3. На рисунке 2 представлено томографическое изображение, которое состоит из трех ортогональных разрезов поковки (Top 1, Right 1, Front 1) и 3D модели с прозрачностью 70 % для видимости цветных дефектов и их формы. В нашем случае сечение проведено в месте дисклокации дефекта объемом 1,53 мм3 (рисунок 2).
а) б)
в) г)
defect 1 – дефект 1; position – позиция дефекта; probability – вероятность дефекта; diameter – диаметр дефекта; volume – объем дефекта; projected area – проекция дефекта на плоскость; а – вид сверху (top 1); б – вид сбоку (right 1); в – вид спереди (front 1); г – объемная модель поковки (3D)
Рисунок 2. Томографический снимок поковки из сплава АМг6
Анализ полученных изображений двух видов показывает, что пики на А‑сканах дефектоскопа, показанные на рисунке 1, представляют собой эхосигналы от внутренних несплошностей, образовавшихся из газовых пузырей или неметаллических включений при прокатке или ковке, распространяющиеся ближе к оси поковки и вдоль волокон металла.
Шлаковые и песчаные включения не способны пластически деформироваться и при обжатии слитка распадаются на большое число обломков с острыми углами, образуя при вытяжке цепочки вдоль волокон.
Программное обеспечение томографа обладает возможностью определения размера в любой плоскости. В нашем случае размеры дефектов колеблются по оси X от 0,19 до 1,2 мм, по оси Y от 0,17 до 1,66 мм и по оси Z от 0,26 до 7,1 мм с максимальной площадью проекции до 3,43 мм2 (площади проекций по оси Z показаны цветной масштабной линейкой). Меньший уровень площади проекции несплошности, выявленный при УЗК, объясняется использованием непритертого пьезоэлектрического преобразователя. Однако следует отметить, что протяженные дефекты с шириной раскрытия меньше 1 мм при УЗК выявлены не были. Это обусловлено физическими свойствами ультразвуковой волны (дифракция ультразвуковых волн) и требованиями технологической инструкции, предотвращающими перебраковку заготовок при проведении неразрушающего контроля.
Таким образом, характер полученных дефектов КТ свидетельствует о недопустимости дальнейшего использования исследуемой поковки для изготовления фланца, работающего под давлением. Можно использовать эту поковку для изготовления других деталей, предварительно удалив сердцевину с дефектами, границы сверления которых легко определяются в программном обеспечении.
При помощи специализированного программного обеспечения VGStudio MAX можно увидеть сечение исследуемого объекта любой плоскостью, провести анализ пор, пустот, сопоставить ее с CAD-данными исследуемого объекта, а также импортировать полученную модель объекта в CAD-систему (обратное проектирование).
В работе предложена усовершенствованная таблица выбора соответствующего метода неразрушающего контроля [4, с. 83].
Таблица.
Рекомендации по применению методов неразрушающего контроля
Дефекты, объекты контроля, их характеристики и условия контроля |
Применимость методов дефектоскопии: |
||||||
1 |
2 |
3 |
4 |
5 |
6 |
7 |
|
Дефекты производственного происхождения |
|||||||
В поковках, штамповках и профилях |
|||||||
Закаты, заковы |
Ш |
О |
О |
Ш |
Н |
Н |
Ш |
Флокены |
О |
Н |
О |
Ш |
Н |
Н |
Ш |
Расслоения, внутренние трещины |
Н |
Н |
Н |
Ш |
Н |
О |
Ш |
Трещины и рванины, выходящие на поверхность |
Ш |
Ш |
О |
Ш |
Н |
Н |
Ш |
Включения |
О |
О |
Н |
Ш |
Н |
О |
Ш |
Возникшие при сварке: |
|||||||
Трещины |
Ш |
Ш |
Ш |
Ш |
Н |
О |
Ш |
Непровары |
Ш |
Н |
Н |
Ш |
Н |
О |
Ш |
Шлаковые включения |
Н |
Н |
Н |
О |
Н |
Ш |
Ш |
Раковины, пористость |
Н |
О |
Н |
О |
Н |
Ш |
Ш |
Возникшие при пайке: |
|||||||
Трещины |
Н |
О |
Н |
О |
О |
О |
Ш |
Непропаи |
Н |
О |
Н |
О |
О |
Ш |
Ш |
Пористость |
Н |
Н |
Н |
О |
Н |
Ш |
Ш |
Возникшие при механической обработке |
|||||||
Шлифовочные трещины |
Ш |
Ш |
О |
О |
Н |
Н |
Ш |
Рихтовочные трещины |
Ш |
Ш |
Ш |
Ш |
Н |
О |
Ш |
Надрывы |
Ш |
Ш |
Н |
Н |
Н |
Н |
Ш |
Разностенность и подрезы |
Н |
Н |
Н |
Н |
Н |
Ш |
Ш |
Возникшие при термической обработке |
|||||||
Закалочные трещины |
Ш |
Ш |
Ш |
Ш |
Н |
О |
Ш |
Несоответствие структуры |
Н |
Н |
О |
Н |
Н |
Н |
Ш (нано КТ) |
Несоответствие толщины упрочненного слоя |
Н |
Н |
О |
Ш |
Н |
Н |
Ш (нано КТ) |
Возникшие при литье: |
|||||||
Раковины, пористость |
Н |
О |
Н |
Ш |
Н |
Ш |
Ш |
Трещины (поверхностные) |
Ш |
Ш |
Ш |
Ш |
Н |
О |
Ш |
Разностенность |
Н |
Н |
Н |
Н |
Н |
Ш |
Ш |
Ликвация |
Н |
Н |
Н |
Ш |
Н |
Ш |
Ш |
Спаи |
Ш |
О |
О |
Ш |
Н |
Н |
Ш |
Включения |
О |
Н |
Н |
Ш |
Н |
Ш |
Ш |
Продолжение таблицы
Дефекты, возникающие при эксплуатации |
|||||||
Усталостные и другие открытые трещины |
Ш |
Ш |
Ш |
Ш |
Н |
О |
Ш |
Точечные коррозионные поражения |
Н |
Ш |
Н |
О |
Н |
Ш |
Ш |
Механические повреждения поверхности (забоины, вмятины, риски и др.) |
Н |
Н |
Н |
О |
Н |
Н |
Ш |
растрескивание и межкристаллитная коррозия |
Н |
Ш |
О |
Ш |
Н |
О |
Ш |
деформация и разрушение закрытых деталей |
Н |
Н |
Н |
О |
Н |
Ш |
Ш |
трещины и коррозионные поражения в закрытых участках |
Н |
Н |
Н |
О |
Н |
О |
Ш |
Зоны и условия контроля |
|||||||
Контроль всей поверхности |
Ш |
Ш |
О |
О |
О |
Ш |
Ш |
местный контроль (отдельных зон) |
Ш |
Ш |
Ш |
Ш |
Ш |
Ш |
Ш |
Демонтированные детали |
Ш |
Ш |
Ш |
Ш |
Ш |
Ш |
Ш |
Недемонтированные детали (контроль в узле) |
|||||||
При доступе с двух сторон |
Ш |
Ш |
Ш |
Ш |
Ш |
Ш |
Ш (мало-габаритные) |
При доступе с одной стороны (дефект с противоположной) |
Н |
Н |
О |
Ш |
Ш |
Н |
Ш (мало-габаритные) |
При ограниченных подходах (в труднодоступных местах) |
Н |
Н |
О |
О |
Н |
О |
Ш (мало-габаритные) |
При отсутствии подходов (закрытые детали) |
Н |
Н |
Н |
О |
Н |
О |
Ш (мало-габаритные) |
Место расположения дефектов |
|||||||
Поверхностные |
Ш |
Ш |
Ш |
О |
Н |
Ш |
Ш |
Подповерхностные (на глубине 0,3-1 мм) |
О |
Н |
О |
О |
О |
Ш |
Ш |
Внутренние (глубинные дефекты) |
Н |
Н |
Н |
Ш |
О |
Ш |
Ш |
Дефекты, расположенные в ослабленных участках детали (галтелях, пазах, отверстиях, на острых кромках и т.д.) |
Ш |
Ш |
Ш |
О |
Н |
Ш |
Ш |
Продолжение таблицы
Физические свойства материала контролируемых объектов |
|||||||
Ферромагнитные |
Ш |
Ш |
О |
Ш |
Ш |
Ш |
Ш |
Немагнитные с мелкозернистой структурой |
Н |
Ш |
Ш |
Ш |
Ш |
Ш |
Ш |
Немагнитные с крупнозернистой структурой |
Н |
Ш |
Ш |
О |
Ш |
Ш |
Ш |
Неметаллические |
Н |
О |
Н |
Ш |
Ш |
Ш |
Ш |
Форма и размеры контролируемых деталей |
|||||||
Простая (одинакового сечения) |
Ш |
Ш |
Ш |
Ш |
Ш |
Ш |
Ш |
Сложная (с различной кривизной в зоне контроля) |
Ш |
Ш |
О |
О |
Н |
Ш |
Ш |
Крупногабаритные и массивные |
Ш |
Ш |
Ш |
Ш |
Ш |
О |
О |
Микродетали (миниатюрные изделия) |
Н |
О |
О |
Н |
Н |
О |
Ш |
Микродетали толщиной более 1 мм |
Ш |
Ш |
Ш |
Ш |
Ш |
Ш |
Ш |
Микродетали толщиной менее 1 мм |
Ш |
Ш |
Ш |
О |
Н |
О |
Ш |
Примечание – Магнитопорошковый метод – 1; капиллярный – 2; токовихревой (накладных датчиков) – 3; УЗК – 4; акустический – 5; метод рентгенографического и g-контроля – 6; компьютерная томография (КТ) – 7; Ш – широкая применимость метода; О – ограниченная; Н – неприменимый |
