Ранжирование специалистов конструкторского бюро с применением метода Делфи
Конференция: XXVI Международная научно-практическая конференция «Научный форум: технические и физико-математические науки»
Секция: Авиационная и ракетнокосмическая техника
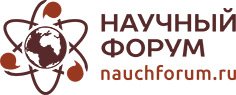
XXVI Международная научно-практическая конференция «Научный форум: технические и физико-математические науки»
Ранжирование специалистов конструкторского бюро с применением метода Делфи
RANKING SPECIALISTS DESIGN OFFICE WITH THE USE OF DELPHI METHOD
Yuri Chakaev
graduate student of Ulyanovsk Institute of civil aviation. B. P. Bugaev, Russia, Ulyanovsk
Ekaterina Alyakina
graduate student of Ulyanovsk Institute of civil aviation. B. P. Bugaev, Russia, Ulyanovsk
Аннотация. Уровень технологической проработки конструкции оставляет отпечаток на надежности самолета. На серийных самолетостроительных заводах совместные усилия конструктора и технолога на этапе производства способны снизить количество скрытых производственных дефектов. Основа высококачественного серийного производства - это повышение качества конструкторской документации и неусыпный контроль технологических процессов.
Abstract. The level of technological development of the design leaves an imprint on the reliability of the aircraft. At serial aircraft factories, the joint efforts of the designer and the technologist at the production stage can reduce the number of hidden manufacturing defects. The basis of high-quality serial production - is to improve the quality of design documentation and vigilant control of technological processes.
Ключевые слова: метод Делфи; конструкторское бюро; конструкторская документация.
Keywords: Delphi method; design Bureau; design documentation.
Введение
Вопрос о безопасности полетов (БП) остро стоит на повестках дня разного уровня совещаний причастных к авиации лиц. В представленном исследовании предлагаем рассмотреть влияние качества конструкторской документации (КД) на БП.
Проведем связи: конструктор выпускает КД на самолет. На основании этой КД технолог производства формирует технологическую документацию (ТД). По ней идет процесс производства самолетных деталей. Визуально можно представить на схеме ниже (Рис.1):
Рисунок 1. Схема
В основе лежат объективные выполнимые требования к качеству деталей, заложенные конструктором у истока.
А качество КД состоит и зависит от полноты указанных в ней требований. Если этих требований недостаточно, для соблюдения условий долговечности, ремонтопригодности, технологичности деталей, то и качество КД является пропорционально сниженным от номинала.
Изготовленные с меньшим качеством от номинала детали не имеют требуемых запасов прочности, структуры материала и не отвечает заявленному ресурсу.
При эксплуатации ВС с изделиями, изготовленными по КД не соответствующего качества самолет, в какой-то момент не справится с реальными возникающими условиями в полете, при приземлении или наборе высоты и произойдет отказ системы [1].
Говорить о создании идеальной модели ВС с первого раза не приходится. За многолетнее наблюдение было отмечено, что с течением определенного времени можно улучшить и приблизить к совершенству некоторые параметры ВС.
Для этого необходимы регулярные оценки надежности элементов ВС.
На основании полученных данных оценки надежности внедрять научные достижения, которые касаются: увеличения ресурсного срока службы, ремонтопригодности, дублирования и других систем.
Надежность - свойство объекта сохранять во времени в установленных пределах значения всех параметров, характеризующих способность выполнять требуемые функции в заданных режимах и условиях применения, технического обслуживания, ремонтов, хранения и транспортирования.
Фактически сегодня мы имеем:
- Проблема формирования и оптимизации содержания и объемов ТОиР, которые в конечном итоге определяют уровень всех видов затрат в ТЭ ЛА.
- Расчет параметров ВС на стадии проектирования возможен лишь до определенного уровня, который на тот момент был около предельного значения.
- Уточнение и подтверждение расчетных параметров ВС в ходе испытаний имеет своей целью войти в допустимые значения.
- Поддержка летной годности, состоящая из необходимой и опытноконструкторской доводки, по ходу эксплуатации складывается из наблюдений за определенный период.
Получение более полной информации о работе ВС возможно за счет:
- внедрения предиктивного ремонта (систем контроля узлов ВС);
- детального учета человеческих факторов и каждого в отдельности;
Одна из разновидностей влияния человеческих факторов еще до эксплуатации ВС на его функциональные системы, летные характеристики, надежность и последующее поддержание летной годности просматривается на стадии проектирования ВС. Инженеры-конструкторы работают над узлами и системами самолета по принадлежности, составлением технологических процессов на основании конструкторской документации занимаются технологи и другими участниками локальных систем по проектированию и постановке на производство ВС типа.
Образование, начальная подготовка, опыт работы, квалификация, степень загруженности, объем работы и индивидуальные данные работников конструкторского бюро влияют на качество выполняемой работы. Чем выше показатели по выделенным нами параметрам, характеризующим эффективность конструкторов, тем выше качество выполняемой им работы. При первом приближении появляется ощущение, что речь идет о логической взаимосвязи параметров и другого исход не возможен. Другими словами, и так ясно, что чем выше показатели, тем лучше. Да и вообще, почему Вы решили, что именно эти параметры кроются за ошибками, которые мы называем человеческими факторами? Отражают ли они суть происходящего в реальном времени при воздействии на них и их изменении?
В данном исследовании предлагаем проверить гипотезу на сколько совокупность различных значений параметров у разновозрастных сотрудников КБ влияет на качество выполняемой ими работы. Это устанавливается за счет расстановки сотрудников по степени значимости и по роли в КБ. Это позволит проанализировать какой из параметров для конкретного работника нужно развить, чтобы повысить индивидуальную эффективность и производительность КБ в целом. В некоторых случаях совокупность развиваемых параметров позволяет улучшить выбранный показатель.
Для этого проводилось наблюдение в течение нескольких месяцев за одним из отраслевых КБ самолетостроительного предприятия, что позволило отобрать фокус-группу из 25 сотрудников преимущественно со стажем работы до 5 лет. Хронометраж и фиксация критериев успеваемости позволили выделить несколько взаимовлияющих параметров отражающих эффективность сотрудников.
Влияние технологии изготовления на показатели надежности.
При создании нового изделия акцент делается на обеспечение требований к качеству, и только потом к производительности и экономичности производственных процессов.
Показатели качества: точность выдерживания посадочных размеров, сопряжения, обводы, чистота поверхностей трущихся пар, величина натяга в неразъемных соединения, степень герметичности трубопроводов, клеевых и сварных соединений агрегатов, усилия трения в подвижных соединениях и значения массы деталей являются результатом производственного процесса использованной технологии и объективно прогнозируют будущую работоспособность.
Однако показатели качества оценивают лишь завершившийся этап изготовления и сборки элементов самолета.
При изготовлении и сборке агрегатов имеет место быть нестабильность производственных процессов, а при эксплуатации на самолет воздействуют реальные условия и случайные нагружения - не исключение.
Статистические данные об отказах в эксплуатации являются той обратной связью, которая позволяет посредством изменения значений показателей качества продукции корректировать технологические способы производства.
Несмотря на возрастающий объем испытаний в процессе проектирования, начальный этап эксплуатации почти каждого самолета является периодом его конструктивно - технологической доводки и продолжается от 2 до 5 лет.
Зависимость между показателями качества производства и показателями их надежности является результатом анализа причин отказов и изучения вызывающих их физических процессов.
Знание закономерностей влияния технологии изготовления на показатели надежности самолета обеспечивает разработку оптимального производственного процесса, при котором принятые показатели качества продукции гарантируют требуемые показатели надежности.
Во время производства элементов самолета с несоблюдением требований технологического процесса возможно возникновение недостатков в конструкции.
Классификация причин производственных недостатков самолетов:
- заниженные значения принятых показателей качества полуфабрикатов, готовых изделий, агрегатов и систем;
- методологические недостатки технологии изготовления, сборки и испытаний;
- низкая стабильность производственных процессов из-за отклонения параметров исходных материалов и недостаточной надежности оборудования.
Существенным признаком отказа из-за производственного недостатка является время его проявления - малый налет после его впуска.
В течении первых нескольких сот часов налета скрытые производственные недостатки, как правило, проявляются по экспоненциальному закону.
В зависимости от происхождения выделяют три группы: недостатки материалов, недостатки обработки и недостатки сборки.
Недостатки материала определяются отклонением от ТУ или ГОСТов и бывают: местные, распределенные и по всему объему полуфабрикатов.
Технологической наследственностью - называется сохранение и суммирование недостатков в последовательных стадиях производственного процесса.
Недостатки обработки деталей проявляются, начинаются, начиная со стадии пластической деформации заготовок. Наследуя недостатки литья, процесс пластической деформации вносит такие недостатки как расслоения, рванины, волосовины.
Теория надежности силовых элементов планера в аспекте сопротивления усталости успешно развивается в трудах ряда ученых.
В отличие от традиционной детерминированной прочности вероятностная прочность рассматривает внешние нагрузки и несущую способность.
Почему же агрегаты, комплектующие изделия или система самолета, которые разрабатывались на самом высоком техническом уровне с использованием научно обоснованных методик и опыта конструирования аналогов, которые изготавливались в полном соответствии с ТУ и которые эксплуатировались на самолете строго по проверенной на практике инструкции и обслуживались по утвержденному регламенту, все же отказывают, с очень малой вероятностью в случайные моменты времени полета?
Объективные причины того, что возникновения отказа есть случайное событие делятся на две группы:
1. Различие в изготовлении:
- разброс физических и прочностных характеристик исходных материалов;
- случайное сочетание геометрических параметров подвижных и неподвижных соединений в пределах предусмотренного допуска чертежа;
- нестабильность ТП;
2. Не абсолютная идентичность режимов полета и условий эксплуатации:
- случайный характер сочетаний внешних воздействий и нагрузок;
- отклонения ожидаемых условий эксплуатации (ОУЭ) от фактических в различных климатических зонах;
- отличие внешних условий работы в полете и при стендовой отработке систем (где не воспринимаются положительные и отрицательные перегрузки, углы атаки, турбулентность атмосферы, реальные уровни вибраций, грозовые разряды и др.)
Отказы систем самолета невозможно полностью исключить, но их количество по времени можно прогнозировать на основе методов расчета безотказности.
Предельное состояние оценивается по соответствующим признакам или критериям, которые устанавливаются главным конструктором и НЛГ.
Принципиальным отличием отечественного подхода к решению проблемы Обеспечения безопасной эксплуатации ВС от американского и европейского в том, что она основана на Поэтапном Установлении Ресурса и Срока Службы ВС (далее ПУРиСС).
ПУРиСС означает, что эксплуатация ВС по мере их наработки и старения разделяется на этапы. Длительность этапа = межремонтный ресурс. При вводе парка в эксплуатацию этот ресурс = 5000-6000 л.ч., что = 3-4 года службы.
Для ВС без капитального ремонта этап УСС = те же 3-4 года эксплуатации.
В пределах очередного этапа установления ресурса и срока службы выявляются все недостатки, например, человеческий фактор при проектировании выраженный в неверно подобранном материале, некорректно приложенной нагрузке и выбранной схеме испытаний, не учтены внешние воздействия и близко расположенные элементы.
Для подробного разбора применения метода Делфи разберем для примера производительность инженеров в конструкторском бюро.
Для этого поставим условия задачи:
Выполнить комплексную оценку совокупности изучаемых параметров инженеров и провести сравнительный анализ значимости этих параметров с использованием метода Дельфи [3].
Решение:
Найдем максимальное значение по каждому изучаемому показателю и выделим его в матрице исходных данных (Табл. 1).
Таблица 1.
Матрица исходных данных
Инженер |
Показатели эффективности |
Динамика |
||||
Квалификация |
Время выполнения одного проекта* |
Объем выпущенных форматов А4** |
Рабочих часов в месяц |
Важность для отдела*** |
||
1 |
2 |
3 |
4 |
5 |
6 |
|
1 |
15,00 |
112,00 |
21,43 |
160 |
7,47 |
|
2 |
25,00 |
97,00 |
40,21 |
156 |
3,88 |
|
3 |
35,00 |
82,00 |
66,16 |
155 |
2,34 |
|
4 |
40,00 |
69,00 |
89,28 |
154 |
1,73 |
|
5 |
55,00 |
63,00 |
133,57 |
153 |
1,15 |
|
6 |
70,00 |
55,00 |
190,91 |
150 |
0,79 |
|
7 |
80,00 |
50,00 |
257,60 |
161 |
0,63 |
|
8 |
90,00 |
50,00 |
291,60 |
162 |
0,56 |
|
9 |
15,00 |
111,00 |
15,68 |
116 |
7,40 |
|
10 |
15,00 |
99,00 |
24,70 |
163 |
6,60 |
|
11 |
20,00 |
92,00 |
35,65 |
164 |
4,60 |
|
12 |
15,00 |
100,00 |
24,00 |
160 |
6,67 |
|
13 |
15,00 |
100,00 |
25,50 |
170 |
6,67 |
|
14 |
20,00 |
87,00 |
34,94 |
152 |
4,35 |
|
15 |
15,00 |
95,00 |
24,47 |
155 |
6,33 |
|
16 |
15,00 |
99,00 |
24,24 |
160 |
6,60 |
|
17 |
25,00 |
85,00 |
52,35 |
178 |
3,40 |
|
18 |
15,00 |
87,00 |
28,45 |
165 |
5,80 |
|
19 |
15,00 |
95,00 |
23,68 |
150 |
6,33 |
|
20 |
20,00 |
81,00 |
37,28 |
151 |
4,05 |
|
21 |
15,00 |
98,00 |
23,27 |
152 |
6,53 |
|
22 |
15,00 |
92,00 |
24,95 |
153 |
6,13 |
|
23 |
20,00 |
88,00 |
35,00 |
154 |
4,40 |
|
24 |
15,00 |
96,00 |
24,22 |
155 |
6,40 |
|
25 |
20,00 |
87,00 |
35,86 |
156 |
4,35 |
Значение каждого показателя из матрицы исходных данных разделим на максимальное значение изучаемого показателя (1).
Например, по столбцу квалификация:
15/90≈0,17 (1)
(округлим до двух знаков после запятой). И остальные ячейки столбца делим на 90, как в примере. Затем в следующем столбце находим наибольшее число и проводим деление каждой ячейки на него.
Результаты полученных расчетов внесем в матрицу координат.
Значение каждого показателя в матрице координат возведем в квадрат и полученные данные внесем в матрицу квадратов.
Возведенные в квадрат данные по каждому показателю просуммируем по строке, т. е. по каждому изучаемому инженеру. Например, по инженеру под порядковым номером 1:
0,03 + 1,00 + 0,01+ 0,81 + 1,00 = 4,005
* - 1 месяц берется за 100 %
** - 300 листов формата А4 берется за 100%
*** - значение близкое к 0 – считается самым востребованным
В табл. 2 по сумме баллов присвоим призовое место каждому инженеру, однако здесь не учитывается значимость используемых оценочных показателей (все они считались равнозначными).
Таблица 2.
Матрица квадратов с ранжированием
Инженер |
Показатели эффективности |
Динамика |
Сумма баллов |
Ранжи-рование* |
|||
Квалификация |
Время вып. проекта |
Объем вып. А4 |
Рабочих часов в месяц |
Важность для отдела |
|||
1 |
2 |
3 |
4 |
5 |
6 |
7 |
8 |
1 |
0,03 |
1,00 |
0,01 |
0,81 |
1,00 |
2,84 |
21 |
2 |
0,08 |
0,75 |
0,02 |
0,77 |
0,27 |
1,88 |
6 |
3 |
0,15 |
0,54 |
0,05 |
0,76 |
0,10 |
1,60 |
2 |
4 |
0,20 |
0,38 |
0,09 |
0,75 |
0,05 |
1,47 |
1 |
5 |
0,37 |
0,32 |
0,21 |
0,74 |
0,02 |
1,66 |
3 |
1 |
2 |
3 |
4 |
5 |
6 |
7 |
8 |
6 |
0,60 |
0,24 |
0,43 |
0,71 |
0,01 |
2,00 |
9 |
7 |
0,79 |
0,20 |
0,78 |
0,82 |
0,01 |
2,60 |
20 |
8 |
1,00 |
0,20 |
1,00 |
0,83 |
0,01 |
3,03 |
22 |
9 |
0,03 |
0,98 |
0,00 |
0,42 |
0,98 |
2,42 |
17 |
10 |
0,03 |
0,78 |
0,01 |
0,84 |
0,78 |
2,44 |
18 |
11 |
0,05 |
0,67 |
0,02 |
0,85 |
0,36 |
1,95 |
8 |
12 |
0,03 |
0,80 |
0,01 |
0,81 |
0,80 |
2,44 |
18 |
13 |
0,03 |
0,80 |
0,01 |
0,91 |
0,80 |
2,54 |
19 |
14 |
0,05 |
0,60 |
0,01 |
0,73 |
0,34 |
1,74 |
4 |
15 |
0,03 |
0,72 |
0,01 |
0,76 |
0,72 |
2,23 |
13 |
16 |
0,03 |
0,78 |
0,01 |
0,81 |
0,78 |
2,40 |
16 |
17 |
0,08 |
0,58 |
0,03 |
1,00 |
0,21 |
1,89 |
7 |
18 |
0,03 |
0,60 |
0,01 |
0,86 |
0,60 |
2,10 |
10 |
19 |
0,03 |
0,72 |
0,01 |
0,71 |
0,72 |
2,18 |
12 |
20 |
0,05 |
0,52 |
0,02 |
0,72 |
0,29 |
1,60 |
2 |
21 |
0,03 |
0,77 |
0,01 |
0,73 |
0,76 |
2,29 |
15 |
22 |
0,03 |
0,67 |
0,00 |
0,74 |
0,67 |
2,11 |
11 |
23 |
0,05 |
0,62 |
0,01 |
0,75 |
0,68 |
2,10 |
10 |
24 |
0,03 |
0,73 |
0,01 |
0,76 |
0,73 |
2,26 |
14 |
25 |
0,05 |
0,60 |
0,02 |
0,77 |
0,37 |
1,80 |
5 |
*- 22 позиция имеет преимущество (лучшее место по сумме набранных баллов)
Для уточнения результатов присуждения призового места воспользуемся созданной эмпирическим путем экспертной оценкой значимости каждого взятого для расчетов показателя и заполним табл. 3.
Экспертная оценка получена эмпирическим путем с применением метода структурированного опроса инженеров-конструкторов со стажем работы в конструкторских бюро от 10 лет и больше.
Справка. Для оценки значимости показателя эксперты используют пятибалльную шкалу (Рис. 2):
№ |
Показатель |
Экспертная значимость |
1 |
Квалификация |
4 |
2 |
Время выполнения одного проекта |
5 |
3 |
Объем выпущенных А4 |
4,5 |
4 |
Рабочих часов в месяц |
3 |
5 |
Важность для отдела |
2 |
Взвесим данные из матрицы квадратов по бальной оценке каждого показателя и просуммируем полученные данные по каждому изучаемому инженеру (по строке). Например, по инженеру с порядковым номером 1:
0,17 ⋅ 4 + 1,00 ⋅ 5 + 0,07 ⋅ 4,5 + 0,9⋅ 3 + 1,00 ⋅ 2 = 9,60 (2)
Таблица 3.
Матрица взвешенных величин
Инженер |
Показатели эффективности |
Динамика |
Сумма баллов |
Ранжи-рование |
|||
Квали-фикация |
Время выполн. проекта |
Объем выпущ. Ф.А4 |
Рабочих часов в месяц |
Важность для отдела |
|||
1 |
2 |
3 |
4 |
5 |
6 |
7 |
8 |
1 |
0,12 |
5 |
0,05 |
2,43 |
2 |
9,60 |
23 |
2 |
0,32 |
3,75 |
0,09 |
2,31 |
0,54 |
7,01 |
11 |
3 |
0,6 |
2,7 |
0,23 |
2,28 |
0,2 |
6,01 |
3 |
4 |
0,8 |
1,9 |
0,41 |
2,25 |
0,1 |
5,46 |
1 |
5 |
1,48 |
1,6 |
0,95 |
2,22 |
0,04 |
6,29 |
5 |
6 |
2,4 |
1,2 |
1,94 |
2,13 |
0,02 |
7,69 |
16 |
7 |
3,16 |
1 |
3,51 |
2,46 |
0,02 |
10,15 |
24 |
8 |
4 |
1 |
4,50 |
2,49 |
0,02 |
12,01 |
25 |
9 |
0,12 |
4,9 |
0,00 |
1,26 |
1,96 |
8,24 |
21 |
10 |
0,12 |
3,9 |
0,05 |
2,52 |
1,56 |
8,15 |
19 |
11 |
0,2 |
3,35 |
0,09 |
2,55 |
0,72 |
6,91 |
8 |
12 |
0,12 |
4 |
0,05 |
2,43 |
1,6 |
8,20 |
20 |
13 |
0,12 |
4 |
0,05 |
2,73 |
1,6 |
8,50 |
22 |
14 |
0,2 |
3 |
0,05 |
2,19 |
0,68 |
6,12 |
4 |
15 |
0,12 |
3,6 |
0,05 |
2,28 |
1,44 |
7,49 |
14 |
16 |
0,12 |
3,9 |
0,05 |
2,43 |
1,56 |
8,06 |
18 |
17 |
0,32 |
2,9 |
0,14 |
3 |
0,42 |
6,78 |
7 |
18 |
0,12 |
3 |
0,05 |
2,58 |
1,2 |
6,95 |
9 |
19 |
0,12 |
3,6 |
0,05 |
2,13 |
1,44 |
7,34 |
13 |
20 |
0,2 |
2,6 |
0,09 |
2,16 |
0,58 |
5,63 |
2 |
21 |
0,12 |
3,85 |
0,05 |
2,19 |
1,52 |
7,73 |
17 |
22 |
0,12 |
3,35 |
0,00 |
2,22 |
1,34 |
7,03 |
12 |
23 |
0,2 |
3,1 |
0,05 |
2,25 |
1,36 |
6,96 |
10 |
24 |
0,12 |
3,65 |
0,05 |
2,28 |
1,46 |
7,56 |
15 |
25 |
0,2 |
3 |
0,09 |
2,31 |
0,74 |
6,34 |
6 |
Сравним призовые места, рассчитанные без экспертной оценки показателей, с призовыми местами, рассчитанными с учетом экспертной оценки, и заполним табл. 4.
Таблица 4.
Сравнительные данные призовых мест
Инженер |
Призовое место, (лучшее место: 25) |
|
Без учета экспертной оценки |
С учетом экспертной оценки по методу Делфи |
|
1 |
2 |
3 |
1 |
21 |
23 |
2 |
6 |
11 |
3 |
2 |
3 |
4 |
1 |
1 |
5 |
3 |
5 |
6 |
9 |
16 |
7 |
20 |
24 |
8 |
22 |
25 |
9 |
17 |
21 |
10 |
18 |
19 |
11 |
8 |
8 |
12 |
18 |
20 |
13 |
19 |
22 |
14 |
4 |
4 |
15 |
13 |
14 |
16 |
16 |
18 |
17 |
7 |
7 |
18 |
10 |
9 |
19 |
12 |
13 |
20 |
2 |
2 |
21 |
15 |
17 |
22 |
11 |
12 |
23 |
10 |
10 |
24 |
14 |
15 |
25 |
5 |
6 |
Коэффициент корреляции инженеров исходя из суммы присвоенных баллов равен 0,972025.
Зависимость полученных данных можно рассмотреть на графике снизу:
Рисунок 3. Корреляция полученных данных
Для продолжения работы по данной тематике проведем оценку узких мест в работе КБ, чтобы выявить наиболее загруженные группы с учетом квалификации участников и сложности выполняемых проектов. Это обнажит потенциально опасное соотношение квалификации и уровня сложности выполняемого проекта индивидуально по каждому сотруднику. Для оценки наиболее загруженных групп будет использована методика временных рядов. Она позволит увидеть какой из групп достается больше других заданий с повышенной сложностью. Имея в распоряжении статистические данные по производительности КБ за прошедший период, авторы на основе небольшой выборки рассчитают максимально возможную производительность на аналогичный период при условии, что состав конструкторов не будет изменяться по параметру квалификация в сторону снижения значения. На основании интегральной оценки результативности специалистов они будут расставляться по зонам ответственности исходя из приоритета текущих задач и сроков выполнения проектов в КБ. Это позволит обходиться минимальным количеством человек на один проект. А соотношение с реальными возможностями конструктора позволят экономить до 10-15% от фактически затрачиваемого времени на сегодняшний день при распределении работ по принципу свободный специалист получает ближайший по сроку сдачи проект.
Вывод
Для проведения сравнительной оценки 25 инженеров использовано пять оценочных показателей. Расчеты, проведенные с использованием метода математического анализа, показали, что более точное распределение мест дал анализ данных с применением экспертной оценки (метод Дельфи), где учтена значимость показателей, используемых для сравнительной оценки показателей инженеров.
Из проведенного факторного анализа показателей эффективности инженерных специалистов видно, что различие переменных можно сгладить с помощью нормирования и центрирования входящих данных. Это позволяет нам применять факторный анализ как метод исследования связей между случайными величинами на примере конструкторского бюро. При этом в сравнении с методом квадратов распределение имеет адекватное отклонения в сторону точности значений за счет более тонкой настройки.
