Разработка системы автоматического погрузочно-разгрузочного крана-штабелёра мостового типа
Журнал: Научный журнал «Студенческий форум» выпуск №6(99)
Рубрика: Технические науки
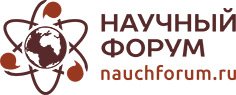
Научный журнал «Студенческий форум» выпуск №6(99)
Разработка системы автоматического погрузочно-разгрузочного крана-штабелёра мостового типа
Для полноценного обеспечения технологического процесса перегрузки товарных материальных ценностей (далее ТМЦ) установка должна отвечать следующим основным критериям: наличие системы противоаварийной защиты (ПАЗ), максимальная быстроходность установки, наличие самодиагностики, связь с информационной системой склада, энергоэффективность, удобство в эксплуатации установкой и ремонтопригодность.
Мостовой кран-штабелёр представляет собой мостовой двухбалочный кран, на тележке которого расположен вилочный поворотный подъёмник, собственно тот рабочий исполнительный механизм, осуществляющий подбор поддона с товаром. Рельсы опираются на стеллажи и жёстко закреплены на них.
Рисунок 1. Состав крана-штабелёра мостового типа
На рисунке 1 изображен кран-штабелёр: 1 – несущий рельс моста, 2 – мост двубалочный, 3 – поворотное подъёмное устройство, 4 – грузозахватный орган, 5 – шкаф автоматики и управления электроприводом. Электропривода на колёсных парах, опирающихся на продольный рельс 1, позволяют перемещаться установке по оси X, электропривода на колесных парах поперечных рельс 2 обеспечивают перемещение по оси Y. На борту тележки устанавливается поворотная колонна на силовом опорном подшипнике. Колонна снабжена электроприводом с редукторным выходом через планетарную передачу. Они образуют опорно-поворотное устройство (ОПУ), реализующее поворот в плоскости XY. На колонне располагается гидравлический подъёмник с цепным подвесом каретки, на которой закреплены вилы 4 – грузозахватный орган. Подъёмник осуществляет перемещение груза по оси Z. Выбор ступенчатого гидропривода с цепным подвесом каретки взамен электропривода с канатно-барабанным механизмом обусловлен бóльшим эксплуатационным ресурсом, что обусловлено отсутствием в нём трущегося каната. Все электроприводы снабжаются абсолютными многооборотными энкодерами (гидропривод снабжается резистивной путевой рейкой), которые точно позволяют высчитывать текущее положение исполнительных органов (ИО) каждой оси, концевыми выключателями (КВ) регистрирующими крайние положения ИО, КВ аварийные, регистрирующие выход за пределы крайние положения и отключающие питание ИО, а также КВ т.н. «нулевой позиции», относительно которой производится отчёт перемещений энкодерами. Сигналы этих датчиков заносятся в блоки распределённой периферии АСУ 5. После приёма сигналов с полевого уровня, информация о состоянии ИО передаётся центральному ЦПУ головного ПЛК крана. Вышеописанная система позволяет координированно перемещаться крану-штабелёру в нескольких плоскостях одновременно, что снижает время на перемещение в пространстве. Ориентирование крана относительно стеллажных ячеек производится за счёт наличия над каждой из ячеек маркированных наклеек с уникальным штрих кодом. Он считывается сканером штрих-кодов, который располагается на борту каретки. Около каждого штрих кода по бокам находятся светоотражающие катафоты. Они необходимы для того, чтобы спозиционировать каретку со сканером непосредственно перед штрих-кодом, затем на сканер подаётся сигнал на считывание и АСУ крана понимает, правильная ли ячейка выбрана для забора груза.
Инженерная система автоматизации в простейшем рассмотрении представлена на рисунке 2.
Рисунок 2. Топология АСУ ТП крана-штабелёра
Полевой уровень сбора данных с установки крана заканчивается на распределённых модулях ввода-вывода и ПЛК крана и ПЛК вводного шкафа управления. Они вместе с HMI-панелью связаны посредством интерфейса ETHERNET. Через промышленный коммутатор АСУ крана интегрирована в сеть предприятия, откуда берется информация о необходимых загрузках-выгрузках грузов склада. Инженерная станция позволяет удалённо контролировать и корректировать задачи крана, HMI-панель же – локально, непосредственно около территории склада.
