ОПЫТ ИСПОЛЬЗОВАНИЯ СТЕРЖНЕВОЙ КОМПОЗИТНОЙ АРМАТУРЫ ПРИ ИЗГОТОВЛЕНИИ РАЗЛИЧНЫХ ВИДОВ СТРОИТЕЛЬНЫХ КОНСТРУКЦИЙ И СООРУЖЕНИЙ
Журнал: Научный журнал «Студенческий форум» выпуск №15(324)
Рубрика: Технические науки
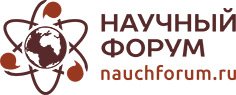
Научный журнал «Студенческий форум» выпуск №15(324)
ОПЫТ ИСПОЛЬЗОВАНИЯ СТЕРЖНЕВОЙ КОМПОЗИТНОЙ АРМАТУРЫ ПРИ ИЗГОТОВЛЕНИИ РАЗЛИЧНЫХ ВИДОВ СТРОИТЕЛЬНЫХ КОНСТРУКЦИЙ И СООРУЖЕНИЙ
Аннотация. Исследование раскрывает потенциал использования композитной арматуры как коррозионно-стойкой альтернативы стали, анализируя противоречия между её высокой прочностью (до 1500 МПа) и низким модулем упругости, обуславливающим повышенную деформативность конструкций. На примерах международной практики показано, что при двукратном удорожании материала эксплуатационные расходы снижаются на 35-40% за счет увеличения межремонтных циклов. Выявлены ключевые ограничения для массового внедрения: необходимость адаптации нормативной базы под анизотропные свойства полимеров и разработки гибридных армирующих систем для сейсмоопасных зон. Результаты подчеркивают трансформационный эффект композитов в проектировании морских и химических объектов, где долговечность превалирует над жесткостью.
Ключевые слова: композитная арматура, стеклопластиковые стержни, коррозионная стойкость, модуль упругости, гибридное армирование, жизненный цикл конструкций, предварительное напряжение, деформативность, нормативные стандарты.
В современной строительной индустрии наблюдается устойчивый переход к материалам, сочетающим высокие эксплуатационные характеристики с экологической и экономической эффективностью, что особенно актуально в контексте растущих требований к долговечности конструкций в условиях их работы в агрессивной среде и минимизации их углеродного следа [1]. Стержневая композитная арматура, созданная на основе полимерных матриц, армированных высокопрочными волокнами, постепенно вытесняет традиционные стальные аналоги, демонстрируя уникальные свойства, недостижимые для металлов [2]. Ее применение открывает новые горизонты в проектировании объектов, подверженных агрессивным воздействиям — от морских гидротехнических сооружений до мостовых переходов в регионах с суровыми климатическими условиями, где коррозия десятилетиями оставалась ключевым фактором деградации конструкций. Легкость материала не только упрощает логистику и монтаж, но и снижает нагрузку на фундаменты, позволяя реализовывать сложные архитектурные формы без компромиссов в надежности [3]. При этом сочетание высокой удельной прочности и упругой деформации композитов трансформирует подходы к расчету конструкций, смещая фокус с сопротивления пластическим деформациям на управление упругими характеристиками. Интеграция таких решений в нормативную базу и практику проектирования свидетельствует о формировании новой парадигмы в материаловедении, где синтез химии, физики и инженерии становится основой для создания инфраструктуры будущего.
Разработка стеклопластиковой и полимерной композитной арматуры стала ответом на эти вызовы: материалы на основе эпоксидных смол, армированных базальтовыми или стеклянными волокнами, демонстрируют не только коррозионную стойкость в 5-7 раз выше, чем у стали, но и уникальное сочетание высокой прочности на растяжение (до 1500 МПа) с низкой плотностью (в 4-5 раз легче металла) [4]. Пионерами в их промышленном производстве выступили США, Канада и Япония, где уже в 1980-х годах началось внедрение композитов в мостовые конструкции приморских регионов — например, при строительстве пешеходного моста Томоэгава в Японии с пролетами, армированными углепластиковыми стержнями, или реконструкции причальных стенок порта Ванкувера с использованием стеклопластиковых сеток [5] и других конструкций ( рис.1-3) [13] .
В Европе лидерство принадлежит Германии и Норвегии, применяющим композиты в тоннелях с высокой влажностью и объектах морской инфраструктуры, таких как волноломы Бергенского порта.
Ключевое отличие композитной арматуры от стальной заключается в анизотропии механических характеристик: при сопоставимой прочности на разрыв ее модуль упругости составляет 50-60 ГПа против 200 ГПа от стального, что приводит к увеличенным деформациям изгибаемых элементов под нагрузкой [6].
Рисунок 1 Набережная Блэкпул, Великобритания (2009 г.)
Рисунок 2. Вокзал ( Вена , Австрия) (2007-2008 г.г.)
Рисунок 3. Мост Irvine Creek (Онтарио, Канада), 2007 г.
Ключевое отличие композитной арматуры от стальной заключается в анизотропии механических характеристик: при сопоставимой прочности на разрыв ее модуль упругости составляет 50-60 ГПа против 200 ГПа от стального, что приводит к увеличенным деформациям изгибаемых элементов под нагрузкой [6].
Эксперименты с железобетонными балками, проведенные в Донском Государствынном Техническом Университете [2-4] показали, что замена стальной арматуры стеклопластиковой при равной площади сечения увеличивает прогибы в 2.1-2.7 раза, а ширину раскрытия трещин — на 40-60%. Это ограничивает ее применение в конструкциях, где жесткость критически важна: в неразрезных многопролетных мостах с динамическими нагрузками, каркасах высотных зданий в сейсмических регионах или элементах подкрановых путей промышленных цехов [9]. Например, в проекте небоскреба «Лахта Центр» в Санкт-Петербурге композитная арматура использовалась только в фундаментной плите, тогда как вертикальные несущие колонны сохранили традиционное стальное армирование из-за требований к устойчивости при ветровых воздействиях [10].
Технико-экономическая эффективность композитов наиболее ярко проявляется в специализированных объектах: очистных сооружениях с постоянным контактом с агрессивными стоками (заводы BMW в Германии), многослойных стеновых панелях с гибкими связями (жилой комплекс «Сколково Парк»), предварительно напряженных дорожных плитах с увеличенным сроком службы (автобан А-7 в Нидерландах) [11]. Снижение массы арматурного каркаса на 70-80% позволяет сократить расход бетона до 15%, а отсутствие необходимости в антикоррозийной обработке уменьшает трудозатраты на 20-25%, что подтверждается расчетами НИИЖБ им. А.А. Гвоздева для логистических центров в Московской области. При этом в сегменте массового жилищного строительства композиты пока уступают стали из-за высокой стоимости сырья: цена базальтопластикового стержня диаметром 10 мм превышает металлический аналог в 2.2-2.5 раза, хотя анализ жизненного цикла конструкций демонстрирует окупаемость за счет увеличения межремонтных интервалов [12].
Таблица 1.
Сравнение прочностных и деформативных характеристик стальной и стеклянной композитной арматур
Характеристика |
Композитная арматура |
Стальная арматура А500С |
Прочность на растяжение |
800-1500 МПа (зависит от типа волокна) |
500-650 МПа |
Модуль упругости |
45-60 ГПа (в 3-4 раза ниже стали) |
200 ГПа |
Коррозионная стойкость |
Устойчива к хлоридам, сульфатам, pH 3-11 |
Требует защитного слоя бетона ≥40 мм |
Деформативность |
Прогибы конструкций выше в 2.1-2.7 раза |
Пластические деформации обеспечивают перераспределение усилий |
Плотность |
1.9-2.1 г/см³ (на 75% легче) |
7.85 г/см³ |
Теплопроводность |
0.35-0.5 Вт/(м·К) (теплоизолирующие свойства) |
46 Вт/(м·К) (мостики холода) |
Электропроводность |
Диэлектрик (применение в ЛЭП, МРТ-кабинетах) |
Проводит ток |
Стоимость |
2.2-2.5× дороже (диаметр 10 мм) |
Базовый ценовой ориентир |
Оптимальные сферы применения |
• Морские сооружения (порт Берген, Норвегия) |
• Многоэтажное строительство («Лахта Центр») |
Примечания:
1. Данные приведены для стержней диаметром 8-12 мм
2. Стоимостные показатели актуальны для РФ и ЕС на 2023 г.
3. Технические параметры соответствуют ГОСТ 31938-2012 и EN 206
Анализ полувекового опыта применения от экспериментальных советских мостов до масштабных проектов вроде терминала аэропорта Осло-Гардермуэн демонстрирует парадоксальный дуализм материала: беспрецедентная устойчивость к химическим и климатическим воздействиям сочетается с повышенной чувствительностью к проектно-расчетным ошибкам. Если в морских дамбах Нидерландов композиты увеличили межремонтный цикл с 15 до 50 лет, то в сейсмически активных регионах Чили их применение в колоннах многоэтажек привело к недопустимым деформациям из-за недоучета ползучести полимерных матриц. Этот дисбаланс между потенциалом и рисками постепенно нивелируется по мере накопления эмпирических данных: разработка гибридных армирующих систем, где сталь компенсирует низкий модуль упругости композитов, а те, в свою очередь, защищают металл от коррозии, открывает путь для синергии материалов. Экономическая целесообразность, изначально ограниченная дороговизной базальтовых волокон, начинает смещаться в пользу полимеров благодаря замкнутым циклам переработки углепластиков и автоматизации плющения ровинга. Однако главным вызовом остается не технология, а инерция мышления: переход от пластических деформаций стали к хрупкому разрушению композитов требует переосмысления самих принципов обеспечения надежности, что уже находит отражение в пересмотре еврокодов и появлении первых BIM-библиотек с нелинейными моделями адгезии.
