Влияние основных технологических факторов на процесс спекания зольной шихты в аглопорит
Журнал: Научный журнал «Студенческий форум» выпуск №29(50)
Рубрика: Химия
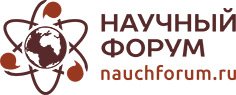
Научный журнал «Студенческий форум» выпуск №29(50)
Влияние основных технологических факторов на процесс спекания зольной шихты в аглопорит
Важными факторами, определяющим производительность агломерационной установки и качество готового продукта, являются процессы горения топлива в сырцовых гранулах и влияние температурного уровня процесса на структуру материала.
На основе результата процесса термообработки гранул, а так же в процессе их обжига может увеличиваться пористость слоя. Поэтому в результате в зоне охлаждения удельное гидравлическое сопротивление меньше, чем других зон. При этом повышение температуры зажигания верхнего слоя гранул без его расплавления позволяет усилить передачу тепла с верхнего слоя гранул к нижним слоям.
Как возможно объяснить влияние продолжительности обжига на показатели агломерации? Прежде всего это объясняется влиянием газовой среды в зажигательном горне. На каждый слой зажигаемых гранул в период внешнего нагрева поступает обедненный кислородом воздух. Недостаток кислорода замедляет скорость горения топлива, которые содержащегося в сырцовых гранулах в период внешнего нагрева. Когда по мере перемещения зоны горения от поверхности агломерируемого слоя до колосниковой решетки топливо начинает интенсивно выгорать в нагретом слое гранул лишь после прекращения подачи теплоносителя и температурно-тепловой режим спекания изменяется.
При разработке технологии производства аглопорита из золы ТЭС, прежде всего, встает вопрос о возможности получения термостойких и прочных гранул. Сырцовые гранулы не должны разрушаться при транспортировке и укладке на ленту агломашины, должны выдерживать давление вышележащих слоев шихты и не растрескиваться при термообработке.
Улучшение качества сырцовых гранул достигается введением в шихту добавок (суглинок, СДБ и др.), а также большое значение имеет содержание в шихте топлива. Избыток топлива приводит к сплавлению гранул в монолит. Оптимальное количество топлива, в первую очередь, зависит от плавкости сырья.
Данилов Б.П. считает, что при содержании в золе несгоревшего топлива более 25 %, следует вводить отощитель (глину и др.), а также им был получен аглопорит объемным весом 400–600 кг/м3, при содержании несгоревшего топлива в золе 10–30 %.
Несколько лет спустя, ВНИИстромом была проведена большая работа по поиску оптимального состава введения добавок в шихту, в зависимости от несгоревшего топлива в золе. С.Г. Васильков и М.П. Элинзон при содержании топлива 4 до 11 %, вводили глину, количество которой достигало 15–20 % веса золы. А при содержании 4,3–4,4 %) топлива, авторы на примере золы Иркутской ТЭЦ без дополнительного измельчения и без добавок получали аглопоритовый гравий. В работе приводятся результаты исследования, в которых указываются, что оптимальным значением содержания несгоревшего топлива является 6–8 %), а т.к. в золе Фрунзенской ТЭЦ количество топлива превышает этот оптимум, они вводили в шихту бестопливную добавку - белостолбовский суглинок в количестве от 5 % до 30 %. Суммарное содержание топлива при этом составляло 7,2–9,7 %). По их мнению, добавка в шихту суглинка способствует ускорению перемещения зоны горения топлива. Причем, чем больше в шихте доля бестопливной добавки, тем значительнее прирост вертикальной скорости процесса обжига, а также выше прочность аглопоритового гравия и насыпная плотность.
Большое влияние на ход процесса собственно обжига оказывает количество воздуха, просасываемого через слой гранул: с увеличением количества просасываемого воздуха скорость перемещения зоны горения возрастает. Коэффициент выхода при разрежении в период спекания 800, 1200 и 1600 Па составил соответственно 0,787, 0,764 и 0,637. Основываясь на этих результатах, авторы этой работы сделали вывод, что увеличение разрежения в период обжига, даже, несмотря на повышение скорости процесса, является нецелесообразным.
В. М. Уфимцев, М. Ф. Чебуков отмечают, что наличие в шихте 2 % топлива значительно улучшает условия обжига и повышает прочность аглопорита.
Область высоких температур позволяет расширить увеличение продолжительности внешнего нагрева верхнего слоя гранул. Тогда вследствии неравномерного горения твердого топлива в теле аглопорита формируется кавернозная структура. При рассмотрении рисунков 1–2,видно что при оптимальной температуре зажигания верхнего слоя гранул 1273 К и чрезмерной продолжительности обжига – 8 минут (рисунок 2) мы получили аглопорит, который представляет собой крупнопористый материал с насыпной плотностью 630–670 кг/м3. В результате так же можно сделать вывод и о том, что снижение продолжительности зажигания верхнего слоя гранул до оптимального уровня – 4 минут (рисунок 1) позволяет получить аглопорит с равномерной пористой структурой, без каверн. Значит, насыпная плотность аглопорита фракции 5–10 мм и 10–20 мм, снижается от 670 кг/м3 до 630 кг/м3 и от 630 кг/м3 до 570 кг/м3.
1 – расплав, 2 – монокристаллы силикатной фазы, 3 – поры
Рисунок. 1 Структура пористости аглопорита в зависимости от продолжительности зажигания верхнего слоя гранул при температуре 1273 К при продолжительности 6 мин
1 – расплав, 2 – монокристаллы силикатной фазы, 3 – поры
Рисунок. 2 Структура пористости аглопорита в зависимости от продолжительности зажигания верхнего слоя гранул при температуре 1273 К при продолжительности 8 мин
Вследствии изучения литературных данных, [1], определили, что отдельный элемент слоя (гранула) имеет две зоны: оболочку и ядро. Таким образом фазовый и химический состав этих зон различен. При выгорания углерода из гранулы в теле материала образуется различная газовая среда: в оболочке – окислительная, а в ядре восстановительная. Следует, на первых этапах низкотемпературной обработки (973–1173 К) в оболочке гранулы протекают процессы диссоциации и окисления железосодержащих минералов за счет диффузии кислорода воздуха. На этом периоде происходит разложение сидерита и гидроокиси железа по реакциям (1–3):
2FeOOH + O2 = Fe2O3 + Н2O (1)
3FeO + ½ O2 = Fe3O4 (2)
2FeCO3 + ½ O2 = Fe2O3 + СО (3)
В последствии прогрева оболочки гранулы до температуры 1073–1273 К начинается интенсивное горение коксового остатка, в результате чего в оболочке создается восстановительная атмосфера и происходит восстановление ранее окисленного железа по реакциям (4–5):
Fe2O3 + CO = 2Fe3O4 + CO2 (4)
Fe3O4 + CO = 3FeO + CO2 (5)
По причине существенного снижения вязкости образующегося расплава (за счет перехода Fe3+ в Fe2+ ) формируется тонкая пленка в зоне горения кокса. Образование такой оболочки затрудняет дальнейшую диффузию кислорода к ядру гранулы. Ширина оболочки при прочих равных условиях зависит от двух факторов: температуры и продолжительности обжига. Тогда повышение температуры обжига до 1373 К приводит к пиролизу коксового остатка ядра. И результатом пиролиза, является частичное восстановление оксидов железа в оболочке. Данный процесс происходит, так как при этой температуре ядро еще полностью не изолированно от оболочки образовавшимся расплавом. И в дальнейшем повышении температуры обжига, происходит расплавление минеральной части исходного сырья, а так же интенсивное образование расплава в оболочке [2].
