Легирование сплавов
Журнал: Научный журнал «Студенческий форум» выпуск №3(54)
Рубрика: Технические науки
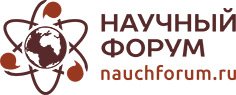
Научный журнал «Студенческий форум» выпуск №3(54)
Легирование сплавов
Легирование – это процесс введения в расплавленные или твердые металлы легирующих элементов с целью получения сплава заданного химического состава и придания ему требуемых механических, технологических или иных специальных свойств.
К легирующим элементам относят технически чистые элементы, вводимые в состав сплава в чистом виде или в составе лигатур. Таким образом, в состав сплава входят основа, легирующие элементы и примеси.
Примеси – это небольшие количества элементов, случайно попадающие в сплав из шихтовых материалов, топлива, атмосферы, шлаков, материала тигля или печи и т.д. Вредные примеси снижают свойства сплава. Их количество ограничивают государственными стандартами или техническими условиями. Остаточные примеси попадают в сплав либо при переплаве отходов, либо вторичных сплавов, а также после проведения некоторых металлургических обработок (модифицирования, раскисления, рафинирования).
Нейтральные примеси обычно не оказывают заметного влияния на основные свойства сплава и поэтому не контролируются в процессе производства сплавов[1].
В настоящее время ГОСТами предусмотрено около 200 литейных сплавов и свыше 400 литейных сплавов изготавливают по различным техническим условиям.
По техническим и экономическим параметрам выбирают группу легирующих элементов, которые целесообразно вводить совместно. Из этой группы легирующих элементов одни увеличивают механические или специальные, другие технологические или литейные свойства.
Выбор основы сплава определяется, прежде всего, условиями работы изделия из этого сплава и экономическими факторами. Например, для транспортных средств, особенно летательных аппаратов, требуется легкость. Поэтому при их конструировании многие детали изготавливаются из сплавов на основе алюминия, магния и титана. Для деталей, работающих при высоких температурах, в условиях интенсивного износа или коррозии требуются тугоплавкие, жаростойкие, коррозионностойкие и износостойкие сплавы на основе никеля, хрома, молибдена и других сплавов[2].
Выбор легирующих элементов производится по двойным диаграммам состояния основа сплава – легирующих элемент.
В настоящее время установлено, что существуют вполне определенные зависимости между параметрами диаграмм состояния и технологическими и эксплуатационными свойствами сплава, позволяющие выбрать оптимальный состав легирующих элементов.
Свойства сплавов зависят от того, какие соединения или фазы образовали компоненты сплава. Какие фазы образуются между компонентами сплава, устанавливается по диаграмме состояния. Поэтому, очевидно между видом диаграммы состояния и свойствами сплава существует определенная связь.
На рисунке 1 приводятся четыре основных типа диаграмм состояний и соответствующие им закономерности изменения свойств сплава с изменением концентрации.
При образовании механических смесей (рисунок 1, а) свойства сплава изменяются по линейному закону. Следовательно, значения свойств сплавов находятся в интервале между свойствами чистых компонентов А и В. При образовании твердых растворов (рисунок 1, б) свойства сплава изменяются по криволинейному закону, причем некоторые свойства (например, электросопротивление) могут значительно отличаться от свойств компонентов А и В. Распад раствора на две или более фазы ведет к повышению электропроводности.
При образовании ограниченных твердых растворов (рисунок 1, в) свойства сплавов в интервале концентраций, соответствующим однофазным твердым свойствами чистых фаз предельно насыщенных твердых растворов, образующих данную смесь.
Рисунок 1. Свойства сплавов и вид их диаграмм состояния (по Н.С. Курнакову)
Если образуются твердые растворы замещения, периоды решетки изменяются в зависимости от разности атомных диаметров растворенного элемента и растворителя.
В том случае, когда диаметр атома легирующего элемента больше диаметра атома растворителя – решетка увеличивается. Если диаметр атома легирующего элемента меньше диаметра атома растворителя решетка уменьшается. При образовании твердых растворов внедрения параметры решетки увеличиваются.
Установлено, чем больше изменение параметров решетки при легировании, тем значительнее изменяются свойства. Причем, уменьшение параметров решетки металла-основы ведет к большему упрочнению, чем ее расширение (рисунок 2).
Цинк, серебро и кремний незначительно изменяют параметр решетки алюминия. Поэтому следует ожидать лишь незначительного упрочнения металла (при этом структурные изменения не учитываются). Как видно из рисунка 2 медь и магний резко изменяют параметр решетки алюминия, вследствие этого его упрочнение происходит весьма значительно. Неслучайно медь и магний входят в состав самых высокопрочных алюминиевых сплавов.
При образовании химического соединения на диаграмме концентрация химического соединения отвечает максимуму (или минимуму) на кривой (рисунок 1, г) показан перелом прямой.
Следует отметить, что приведенные зависимости от вида диаграммы состояния не всегда подтверждаются опытом, так как в них не учитываются форма и размеры кристаллов, их взаимное расположение, температура и другие факторы.
Рисунок 2. Влияние легирующих элементов на изменение параметров решетки алюминия
На рисунке 3 показана схема зависимости между двойной диаграммой состояния и механическими свойствами сплава. На участке концентраций аб характеристики прочности всегда возрастают. В пределах этого участка термическая обработка не оказывает влияния на свойства. На участке бе прочность продолжает расти, а термическая обработка ее может значительно изменить. Считается, что воздействие закалки и старения тем сильнее, чем
больше искривлена линия предельной растворимости на диаграмме состояния бв. Если эта линия вертикальная прямая, после термической обработки упрочнение не увеличивается. При медленном охлаждении распад высокотемпературной фазы происходит с выделением грубых включений, и прочность незначительно возрастает при увеличении количества легирующего элемента.
Рисунок 3. Зависимость свойств сплава от диаграммы состояния
Пластичность сплава зависит не только от концентрации, но и от распределения добавки в структуре. Если коэффициент распределения мал, то легирующий элемент концентрируется по границам зерен и пластичность сплава резко падает даже при малых концентрациях добавки. При средних величинах коэффициента распределения (0,1–1,0 %) пластичность обычно снижается умеренно с увеличением количества легирующего элемента. Однако при введении некоторых добавок при коэффициенте распределения близком к единице пластичность растет одновременно с прочностью, достигая максимума на пределе растворимости[3].
Принято делить процессы введения добавок в сплав на монолегирование и комплексное легирование. Монолегированными сплавами называют такие, которые содержат кроме основы только один легирующий элемент. Это, как правило, самый эффективный элемент из ряда легирующих добавок. Такими сплавами являются силумины, двойные латуни, некоторые алюминиево-магниевые сплавы и другие. При выборе состава решающим является определение концентрации единственного легирующего элемента, нижний предел которого – концентрация на уровне примеси, а верхний зависит от природы сплава. Для высокотехнологичности сплава с невысокими требованиями к прочности это будет эвтектическая концентрация, а для сплава, от которого требуется высокая прочность – предельная растворимость. В связи с этим нецелесообразно в монолегированных сплавах применять малорастворимые добавки.
При оценке рациональной концентрации легирующего элемента большую роль играет ее стоимость. При стоимости добавки близкой к стоимости основы сплава или даже более низкой, целесообразно вводить ее до самых высоких концентраций. Для более дорогих добавок разумно введение при умеренных концентрациях[1].
Одновременное введение в сплав нескольких легирующих элементов считается комплексным легированием. Подобные элементы могут быть взяты из одного или нескольких рядов легирующих элементов. Такую группу добавок называют легирующим комплексом.
Целесообразность и необходимость комплексного легирования определяется требованием одновременного обеспечения определенного уровня нескольких свойств сплава, снижением отрицательного влияния вредных примесей и некоторых легирующих добавок, а также возможным изменением свойств сплава вследствие взаимодействия между собой или основой двух или более легирующих элементов [3].
