Классификация методов создания износостойких покрытий
Журнал: Научный журнал «Студенческий форум» выпуск №13(64)
Рубрика: Технические науки
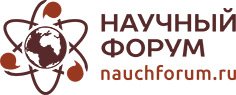
Научный журнал «Студенческий форум» выпуск №13(64)
Классификация методов создания износостойких покрытий
Аннотация. В статье рассмотрены наиболее известные методы нанесения износостойких покрытий на поверхности деталей. Проведен анализ сильных и слабых сторон. Знание каждой технологии позволит сделать правильный выбор при примении ее в производстве, что может продлить жизнь изделия в разы, практически не увеличивая его стоимости. Защитные и износостойкие покрытия обеспечивают возможность создания новых изделий-композиций, сочетающих высокую долговечность с достаточной надежностью, повышают эксплуатационную стойкость деталей машин и инструментов по сравнению со стойкостью, достигаемой известными способами термической обработки позволяют восстанавливать изношенную поверхность и, следовательно, снижают потребности в запасных частях.
Ключевые слова: износостойкие покрытия, термические методы, термомеханические методы, адгезионные методы.
В настоящем времени используются десятки методов нанесения покрытий на поверхность деталей машин. Технологических способов реализации этих методов применительно к определённым конкретным узлам и деталям значительно больше. Но, несмотря на такое разнообразие имеющихся способов нанесения покрытий, их все можно разделить на ряд групп, различающихся видами используемой энергии, обеспечивающей сцепление слоя с металлом. Различают (Рисунок 1): термические методы, оказывающие интенсивное тепловое воздействие на металл изделия и присадочный материал; термомеханические методы, включащие нагрев и механическое воздействие при формировании слоя на поверхности детали; адгезионные методы, при которых взаимодействие присадочного материала с поверхностью протекает в результате реализации физической и химической адсорбции.
Термические способы нанесения покрытий базируются преимущественно на технологиях наплавки. При данном методе металл, формирующий поверхностный слой, подвергается интенсивному нагреву, вызывающему его плавление. Формирование большого объема жидкого металла, полученного в результате плавления металла детали и присадочного материала, является отличительной особенностью наплавочных процессов. Образующаяся жидкая фаза активно смачивает не расплавившуюся поверхность, обеспечивая при последующей кристаллизации формирование однородной кристаллической решетки.
Рисунок 1. Классификация методов нанесения покрытий
Наплавочные технологии обеспечивают максимальную прочность сцепления поверхностного слоя с основой детали. Высокая энергоемкость определяет их значительную производительность. Наплавкой получают поверхностные слои толщиной от 0,5 до 20 мм. Максимально возможная высота наплавленного слоя в теории ничем не ограничена, но на практике слои толщиной более 20 мм не наплавляют.
В то же время интенсивный нагрев, свойственный наплавочным процессам, вызывает ряд отрицательных последствий. К числу таких последствий могут быть отнесены: неэффективный нагрев металла детали, не участвующего в формировании износостойкого слоя, что ограничивает размеры деталей, способных выдержать наплавочный процесс; разбавление высоколегированного присадочного металла низколегированным основным, что приводит к потере эксплуатационных характеристик; получение грубой чешуйчатой поверхности и значительный припуск на последующую механическую обработку.
Наплавочные технологии различаются по виду используемых источников нагрева. Электродуговые методы наплавки включают в свой состав широкий перечень технологий: ручная дуговая наплавка – используется при нанесении высоколегированных покрытий на детали сложной конфигурации с толщиной стенки от 3 мм; электродуговая наплавка под флюсом – применяется для деталей диаметром более 50 мм. Толщина наплавленного слоя изменяется от 2 до 10 мм; электродуговая наплавка в углекислом газе – выполняется на деталях диаметром от 20 мм, работающих в различных условиях; электродуговая наплавка в среде инертных газов – применяется для нанесения высоколегированных присадочных материалов, вибродуговая наплавка – используется для деталей малых размеров (диаметром от 10 мм). Обеспечивает невысокий уровень сопротивления усталости, поэтому не применяется для восстановления деталей, испытывающих значительные динамические нагрузки, например коленчатых валов.
Плазменно-дуговая наплавка используется при нанесении покрытий на ответственные детали при повышенных требованиях к износостойкости, сопротивлению усталости полученных слоев. Использует теплоту, выделяемую сжатой электрической дугой, совмещенной с плазменной струей, что обеспечивает высокую производительность технологического процесса.
Газовая наплавка – основана на использовании теплоты, выделяемой при сгорании горючего вещества в среде технически чистого кислорода. Относится к ручным методам наплавки и применяется для цилиндрических и профильных поверхностей с местным износом. Используется, как правило, на деталях малой толщины, обеспечивая формирование небольших по высоте слоев.
Электрошлаковая наплавка – является наиболее производительным методом наплавки и применяется для деталей со значительными износами. Формирование наплавленного слоя идет в один проход независимо от требуемой толщины слоя за счет теплоты, выделяемой при прохождении тока через ванну расплавленного шлака.
Лазерная и электроннолучевая наплавки – относятся к технологиям, использующим высококонцентрированные источники нагрева. Это определяет довольно высокие скорости нагрева, обеспечивающие минимальные размеры зоны термического влияния в металле детали, что позволяет вести наплавку на ответственные детали и детали сложного профиля.
Индукционная или высокочастотная наплавка – осуществляется путем нагрева присадочного материала и поверхности детали индукционными токами. Применяется для нанесения износостойких материалов на определённые участки деталей при местных износах, например рабочие органы, лезвия, проушины и др.
Заливка жидким металлом – также относится к термическим видам нанесения покрытий, при которых нагрев присадочного материала производится отдельно от самой детали. Применяется для деталей со значительными износами (не менее 3 мм) при повышенных требованиях к износостойкости и пониженных требованиях к ударной вязкости.
Термомеханические способы создания поверхностных слоев совмещают в процессе формирования и нагрев, и механическое усилие. Это позволяет снизить тепловложение в металл детали и значительно сократить долевое участие основного металла в поверхностном слое. Кроме того, механическое воздействие способствует выходу газов в процессе формирования слоя, снижению его пористости и улучшению качества формируемой поверхности. Но сокращение тепловой энергии, вводимой в зону формирования поверхностного слоя, снижает степень разогрева присадочного материала и ухудшает его сцепление с поверхностью детали. В результате чего часть металлических связей между частицами присадочного материала заменяется адгезионными, увеличивается роль подготовки поверхности детали для обеспечения требуемого качества нанесения покрытий. Технологии напыления характеризуются минимальным тепловложением в поверхностный металл детали. Присадочный материал при этом нагревается до температур, обеспечивающих его пластификацию, но плавление и переход в жидкую фазу не происходят. В таком состоянии частицы присадочного материала с высокой скоростью переносятся на поверхность, где при соударении деформируются и образуют напыленные слои. Малое тепловложение позволяет наносить слои на мелкие изделия с малой толщиной стенки. При этом толщина напыленного слоя находится в пределах от 0,01 до 3,0 мм. Характерной особенностью является то, что полученный слой, обладая высокими значениями твердости и износостойкости, не увеличивает прочность детали по сечению.
В зависимости от источника нагрева различают: газопламенное напыление порошковыми материалами применяемое для наружных и внутренних цилиндрических поверхностей, при невысоких требованиях к прочности сцепления с основным материалом; плазменное напыление – формирующее высоколегированные слои на наружных и внутренних цилиндрических и плоских поверхностях; индукционное напыление – осуществляемое генератором тока высокой частоты и позволяющее создавать покрытия повышенной плотности при минимальном выгорании легирующих элементов; детонационное напыление – при котором основным энергетическим воздействием на присадочный материал является ударное воздействие. Это сводит к минимуму роль нагрева и обеспечивает высокую плотность и качество. Применяется при нанесении износостойких покрытий с особыми свойствами.
Технологии металлизации по своим характеристикам близки к технологиям напыления, но при этом обладают более интенсивным тепловым воздействием на присадочный материал. При данном способе присадочный материал нагревается до жидкого состояния и затем в виде капель с большой скоростью подается на поверхность, вызывая ее некоторый разогрев. Перевод присадочного материала в жидкое состояние снижает пористость слоя и увеличивает долю металлических связей при сцеплении с поверхностью и внутри самого слоя, но, полученная прочность таких слоев все равно уступает прочности монолитного металла.
В зависимости от источника нагрева различают электродуговую, газопламенную и плазменно-дуговую металлизацию. Технологическим отличием от аналогичных методов напыления является возможность применения в качестве присадочного материала проволок и прутков.
Электроконтактная наварка – использует термическое воздействие при формировании поверхностного слоя. При данном методе плавлению подвергается как присадочный материал, так и металл детали. Объем расплавленного металла весьма невелик, а его кристаллизация протекает под действием механического усилия. Используемая в качестве присадочного материала лента подвергается нагреву и плавлению не по всей толщине, а лишь только в месте контакта с поверхностью детали.
Применяется при нанесении покрытий на гладкие цилиндрические и плоские наружные и внутренние поверхности, толщину создаваемого слоя можно регулировать в пределах 0,2-1,5 мм, зона термического влияния не превышает 0,5 мм. К недостаткам следует отнести отсутствие сплавления в отдельных местах ленты с основным металлом, которое выявляется при шлифовании.
Технологии механо-термического формирования вместе с термическим фактором используют механическое воздействие внешней нагрузки, что в комплексе способствует получению слоя с более высоким качеством.
Адгезионные (гальванические покрытия) получают путем осаждения требуемого металла на поверхность детали из раствора электролита совмещённо с наложением электрического тока или без него. Гальванические процессы имеют ряд преимуществ: позволяют наносить тонкие покрытия равномерной толщины от 0,05 до 0,5 мм с различной твердостью и различной износостойкостью; не ухудшают структуру основного металла, поскольку он в процессе наращивания остается холодным; позволяют одновременно обрабатывать большую группу деталей.
В то же время этим способам присущи ряд недостатков: значительная сложность и большой объем работ при выполнении технологических процессов, низкая скорость электролитического осаждения, снижение сопротивления усталости деталей, загрязнение окружающей среды. Гальванические покрытия отличаются адгезионным характером связи с основой. Это определяет низкую прочность сцепления с поверхностью детали.
Наиболее широкое применение нашли процессы хромирования, железнения, никелирования, применяемые для наружных и внутренних поверхностей деталей с износом, не превышающим 0,2-0,5 мм, высокой поверхностной твердостью и при нежестких требованиях к прочности сцепления покрытия с основным металлом.
Список литературы:
