ВЫБОР МЕТОДА ПОКРЫТИЯ ДЕТАЛИ «КОРПУС» С ЦЕЛЬЮ ПОВЫШЕНИЕ РЕСУРСА
Конференция: CLXV Студенческая международная научно-практическая конференция «Молодежный научный форум»
Секция: Технические науки
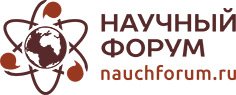
CLXV Студенческая международная научно-практическая конференция «Молодежный научный форум»
ВЫБОР МЕТОДА ПОКРЫТИЯ ДЕТАЛИ «КОРПУС» С ЦЕЛЬЮ ПОВЫШЕНИЕ РЕСУРСА
Деталь «Корпус» применяется в приборостроении, имеет сложную конфигурацию и высокие требования по точности к исполнительным поверхностям. Изготавливается из алюминиевого сплава Д16 ГОСТ 4784-2019.
Деталь имеет призматическую форму с габаритными размерами 190×149×80 мм. Деталь является полой, в ней выполнено большое число окон и пазов для установки датчиков и других устройств. Данные окна и пазы оснащены крепежными резьбовыми отверстиями с точным взаимным расположением. Для повышения жесткости конструкции детали «Корпус» предусмотрены ребра жесткости и усиления. Чертеж детали «Корпус» и 3D модель детали «Корпус» представлены на рисунках 1, 2 и 3 соответственно.
В качестве защитного покрытия исполнительных поверхностей детали «Корпус» использовалось химическое оксидирование Хим. Окс. ГОСТ 9.306-85 толщиной 3…4 мкм. Покрытие наносилось по действующей на базовом предприятии технологии [1, с.28] в водном растворе карбоната натрия Na2СО3 (50 г/л) с добавлением 15 г/л хромата натрия Na2Cr4 и 2,5 г/л гидроксида натрия NaOH. Оксидирование проводится при температуре 90оС в течении 10 минут. Покрытие детали «Корпус» должна успешно противостоять коррозии согласно ГОСТ 9.031-74 с образованием очагов коррозионных поражений площадью не более 0,1%.
Рисунок 1. Фрагмент чертежа детали «Корпус» (вид спереди и снизу)
Рисунок 2. Фрагмент чертежа детали «Корпус» (вид справа и слева)
Рисунок 3. 3D модель детали «Корпус»
При эксплуатации детали «Корпус» под действием окружающей среды произошло значительное уменьшение ресурса детали (до 30%).
На исполнительных поверхностях с покрытием наблюдались значительные по интенсивности коррозионные поражения, приводящие к отказам и снижению ресурса детали «Корпус». Опыт эксплуатации детали «Корпус» позволил прийти к выводу, что метод получения покрытия Хим. Окс. не обеспечивает требуемых защитных свойств. В результате коррозии происходят отказы прибора, в который входит деталь «Корпус», что значительно снижает ресурс изделия.
Автором принято решение изменить способ нанесения покрытия с химического оксидирования на анодное оксидирование методом МДО (микродугового оксидирования).
Режимы МДО были выбраны по данным исследования [2, с.112] и представлены в таблице 1.
Таблица 1.
Режимы нанесения покрытия
Параметр |
Значение параметра |
Состав раствора , г/л: H2O H2SO4 H3PO4 |
700 150 150 |
Температура, оС |
25…30 |
Толщина защитной пленки, мкм |
10…15 |
Время |
15…20 |
Напряжение, В |
14…20 |
Плотность тока, А/дм2 |
0,9…1,5 |
Скорость формирования покрытия, мкм/ч |
30 |
Для подтверждения правильности решения по изменению способа нанесения покрытия проведены сравнительные испытания коррозионной стойкости поверхностей детали «Корпус» по ГОСТ 9.031-74 при обработке в кислых растворах. Для этого изготовлены образцы детали «Корпус» с покрытиями, полученными методом химического оксидирования и МДО.
При испытании было выявлено значительное снижение показателя потери массы ρ с 20…21 мг/дм2 до 14…16 мг/дм2, что свидетельствует о повышении коррозионной стойкости до 1,5 раза.
Исследования также показали увеличение толщины покрытия с 6…8 до 13…15 мкм, что увеличивает его ресурс и ресурс детали «Корпус» в целом. Эти данные подтвердились результатами натурных испытаний. При эксплуатации детали «Корпус» в составе прибора отмечено увеличение ресурса всего изделия на 40…45% при применении метода химического оксидирования и МДО для получения покрытия.
