МИКРОТВЕРДОСТЬ И МИКРОСТРУКТУРА Al+TiO2, ОБРАБОТАННОГО МЕТОДОМ ТРЕНИЯ С ПЕРЕМЕШИВАНИЕМ
Конференция: CCLXIX Студенческая международная научно-практическая конференция «Молодежный научный форум»
Секция: Физико-математические науки
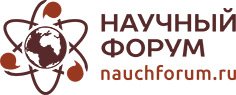
CCLXIX Студенческая международная научно-практическая конференция «Молодежный научный форум»
МИКРОТВЕРДОСТЬ И МИКРОСТРУКТУРА Al+TiO2, ОБРАБОТАННОГО МЕТОДОМ ТРЕНИЯ С ПЕРЕМЕШИВАНИЕМ
Алюминиевые сплавы широко используются в авиационной, автомобильной и судостроительной промышленности благодаря их прочности и небольшому весу. Однако эти сплавы имеют недостаточную износостойкость. Чтобы улучшить свойства алюминиевых сплавов, можно добавлять армирующие частицы, что приводит к созданию металломатричных композитов (ММК). В последнее время использование ММК расширилось благодаря повышению их механических свойств и износостойкости. Обычно ММК производятся методом ex-situ, когда армирующие частицы заранее добавляются в матрицу металла. Недостатком этого метода является необходимость хорошего перемешивания расплава из-за низкой смачиваемости частиц. Также возможны реакции между частицами и матрицей, что ухудшает механические свойства ММК. В настоящее время все большую популярность получают in-situ композитные технологии, при которых упрочняющие частицы синтезируются прямо в процессе смешивания компонентов композита. Такие технологии позволяют достичь более плотного контакта между матрицей и частицами, а также снизить загрязнения. Одной из перспективных технологий для получения композитов является отп. В отличие от ММК, полученных другими методами, отп отличается простотой и надежностью изготовления изделий, так как процесс осуществляется без плавления материала и способствует улучшению механических свойств за счет измельчения микроструктуры.
Использован лист алюминиевого сплава 6063 толщиной 3 мм, а также мелкодисперсный порошок TiO2. На фрезерном станке было вырезано 6 канавок, каждая из них имела ширину 1 мм, глубину 1,5 мм и длину 90 мм. Расстояние между канавками составляло 1,5 мм. После этого в эти канавки был насыпан и плотно утрамбован порошок TiO2, согласно рисунку 1. Многопроходная операция отп проводилась с выдвинутым на 2 мм наконечником. Количество проходов составляло 2, 4, 10 и 20, подготовлены образцы для металлографического анализа.
Микротвердость была исследована на шлифах, которые были вырезаны поперек плоскости шва с использованием электроискрового станка. Измерения микротвердости по Виккерсу проводились с использованием микротвердомера МВТ-71У4.2 при нагрузке 50 гс и времени выдержки 10 секунд. Микротвердость была измерена вдоль линии, которая находилась на расстоянии примерно 0,5 мм от поверхности контакта с инструментом.
Исследование микроструктуры было проведено с использованием растрового электронного микроскопа Tescan Vega.
В зоне перемешивания/композита Al+TiO2 не наблюдается фазовых превращений. Температура начала плавления композита осталась почти такой же, как и для алюминиевого сплава 6063. В состоянии поставки материал находится в дисперсионно-упрочненном состоянии с микротвердостью около 80 HV. ОТП (рис.1) приводит к уменьшению микротвердости в зонах термомеханического воздействия и перемешивания, что связано с сильным разогревом.
Рисунок.1. Распределение микротвердости в зоне ОТП композита Аl+TiO2
Наблюдается небольшое увеличение микротвердости по мере увеличения количества проходов с 4 до 20. После 2-х проходов отп формируются участки повышенной микротвердости (до 67 HV). Повышенная микротвердость наблюдается в участках с высокой плотностью частиц TiO2. В участках с низкой плотностью частиц твердость снижается до 43 HV. После четырех проходов твердость распределена более равномерно, но ее значение уменьшилось до 38 – 52 HV. Увеличение количества проходов отп до 20 не приводит к изменению микроструктуры. Средний размер зерен после 10 и 20 проходов составляет 3–5 мкм. На рис.2, показана зависимость усредненной микротвёрдости в зоне композита от количества проходов ОТП. Видно, что наибольшая микротвердость наблюдалась после 2 и 20 проходов, а минимальная после 4 проходов.
Рисунок.2. Зависимость значения микротвёрдости от количества проходов в зоне перемешивания
В результате исследования выяснилось, что в композите al+tio2 не происходит фазовых превращений при перемешивании. Температура плавления композита остается такой же, как у сплава 6063. В упрочненном состоянии материал имеет микротвердость около 80 hv. При отпуске микротвердость уменьшается в областях термомеханического воздействия и перемешивания из-за сильного разогрева. При увеличении числа проходов отп происходит небольшое повышение микротвердости. После 2 проходов отп образуются участки повышенной микротвердости (до 67 hv) в областях с высокой плотностью частиц tio2. В областях с низкой плотностью твердость снижается до 43 hv. После 4 проходов твердость распределяется более равномерно, но ее значение уменьшается до 38-52 hv. Увеличение числа проходов до 20 не влияет на микроструктуру. Средний размер зерен после 10 и 20 проходов составляет 3-5 мкм. Плотность частиц TIO2 уменьшается после 20 проходов из-за увеличения площади композита.
