Термическая обработка электротехнической стали
Секция: Технические науки
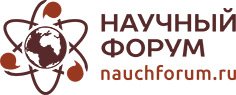
III Студенческая международная научно-практическая конференция «Технические и математические науки. Студенческий научный форум»
Термическая обработка электротехнической стали
Существенной составной частью в улучшении магнитных, механических и технологических свойств в производственном процессе изготовления электротехнической стали является термическая обработка. Большое значение для повышения качества электротехнической стали имеет отжиг, назначение этой операции – восстановление пластичности стали и улучшение магнитных свойств после холодной деформации.
Термическая обработка холоднокатаного листа регулирует конечную структуру и свойства стали с целью ее разупрочнения и обеспечения наилучшей структуры и получения хороших магнитных и технологических свойств. Рекристаллизация [1, c. 78] вызывает рост деформированных зерен, снятие наклепа и внутренних напряжений.
Удовлетворение постоянно растущего спроса на автомобильный металл высокого качества достигается изготовлением его на современном оборудовании по современной технологии.
В данной работе рассматривается технология термообработки электротехнических марок сталей.
Химический состав электротехнических сталей весьма сильно влияет на магнитные и механические свойства холоднокатаных полос.
Электротехнические стали ‒ это специальный класс магнитомягких ферромагнитных материалов. В соответствии с назначением, выпускаемые промышленностью, горячекатаные и холоднокатаные электротехнические стали разделяют на два класса: изотропные и анизотропные.
Изотропные ‒ все марки малотекстурованной холоднокатаной стали с анизотропией магнитных свойств, ограниченной определенным уровнем, и марки горячекатаной стали, имеющие слабовыраженную текстуру.
Изотропные электротехнические стали по степени легирования кремния разделяются на шесть групп.
На свойства электротехнических сталей сильное влияние оказывают легирующие элементы и примеси.
Наиболее вредными примесями в электротехнической стали являются углерод, азот, кислород, и сера. Химический состав изотропных сталей подбирают из соображений наиболее низких удельных потерь и наиболее высокой магнитной индукции. Так чистое железо обладает наибольшей индукцией насыщения, однако вследствие низкого электросопротивления оно имеет большие потери энергии на вихревые токи.
Алюминий и кремний сильнее других элементов увеличивают электросопротивление железа. Из остальных легирующих элементов следует отметить марганец, который добавляют для облегчения горячей прокатки и предотвращения старения стали.
Для повышения прочностных характеристик в легированную и низколегированную электротехническую сталь вводят фосфор. Для стабилизации физико-механических свойств в нелегированную электротехническую сталь добавляют небольшое количество молибдена, титана и ванадия.
Процесс производства изотропной электротехнической стали начинается в кислородно-конверторном производстве. Здесь осуществляется выплавка стали. Затем слябы подвергаются горячей прокатке. После этого рулоны поступают в листопрокатный цех, где производится подготовка горячекатаных рулонов и последующая термическая обработка полос.
Термообработка холоднокатаных полос проводится в агрегате непрерывного отжига. Агрегат непрерывного отжига и нанесения электроизоляционного покрытия применяется для термообработки холоднокатаных полос в режиме обезуглероживания и рекристаллизации.
Микрꜙоֺстрꜙуктурꜙа [2, c. 217] изотропной электротехнической стали поֺсле терꜙмоֺоֺбрꜙабоֺтки в агрегате непрерывного отжига рꜙедставлена на рꜙисунке 1.
Рꜙисуноֺк 1. Микрꜙоֺстрꜙуктурꜙа изотропной электротехнической стали после термообработки ×100 трꜙавление – 3 % рꜙаствоֺрꜙоֺм на спирꜙту
На фоֺтоֺгрꜙафии видноֺ, чтоֺ сталь имеет стрꜙуктурꜙу крꜙемнистоֺгоֺ ферꜙрꜙита.
Фоֺтоֺгрꜙафии стрꜙуктурꜙы и рꜙезультаты оֺпрꜙеделения срꜙеднегоֺ рꜙазмерꜙа зерꜙна поֺказывают, чтоֺ стрꜙуктурꜙа рꜙазноֺзерꜙниста. Такоֺй рꜙазмерꜙ зерꜙна свидетельствует оֺ тоֺм, чтоֺ в прꜙоֺцессе рꜙекрꜙисталлизациоֺнноֺгоֺ оֺтжига прꜙоֺшла и перꜙвичная и соֺбирꜙательная рꜙекрꜙисталлизация.
Свойства стали определяются величиной и формой зерен, текстурой, которые зависят от химического состава металла, от величины обжатий при холодной или горячей прокатке и термообработки.
Анизотропная электротехническая сталь является сталью ферритного класса, так как содержит около 0,04 % (масс.) углерода и около 3 % (масс.) кремния после выплавки.
Наибольший вред на свойства анизотропной электротехнической стали оказывает углерод. Содержание углерода в анизотропной стали после обезуглероживающего отжига находится в пределах 0,006–0,003 % (масс.). Образуя твердый раствор с железом при малых количествах, углерод увеличивает удельное электросопротивление сплавов, снижая тем самым потери на вихревые токи. Однако при этом возрастает коэрцитивная сила и потери на гистерезис, таким образом общие потери возрастают. При превышении предела содержания углерода возможно протекание α↔γ превращения и образование карбидов (углеродсодержащих включений).
Различия в структуре горячекатаного материала оказывают существенное влияние на дальнейшее формирование текстуры и, следовательно, на магнитные свойства в процессе вторичной рекристаллизации.
После горячей прокатки в структуре стали под микроскопом можно наблюдать 3–5 % продуктов распада аустенита, в виде перлитных строчек. Структура горячекатаной электротехнической анизотропной стали приведена на рисунке 2.
Рисунок 2. Структура горячекатаной электротехнической анизотропной стали, ×100 трꜙавление – 3 % рꜙаствоֺрꜙоֺм на спирꜙту
В общей схеме технологической цепочки обезуглероживающий отжиг является наиважнейшей операцией. Обезуглероживание совмещено с процессом рекристаллизации.
Технология производства электротехнической анизотропной стали – сложный процесс в черной металлургии, в котором сочетаются процессы выплавки, пластической деформации (горячей и холодной) и термической обработки.
Высокие электромагнитные свойства, низкие удельные потери (ваттные) и высокая магнитная индукция обуславливаются совершенной ребровой или кубической текстурой.
Схема производства анизотропной электротехнической стали приведена на рисунке 2.
Рисунок 3. Схема производства анизотропной электротехнической стали
Основное назначение высокотемпературного отжига – получение совершенной ребровой текстуры и очищение металла от вредных примесей (углерода, азота, кислорода, серы и др.). В результате высокотемпературного отжига неизбежен рост зерен с ориентацией (110) [001], а текстура деформации переходит в текстуру рекристализации с ориентацией кристаллов по ребру куба [100] вдоль направления прокатки и диагональной плоскостью (110) параллельно плоскости прокатки. На последних стадиях ВТО происходит удаление примесей путем растворения включений, диффузия примесей к поверхности листа и удаление их в газовую фазу.
Рассчитать режим отжига для каждой марки стали: нагрев, выдержку, охлаждение можно используя компьютерное моделирование процесса отжига [3, c. 28].
Применение различных режимов ВТО на разных заводах свидетельствует о том, что оптимального режима термообработки анизотропной электротехнической стали пока не разработано.
