Проектирование гибкого производственного модуля на базе фрезерных станков с ЧПУ HERMLE C40U
Секция: Технические науки
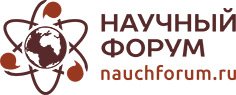
XXXIII Студенческая международная научно-практическая конференция «Технические и математические науки. Студенческий научный форум»
Проектирование гибкого производственного модуля на базе фрезерных станков с ЧПУ HERMLE C40U
Технический прогресс в машиностроении во многом определяет развитие всего хозяйства страны. Происходит запрос не только на увеличение объемов производства, но и на увеличение числа номенклатур выпускаемых изделий, к которым предъявляются высокие требования к точности и качеству изготовления, надежности при эксплуатации.
Однако увеличение темпа и объема производства влечет за собой увеличение загрузки оборудования, увеличение парка станков, увеличение числа рабочих, работу во вторую и третью смену. Современное оборудование нуждается в рабочих с высоким уровнем подготовки и высокой квалификацией, что в свою очередь требует увеличение затрат на заработную плату. А так же нехватка подготовленных кадров затрудняет организацию работы во вторую и третью смены. Поэтому перед машиностроительными предприятиями возникает непростая задача: увеличивать темпы и объемы выпуска продукции с минимальными затратами на привлечение дополнительного персонала и увеличения числа применяемого оборудования.
Одним из способов повышения эффективности машиностроительного производства является автоматизация. Благодаря автоматизации снижается участие человека в производственных процессах, возрастают объемы производства, улучшается качество продукции и условия работы персонала, увеличиваются экономические показатели производства. Одним из вариантов автоматизации производства является гибкий производственный модуль (ГПМ). Гибкий производственный модуль обычно организовывается на базе многоцелевого станка с ЧПУ и является дальнейшим развитием оборудования с целью повышения степени автоматизации и производительности при сохранении высокой гибкости. ГПМ может встраиваться как в гибкую производственную систему (ГПС), как и быть самостоятельной производственной единицей.
По сравнению с другими металлорежущими станками металлообраба-тывающий ГПМ работает в "безлюдном" режиме. Понятие "безлюдного" режима не означает, что человек не участвует в использовании оборудования, однако предполагает возможность достаточно длительного функционирования оборудования в автоматическом режиме.
Для организации ГПМ станок с ЧПУ нуждается в дополнительном оснащении. Основными требованиями ко всему оборудованию входящему в состав ГПМ являются высокая надежность и способность автоматизации всех основных, вспомогательных и рабочих движений. ГПМ как правило имеет в своем составе транспортно-накопительную систему, контрольно-измерительную и диагностическую системы а так же систему удаления отходов.
Дополнительное оборудование для организации ГПМ, как правило, дорогостоящее. Поэтому необходимо учитывать экономическую целесообразность автоматизации. Для окупаемости затрат на организацию ГПМ необходима его максимальная загрузка с наибольшей производительностью.
Взяв некоторые действительные исходные данные с реального производства можно попробовать оценить целесообразность внедрения ГПМ на предприятии. Для оценки эффекта от внедрения ГПМ был рассмотрен участок фрезерных станков c ЧПУ оборудованный двумя 5-координатными станками HERMLE C40U (рисунок 1).
Рисунок 1. Существующая компоновка участка
Работа на участке организованна в 2 смены без выходных ( 332 рабочих дня). По количеству и размеру партий деталей тип производства мелкосерийный. На участке обрабатываются детали 31 наименования с габаритными размерами от 40 до 495 мм из алюминиевых и стальных сплавов, изготовляемые в условиях мелкосерийного производства месячными партиями 5 – 124 шт. Средний годовой объем выпуска деталей 3931 шт. Заготовки получены методом литья, штамповкой, из поковок и из плит.
Следуя методике для расчетов ГПМ Б.Н. Хватова [3] была получена следующая проектная компоновка ГПМ (рисунок 2).
Станки расположены в линию и сгруппированы по технологическому принципу. Автоматизированная транспортно-складская система (АТСС) представлена стеллажом-накопителем и роботом штабелером. Стеллаж вместимостью 57 ячеек однорядный трехъярусный вытянут вдоль всей линии станков. По другую сторону стеллажа располагаются две позиции выполняющие совмещенные функции загрузки и разгрузки спутников а так же две позиции контроля.
Рисунок 2. Проектная компановка ГПМ
Для автоматизированного контроля решено применить устройство Equator фирмы Renishow которая представляет из себя КИМ для автоматизированных измерений и расположено между станками.
Со стороны станков расположен робот-штабелер который забирает спутники со стеллажа и устанавливает их на станки, забирает спутники со станков и устанавливает на позицию автоматизированного контроля, снимает спутник с позиции автоматизированного контроля и возвращает спутник на стеллаж или на станок для дальнейшей обработки с коррекцией, а так же штабелер служит для подачи спутников на позицию разгрузки и из позиции загрузки передает спутники на стеллаж.
Автоматизированная система инструментального обеспечения (АСИО) представлена складом инструментальных наладок на 158 мест и роботом-манипулятором. Робот манипулятор снимает инструмент со станка и помещает его в склад, а из склада догружает необходимый инструмент в магазин станка. За складом организовано рабочее место для сборки и настройки инструмента где производится замена изношенного инструмента, его балансировка, настройка по вылету из патрона, настройка расточных систем на необходимый размер. Инструмент на склад загружается вручную слесарем-инструментальщиком по настройке режущего инструмента, хотя так же возможна автоматизация этого процесса. Для установки спутников на станки и позицию автоматизированного контроля применяются базирующие станции фирмы SHUNK. В спутниках вмонтированы ответные базирующим станциям пальцы, которые служат для закрепления спутника в станции и от которых идет привязка детали для обработки и измерений. Применяемая станочная оснастка осталась без изменения. Конструкция оснастки позволяет ей легко устанавливаться на спутник без доработок. Станки дополнительно оборудованы устройством для автоматического открытия дверей, необходимым для загрузки и разгрузки спутника на станок. Так же предусмотрен автоматический подвод сжатого воздуха к базирующей станции на столе станка необходимый для снятия спутника. Кроме этого станки оборудованы считывающими устройствами. Считывая информацию со спутника, например от штрих-кода, станок получает информацию какая деталь поступила на обработку и какое положение имеет ноль детали относительно базирующих пальцев. Работа слесаря-инструментальщика организована только в первую смену. Так же в первую смену организованна работа слесарей-наладчиков и контролеров. Задача слесарей-наладчиков снимать со спутников готовые детали и устанавливать оснастку и заготовки для последующей обработки. Контролеры занимаются контролем качества готовых деталей. В последующие вторую и третью смену ГПМ работает в автоматическом режиме.
ГПМ позволяет очень быстро переналаживаться с производства одной детали на другую. Это достигается буквально добавлением в инструмента-льный магазин инструмента, если это необходимо, и сменой спутника, на котором уже установлена необходимая оснастка и заготовка. Подобное свойство ГПМ позволяет перейти от традиционной схемы обработки деталей партиями к обработке деталей поштучно в количестве необходимом для дальнейшего производства. Загрузку ГПМ необходимо производить таким образом, что бы при имеющимся запасе спутников с стеллаже-накопителе и имеющимся инструменте на складе АСИО обеспечивалась загрузка обору-дования минимум на две смены непрерывной работы. Система управления (рисунок 3) будет иметь следующий вид: все компоненты ГПМ управляются от центральной ЭВМ через общую шину. Это облегчает взаимодействие компонентов ГПМ и встраивание при необходимости ГПМ в гибкую производственную систему (ГПС). В системе предусмотрен буфер обмена необходимый для передачи поочередных команд для взаимодействия компонентов системы через общий кабель. Это позволит уменьшить количество применяемых кабелей, повысит надежность системы и облегчит диагностику. В соответствии с международной классификацией все СЧПУ по уровню технических возможностей делятся на классы. Центральная ЭВМ имеет класс DNC (Direct Numerical Control) -системы прямого числового управления группами станков от одной ЭВМ. Cтанки, КИМ Equator и робот-манипулятор АСИО имеют класс CNC (Computer Numerical Control)-системы ЧПУ со встроенной мини-ЭВМ (компьютером, микропроцессором). Робот-штабелер имеет класс NC (Numerical Control) — системы ЧПУ с покадровым чтением управляющей программы на протяжении цикла работы.
Рисунок 3. Система управления ГПМ
ГПМ позволяет значительно сократить вспомогательное и подготови-тельно-заключительное время, так как все вспомогательные операции происходят параллельно с работой станков, в это время станки не простаивают. Вспомогательное время в ГПМ равняется времени замены роботом-штабелером спутника с заготовкой, в среднем 4 минутам. Зная первоначальное вспомо-гательное время на изготовление каждой детали и количество деталей можно определить экономию времени которая происходит на ГПМ. Так же ГПМ предполагает работу в 3 смены, что увеличивает производительное время работы оборудования. Количество приобретенного производительного времени от ГПМ в сравнение с существующей организацией участка представлены в таблице 1. ГПМ позволяет ввести третью смену. Работа слесарей-наладчиков, операторов, слесаря инструментальщика необходима только в первую смену. Работа во вторую и третью смену происходит в автоматическом режиме. Третья смена позволяет увеличить годовой фонд производительного времени на 5308 часов, что дает возможность для дальнейшей загрузки оборудования новыми деталями. Сокращения подготовительно-заключительного и вспомогательного времени позволяет дополнительно высвободить 441,1 час станочного времени. В общей сложности ГПМ позволяет увеличить загрузку оборудования дополнительно на 5749 часов в год при этом сократить работу персонала во 2-3 смены.
Таблица 1.
Результаты сравнений
|
|
|
|
Годовой фонд времени работы станков ч. |
Участок станков с ЧПУ |
6065,2 |
631,2 |
72 |
10628 |
ГПМ |
6065,2 |
262,1 |
___ |
15936 |
Приобретаемое производительное время |
______ |
369,1 |
72 |
5308 |
В итоге проектируемый ГПМ по сравнению с существующей организацией работы дает значительную прибавку производительного времени. Эту прибавку можно использовать для увеличения количества выпускаемых деталей или освоения производства других номенклатур деталей. Время на изготовление деталей сокращается за счет параллельного выполнения основных и вспомогательных операций. В ГПМ появляется возможность выпуска деталей не партиями, а поштучно и без потери времени на переналадку. Появилась возможность организации работы в 3 смены, при этом работа ГПМ во вторую и третью смену происходит в автоматическом режиме без участия персонала. Так же организация ГПМ позволяет улучшить условия труда, уменьшить долю человеческого труда в производстве, и соответственно снизить процент брака по вине человека Автоматизированный контроль ГПМ так же позволяет выявить и избежать брак например от износа или поломки инструмента, повысить качество выпускаемых деталей.
