Исследование растворимости нанопорошковой лигатуры Cu-SiC на получение композиционного алюминиевого сплава
Секция: Технические науки
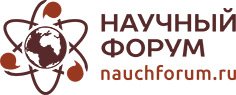
XXXIX Студенческая международная заочная научно-практическая конференция «Молодежный научный форум: технические и математические науки»
Исследование растворимости нанопорошковой лигатуры Cu-SiC на получение композиционного алюминиевого сплава
В связи с быстрым ростом производственного сектора в развитых странах в последние десятилетия, все чаще возникают вопросы, касающиеся проблем трения и изнашивания, вредные последствия которых порой доставляют огромные убытки. Актуальность работы обусловлена растущей потребностью в материалах на основе алюминия – объясняется это в первую очередь его низкой плотностью (2,7 г/см3, против 7,8 г/см3 для железа и 8,94 г/см3 для меди) и высокими механическими характеристиками.
Целью исследования является определение растворимости нанопорошковой лигатуры Cu-SiC в зависимости от режима плавки.
Лучшим методом изготовления композиционных материалов системы Al-SiC являются жидкофазные. Поэтому для исследования влияния состава псевдолигатур на процесс получения алюминиевых композиционных сплавов были проведены экспериментальные плавки. Плавление проводилось в плавильной печи GRAFICARBO с цифровым терморегулятором с максимальной температурой 1200°С и максимальной загрузкой тигля 2000 гр. В алюминиевый сплав А7 вводились лигатуры в виде брикетов, полученных путем прессования с различными удельными давлениями. Плавки проводились по двум режимам: режим №1 – при 950°С при выдержке 35 минут (образцы № 1, 2) и режим №2 – при 750°С с выдержкой 2 часа (образцы № 3, 4). Состав лигатуры, усилие прессования, температура ввода и время выдержки представлены в таблице 1.
Таблица 1.
Состав лигатуры, давление прессования, температура плавления
№ образца |
Основа сплава/ вес, гр. |
Состав лигатуры/ вес, гр. |
Давление прессования, тонн сил |
Температура ввода лигатуры, ºС |
Время выдержки, мин |
1 |
А7/200 гр. |
Cu-2,5%SiC/ 5 |
35 |
950 |
35 |
2 |
А7/200 гр. |
Cu-2,5%SiC/ 5 |
25 |
950 |
35 |
3 |
А7/100 гр. |
Cu-2,5%SiC/ 5 |
35 |
750 |
120 |
4 |
А7/100 гр. |
Cu-2,5%SiC/ 5 |
25 |
750 |
120 |
Режим №1
Исследование микроструктуры полученных при литье слитков проводилось при увеличении *100 на металлографическом микроскопе. Структуры слитков представлены на рисунке 1.
Рисунок 1. Микроструктура образцов, полученных при литье режимом 1. а – структура сплава А7; б – структура образца 1; в – структура образца 2
Был исследован химический состав полученных образцов. Содержание основных элементов в образцах №1, №2, сплавленных при температуре 950ºС с выдержкой 35 минут примерно одинаковый и представлен в таблице 2.
Таблица 2.
Химический состав, полученных при плавке образцов по 1-му режиму
№ образца |
Алюминий,% |
Медь,% |
Углерод,% |
Кислород,% |
1 |
85,71 |
2,2 |
5,11 |
6,48 |
2 |
88,36 |
2,22 |
4,49 |
4,44 |
Микроструктура образцов 1 и состава Al+ Cu-2,5%SiC при увеличении 500 представлена на рисунке 2.
Рисунок 2. Микроструктура образцов 1, 2. а – образец №1; б – образец №2
По результатам микроисследования полученных слитков оказалось, что кремний в структуре не выявляется. Медь, которая является носителем для SiC, не растворяется, а выделяется по границам зерен алюминия. Из карт распределения основных элементов всех образцов 1, 2 видно, что распределение алюминия и углерода равномерное по всему объему, а медь располагается по границам зерен. Карты распределения элементов (Al, Cu, C) образца № 1 представлены на рисунке 3, образца №2 на рисунке.4.
Рисунок 3. Карта распределения основных элементов образца №1
Рисунок 4. Карта распределения основных элементов образца №2
Режим №2
Микроструктура слитков, полученных литьем при температуре 750°С выдержкой 2 часа, исследовалась при увеличении *500 на металлографическом микроскопе. Структуры полученных слитков представлены на рисунке 5.
Рисунок 5. Микроструктура образцов 3,4. Увеличение *500
Из фотографий микроструктур видно, что при данном режиме по сравнению с 1-м режимом плавки растворение брикета прошло лучше, что подтверждает и химический состав образцов № 3 и 4, представленный в таблице 3.
Таблица3.
Химический состав полученных при плавке образцов по 2-му режиму
№ образца |
Al,% |
Cu,% |
O,% |
Ag,% |
C,% |
Si, % |
3 |
89.72 |
3.64 |
1.67 |
0.54 |
4.29 |
- |
4 |
88.77 |
1.61 |
2.80 |
2.19 |
3.62 |
0.39 |
Из химического состава видно, что медь растворилась в большей степени (примерно 1,6%), чем по первому режиму плавки (примерно 2,2%). Так же проявилось небольшое количество кремния, при 1-м режиме плавки кремний вообще не обнаружился.
Как видно из рисунка микроструктуры образцов № 3 и 4, медь также распределена по границам зерен, как и на образцах, сплавленных по 1-му режиму плавки.
При этом карты распределения основных элементов показывают, что распределение алюминия и углерода равномерное по всему объему, а медь располагается по границам зерен. Карты распределения элементов образца № 3 представлены на рисунке 6, образца №4 – на рисунке 7.
Рисунок 6. Карта распределения основных элементов образца №3
Рисунок 7. Карта распределения основных элементов образца №4
Исследование твердости слитков
Исследование твердости проводилось по торцевой поверхности образцов с шагом 5 мм на приборе Роквелла по шкале В с нагрузкой 100 кг стальным шариком. Результаты замеров твердости приведены в таблице 5.
Таблица 5.
Результаты замеров твердости
№ образца |
№ замера |
||||||||
1 |
2 |
3 |
4 |
5 |
6 |
7 |
8 |
9 |
|
Плавка при 950ºС с выдержкой 30 минут |
|||||||||
1 |
17 |
24 |
27 |
31 |
48 |
45 |
33 |
30 |
33 |
2 |
18 |
23 |
28 |
36 |
28 |
22 |
27 |
32 |
30 |
Плавка при 750ºС с выдержкой 120 минут |
|||||||||
3 |
25 |
32 |
40 |
47 |
56 |
49 |
54 |
39 |
27 |
4 |
10 |
16 |
16 |
14 |
15 |
14 |
14 |
11 |
12 |
Из таблицы 5 видно, что твердость образцов №1, 2 выплавленных по первому режиму плавки примерно одинаковая HRB 25-32. Твердость образцов №3 и 4 тоже соответствует этим значениям твердости.
Изломы всех образцов имеют хрупкий характер. Хрупкий излом имеет кристаллическое строение, происходит практически без предварительной пластической деформации, в нем можно различить форму и размер зерен металла. Хрупкий излом характерен для достаточно твердых материалов, что соответствует замеренным значениям твердости. Высокие значения твердости в отдельных точках, свидетельствуют о наличии не растворившихся частиц лигатуры.
Выводы и заключение
Целью исследования являлось изучение растворимости нанопорошковой лигатуры Cu-SiC на получение композиционного алюминиевого сплава. Исследование заключалось в плавке алюминиевого сплава по различным режимам, микроисследование полученных отливок, определение химического состава и твердости. По проделанной работе можно сделать следующие выводы:
1. Распределение основных элементов сплава равномерное по всему объему слитка.
2. Медь, которая входила в состав лигатуры и является носителем для SiC, не растворяется, а выделяется по границам зерен алюминия.
3. Кремний при микроисследовании не выявляется.
4. Замеры твердости образцов, свидетельствуют об упрочнении сплава.
В дальнейшем планируется продолжать исследование полученных образцов. Отработать режимы плавления и методы ввода лигатур.
