Метод проектирования бурового инструмента с использованием пространственной матрицы координат расположения резцов
Секция: Технические науки
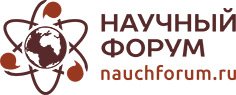
XXXVIII Студенческая международная заочная научно-практическая конференция «Молодежный научный форум: технические и математические науки»
Метод проектирования бурового инструмента с использованием пространственной матрицы координат расположения резцов
Основными недостатками существующих методов проектирования бурового инструмента является использование дополнительных графических материалов для определения натуральных положений, взаимного расположения резцов, сложность определения взаимного расположения резов с внешними поверхностями и с соседними лопастями, В целом очень высокая трудоемкость.
Стендовые сравнительные исследования силовых параметров резания одиночными поворотными и плоскими резцами показали, что области применения данных видов инструментов различны (Рис. 1). В частности, при увеличении прочности разрушаемой породы энергоемкость плоскими резцами значительно больше, по сравнению с энергоемкостью при разрушении поворотными резцами.
Из графических зависимостей видно, что энергоемкость и эффективность поворотных резцов выше при величине стружки менее 8-10 мм на единичный резец. Подача уменьшается при увеличении прочности разрабатываемой породы.
Лабораторные исследования показали, что в предлагаемой конструкции результирующая нагрузка прилагается под углом 45 градусов и режущий элемент работает на сжатие. В связи с чем, конструкцию пластины можно выполнить с упором в хвостовой части.
Рисунок 1. Стендовые исследования силовых параметров резания одиночными поворотными и плоскими резцами
Крепление осуществляется фиксированием фасонной части корпуса режущего элемента затвердевшим полимерным материалом, что позволяет менять резцы, сохраняя долото. Рабочая часть корпуса резца выполняется с уплотнительной юбкой, и армируется твердосплавным наконечником, который самозатачивается при вращении от нагрузки, в результате инструмент сохраняет первоначальный угол резания при движении по траектории забоя.
Рисунок 2. Конструкция поворотных резцов: 1 – Хвостовик резца, 2 – Головка резца, 3 – Твердосплавный наконечник, 4 – Полимерный материал, 5 – Отверстие для заливки
Обследования буровых установок в условиях эксплуатации на нефтегазовых месторождениях при нефтедобыче показали, что подача при использовании бурового инструмента с плоскими элементами составляет не более 1 мм. В тоже время энергоемкость применения плоских резцов при малых подачах значительно уступает поворотным резцам (Рис.1).
С появлением современны программ трехмерного моделирования на основе систем AutoCAD, компас-3D и Solidwork появилась возможность визуализации процесса проектирования.
При проектировании появилась возможность контроля взаимного положения инструмента, коррекции углов резания с учетом рациональных геометрических параметров резания.
Для точного моделирования взаимного расположения резцов на лопастях можно использовать матрицу установки режущего инструмента.
Первоначально необходимо знать схему расстановки и количество резцов на каждой лопасти долота.
Во-первых, для этого разрабатывается схема расстановки резцов на буровом инструменте.
Рисунок 3. Схема установки количество резцов бурового инструмента
Чертим схему и наносим цвета для того, чтобы согласно цветовой гамме было установлено положение резца. Для каждого резца на лопасти будет своя цветовая гамма расположения.
Во-вторых, выбирается форма забоя. Существуют вогнуто-конусная, плоская, выпукло-конусная, но в данном случае выбираем комбинированную форму забоя.
Таким образом, обеспечивается в средней части формирования конуса целика и по краям плавный переход к стенке скважины.
Рисунок 4. Комбинированная форма забоя: а – вогнуто-конусная форма; б – плоская форма; с – выпукло-конусная форма
Определив геометрические параметры движения резцов можно построить матрицу для индивидуального монтажа каждого резца на лопасти.
Матрица состоит из схемы расстановки и формы забоя.
Рисунок 5. Матрица установки резцов в забое
В результате строим форму забоя с индивидуальным расположением линий резания для резца.
Для простоты монтажа удаляем лишнюю часть матрицы с обратной стороны, в результате получаем элемент матрицы с координатами положения резцов.
Для установки резцов создаем лопасть и строим плоскость 1 перпендикулярной оси вращения и проходящей через линию установки резцов на выбранной лопасти. Дополнительно строим плоскость 2 проходящую через вершину резца, которая совпадает с линией резания и расположена перпендикулярно осевой линии.
Рисунок 6. Элемент матрицы
Во вспомогательной плоскости 2 строим эскиз, где отображается ось положения резца, и формируем корпус твердого тела на лопасти, обеспечивающий установку держателя резца.
Получив твердое тело, в этой же плоскости строим новый эскиз по чертежу режущего инструмента с возможностью посадки в отверстие по эскизу делается круговой вырез.
На этом операция установки первого резца закончена, следующий резец выполняется аналогично предыдущему, но при этом точка установки резца определяется согласно схеме установки резца (рис. 3).
Получив твердое тело, в этой же плоскости строим новый эскиз по чертежу режущего инструмента с возможностью посадки в отверстие по эскизу делается круговой вырез.
Рисунок 7. Эскиз корпуса твердого тела
На этом операция установки первого резца закончена, следующий резец выполняется аналогично предыдущему, но при этом точка установки резца определяется согласно схеме установки резца (рис. 3).
Рисунок 8. Посадочное место для режущего инструмента
Рисунок 9. Лопастной буровой инструмент с поворотными резцами
Во время моделирования необходимо выбрать минимальное расстояние между сопряжениями державки с целью оптимального взаимного расположения.
Последовательное построение резцов обеспечит оптимальное расположение друг относительно друга и формирование лопасти бура.
Лопасти проецируются отдельно друг от друга по индивидуальной схеме расстановки, и для окончательного монтажа применяется вспомогательные базовые плоскости, и корпусные элементы опорной части бурового инструмента.
В результате использования матрицы проектирования позволяет разработать буровой головки с точным расположением режущего инструмента с правильными геометрическими параметрами резания.
Использование матрицы позволяет корректировать установку режущего инструмента в процессе формирования геометрии лопасти.
Данная технология предназначена для изготовления буровой головки на станках с ЧПУ.
Используя матрицы режущего инструмента, в будущем позволит разработать алгоритм проектирования буровой головки в автоматизированном виде.
