Критерии и условия, повышающие надежность функционирования нефтетранспортного оборудования
Журнал: Научный журнал «Студенческий форум» выпуск №21(157)
Рубрика: Технические науки
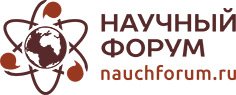
Научный журнал «Студенческий форум» выпуск №21(157)
Критерии и условия, повышающие надежность функционирования нефтетранспортного оборудования
Надежность – свойство объекта выполнять заданные функции в заданном объеме при определенных условиях функционирования. Применительно к системам нефтеснабжения в числе заданных функция предусматривают бесперебойное снабжение потребителей нефтью и нефтепродуктами требуемого качества и недопущение ситуаций, опасных для людей и окружающей среды. Надежность – комплексное свойство, которое в отдельности или определённом сочетании включает безотказность, долговечность, ремонтопригодность, устойчивоспособность, режимную управляемость, живучесть и безопасность. Так как в дальнейшем перечисленные понятия будут часто встречаться при рассмотрении проблем надежности магистральных трубопроводов, необходимо привести их определения[1].
Безотказность – свойство магистрального трубопровода непрерывно сохранять работоспособность в течение некоторого времени.
Долговечность – свойство магистрали сохранять работоспособность до наступления предельного состояния при установленной системе технического обслуживания и ремонтов.
Ремонтопригодность – способность трубопровода, заключающаяся в приспособленности к предупреждению и обнаружению причин возникновения его отказов, повреждений и устранению их последствий путем проведения технического обслуживания и ремонтов.
Устойчивость – способность объектов непрерывно сохранять устойчивость в течение некоторого времени.
Режимная управляемость – свойство трубопровода поддерживать нормальный режим посредством управления.
Живучесть – свойство магистрального трубопровода противостоять возмущениям, не допуская их каскадного развития с массовым нарушением поставки топлива, сырья потребителям.
Безопасность – возможности объекта не допускать ситуаций, опасных для людей и окружающей среды.
Анализ работоспособности, безотказности и ремонтопригодности линейной части трубопроводов, технологического оборудования составляет информационную базу анализа надежности магистральных трубопроводов как сложных технических систем. Однако такой анализ не решает проблемы оценки надежности трубопровода как сооружения. В данной случае надежность – собирательное понятие для обозначения совокупности свойств определяющих качество функционирования объекта.
Основной показатель надежности трубопровода – пропускная способность – интегральная характеристика производственной мощности нефтетранспортной системы. Данный показатель характеризует состояние трубопровода в данный момент времени независимо от состояния других элементов систем. Обычно, проектную пропускную способность считают постоянной, т.е. это пропускная способность идеального абсолютно надежного трубопровода, работающего в неизменяющихся условиях. Расчет фактической надежности магистрального трубопровода состоит в исследовании изменения реальной пропускной способности в зависимости от частоты, характера и продолжительности отказов линейной части, насосных и компрессорных станций.
Следующий показатель надежности трубопровода – это качество и надежность сварных соединений. Большая часть соединений труб, трубных деталей, запорной и регулирующей арматуры на магистральных трубопроводах являются сварными. В технологии прокладки трубопроводов качество выполнения сварочно-монтажных работ в значительной степени определяет надежность их эксплуатации и безопасность работы. Требования к качеству сварки сводятся к обеспечению условий равнопрочности и вязкости сварных соединений основному металлу труб, трубных деталей и арматуры.
Качество сварки, надежность сварных соединений определяются многими составляющими и в том числе показателями свариваемости сталей, способом и технологическими параметрами сварки, правильным выбором и качеством сварочных материалов, квалификацией сварщиков и контролеров качества, а также применяемым методом контроля и чувствительностью аппаратуры. По результатам контроля обнаруженные дефекты в сварных соединениях могут быть устранены, стыки отремонтированы или вырезаны и заменены катушкой[3].
Защита от коррозии магистральных трубопроводов непрерывно совершенствуется. В настоящее время для защиты нефтепроводов от внутренней коррозии применяют ингибиторы коррозии и покрытия из коррозионностойких материалов. Технология применения ингибиторов коррозии несовершенна, поскольку нет однозначных ответов на вопросы: когда необходимо начинать защиту, в какие точки, сколько и какого ингибитора подавать в поток. Нанесение защитных покрытий на внутреннюю поверхность трубопроводов не нашло широкого применения, т.к. возникают проблемы в зоне сварного стыка[2].
Вместе с тем известно, что сами по себе нефть и нефтяной газ не вызывают коррозии. В большинстве случаев внутренняя коррозия нефтепроводов является следствием электрохимических процессов, протекающих при контакте пластовой воды с металлом.
Расслоение водонефтяной эмульсии и образование слоя воды, контактирующего со стенкой трубопровода, создают условия для возникновения коррозии вдоль нижней образующей в виде язв и канавок.
Эффективным способом защиты нефтепроводов от внутренней коррозии является технологический. Сущность этого способа защиты состоит в поддержании таких режимов течения обводненной нефти, при которых исключается контакт пластовой воды со стенками трубопровода[4].
Таким образом, при проектировании особое внимание необходимо уделять таким параметрам, как: расчет пропускной способности, качество сварных соединений, расчет оценки коррозионной опасности. Именно они значительно влияют на надежность трубопроводных систем.
