Моделирование волочения биметаллических труб
Журнал: Научный журнал «Студенческий форум» выпуск №12(33)
Рубрика: Технические науки
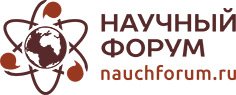
Научный журнал «Студенческий форум» выпуск №12(33)
Моделирование волочения биметаллических труб
Аннотация. Приведены результаты моделирования энергосиловых условий при сборке волочением биметаллической трубы (внешний слой - медь М1, внутренний слой - алюминиевый сплав АД33Т) методом конечных элементов в программном комплексе DEFORM-2D. Показано влияние угла конусности рабочего канала волоки на формирование остаточных контактных напряжений в готовой трубе, определяющих прочность сцепления слоев после волочения.
Ключевые слова: Волочение; сборка; биметаллическая труба; моделирование; силовые условия; остаточные сборочные напряжения; программа DEFORM-2D.
В биметаллическом полуфабрикате сочетаются эксплуатационные свойства, которые нельзя получить в одном отдельно взятом металле или сплаве [1]. Например, можно сочетать высокую прочность металла оболочки с коррозионной стойкостью внутренних элементов конструкции составных труб [2].
Применение сборных биметаллических полуфабрикатов сложных поперечных сечений с большим количеством ребер увеличивает мощность и производительность теплообменных и холодильных установок, прочность и жесткость конструкций, уменьшает металлоемкость машин и объем механической обработки, обеспечивает экономию электроэнергии, материалов и снижение стоимости продукции на единицу конечного полезного эффекта [7].
Перспективным процессом получения биметаллических труб сложных поперечных сечений является сборка совместным волочением вставленных одна в другую монометаллических и биметаллических длинномерных заготовок. Однако его широкое внедрение сдерживается отсутствием научно обоснованной технологии их производства [3,4]. Технология производства составных многослойных труб зависит от ряда факторов: соотношение прочностных свойств и толщин слоев, конфигурации и размеров, а также требований по прочности сцепления сочленяемых слоев, качеству поверхности. Сборку составных труб необходимо производить так, чтобы в зоне контакта слоев в готовой биметаллической трубе возникали остаточные контактные напряжения радиальные напряжения за счет различной упругой отдачи металлов [5].
Данный процесс, на сегодняшний день, является не достаточно изученным.
В настоящее время для исследования процесса волочения наиболее широко используется компьютерное моделирование [6-10].
Цель работы – исследование процесса сборки волочением биметаллических полуфабрикатов, обеспечивающего получения прочного сцепления сочленяемых слоев из разнородных материалов.
Проведено компьютерное моделирование сборки волочением биметаллической трубы с помощью метода конечных элементов в специализированном программном комплексе DEFORM-2D [11]. При моделировании в качестве заготовок использовали трубу из меди М1 для внешнего слоя и трубу из сплава АД33Т для внутреннего, вставленные одна в другую с зазором 0,5 мм. Предел текучести данных материалов составляет: М1 - 80 МПа; АД33Т - 120 МПа, а предел прочности: для М1 - 250 МПа; АД33Т - 180 МПа. До волочения заготовки имели следующие размеры: внешняя труба - внутренняя -
х1 мм; зазор между заготовками составлял 0,5 мм. После сборки труба имела размеры
Трубу протягивали через коническую волоку с диаметром 10 мм, углом конуса рабочей зоны 2α = 12°; 18° ; 24°; 30° и длиной калибрующего пояска 5 мм ,рисунок 1а. Радиус сопряжения рабочей и калибрующей зон 10 мм. Чертеж заготовки в сборе представлен на рисунке 1б. Коэффициент вытяжки l=1,2. Трехмерные геометрические модели волоки 1, внутреннего слоя 2 и внешнего слоя 3, полученные с помощью программного комплекса DEFORM, приведены на рисунке 2.
Рисунок 1. Чертеж волоки и заготовки
1 – волока; 2 – внутренний слой; 3 –внешний слой
Рисунок 2. Компьютерная модель волочения биметаллической трубы
На поверхностях контакта заготовки и волоки действуют касательные напряжения, определяемые по закону Кулона. Коэффициент трения принят равным 0,12. Конечно - элементная сетка трубы сгенерирована с использованием 1000 элементов с длиной ребра элемента 0,333 мм.
На рисунке 3 изображен график изменения усилия волочения от времени расчета . Из графика видно, Кривые состоят из трех участков. Первый участок определяется ростом усилия волочения при входе составной заготовки в канал волоки. На втором участке усилие практически не меняется, что говорит об установившемся процессе. На третьем участке усилие резко убывает при выходе сборной трубы из канала волоки.
В качестве основного требования к аналитическим зависимостям для расчета технологических параметров процесса волочения отмечено, что они должны показывать наличие зоны оптимальных углов канала волоки. Предлагаемая модель удовлетворяет этому требованию. Оптимальным углом конусности рабочей зоны волоки - 24°.
Рисунок 3. График изменения усилия волочения от времени расчета
На рисунках 4 - 7 представлены графики распределения остаточных радиальных напряжений после снятия нагрузки. Из рисунков следует, что после волочения, на границе сопряжения внутреннего и внешнего слоев создаются радиальные контактные напряжения, отвечающие за прочное сочленение слоев. Замер производился от места сопряжения к внутреннему или внешнему диаметру трубы.
Рисунок 4. Распределение радиальных напряжений по внешнему (а) и внутреннему (б) элементам составной трубы при угле конусности волоки 12°
Рисунок 5 Распределение радиальных напряжений по внешнему (а) и внутреннему (б) элементам составной трубы при угле конусности волоки 18°
Рисунок 6. Распределение радиальных напряжений по внешнему (а) и внутреннему (б) элементам составной трубы при угле конусности волоки 24°
Рисунок 7. Распределение радиальных напряжений по внешнему (а) и внутреннему (б) элементам составной трубы при угле конусности волоки 30°
На рисунке 8 получен график зависимости контактного давления от угла конуса волоки и сравнение с расчетными данными, полученными по формуле 1:
(1)
Рисунок 8. График зависимости контактного давления от угла конуса волоки и коэффициента вытяжки
По полученным данным мы можем судить о том, что наибольшее контактное напряжение возникает при угле конуса волоки равном 24°. Сравнение данных полученных моделированием и расчетных данных говорит о сходимости в пределах 22 – 50%.
ВЫВОД
С помощью моделирования можно проанализировать процесс сборки волочением биметаллической трубы. Полученные данные позволяют подобрать технологические параметры, отвечающие за прочность сцепления слоев биметаллической трубы. Это позволит эффективно управлять процессом на стадии проектирования, уменьшит финансовые затраты и снизит трудоемкость.
