СОВРЕМЕННЫЕ ТЕХНОЛОГИИ ИЗГОТОВЛЕНИЯ ДЕТАЛЕЙ ИЗ ПОЛИМЕРНЫХ КОМПОЗИЦИОННЫХ МАТЕРИАЛОВ
Секция: Технические науки
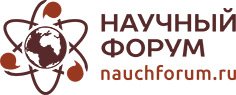
LI Студенческая международная научно-практическая конференция «Технические и математические науки. Студенческий научный форум»
СОВРЕМЕННЫЕ ТЕХНОЛОГИИ ИЗГОТОВЛЕНИЯ ДЕТАЛЕЙ ИЗ ПОЛИМЕРНЫХ КОМПОЗИЦИОННЫХ МАТЕРИАЛОВ
Конструкционные материалы во многом определяют высокий уровень современной авиакосмической техники, что связано с их высокой надежностью, весовой эффективностью, хорошими технологическими и эксплуатационными свойствами. Разработка новых технологий, которые исключают необходимость использования автоклавного оборудования и изготовления препрега, являются очень актуальными. Главным недостатком ПКМ является их высокая стоимость, которая во многом определяется длительностью процесса их формования, ограниченной жизнеспособностью получаемых препрегов и высокой стоимостью технологического оборудования.
В настоящее время известно множество технологических процессов формования, применяемых в производстве изделий из композиционных материалов. В данной статье рассмотрены три технологии, по мнению авторов, являющиеся наиболее перспективными для деталей авиационной техники.
Основное развитие автоклавная технология получила благодаря использованию конструкций из углепластика в аэрокосмическом секторе и авиастроении, за счет низкого веса и высоких физико-механических свойств конечных изделий. Предварительно раскроенный препрег или многослойный пакет из препрега на основе углеродных волокон укладывают в форму. К форме при помощи термостойкого герметизирующего жгута крепят вакуумный мешок. Использование вакуумного насоса позволяет свести пористость ламината к минимуму, что гарантирует высокое качество конечного изделия. Использование автоклавной технологии позволяет производить крупногабаритные изделия, к которым применяются самые высокие требования по качеству [1]. За счет использования вакуумного насоса в вакуумном мешке создается разрежение и удаление воздушных включений из ламината. Далее, изделие на специальной тележке, перемещающейся по рельсам, загружается в автоклав (рис. 1). Не отключая вакуум, в автоклаве создают избыточное давление и нагрев до температуры отверждения препрега.
Можно отметить следующие характерные особенности метода автоклавного формования:
- возможность получения изделий равномерной толщины;
- возможность формования крупногабаритных изделий;
- высокое качество поверхности изделий;
- при использовании вакуумного мешка получаются высококачественные изделия с низкой пористостью
Рисунок 1. Автоклав для изготовления изделий из ПКМ
Недостатком автоклавного метода является высокая стоимость самого автоклава, а также наличие ручного труда, что требует высокой квалификации персонала. Данный метод малопригоден для крупносерийного производства и находит большее применение в производстве небольших партий высококачественных изделий. Перспектива снижения стоимости процесса (соответственно и изделий) связана с механизацией и автоматизацией ряда операций, сокращением благодаря этому трудовых затрат и подбором лучших материалов для вакуумных мешков.
Альтернативой препрегово-автоклавной технологии изготовления деталей является метод пропитки под давлением и метод автоматизированной выкладки ТПКМ.
Суть способа пропитки под давлением (технология RTM) заключается в следующем: армирующий тканевый наполнитель в необходимом количестве укладывается в форму, которая далее герметизируется, и через дренажную систему под давлением в нее подается связующее (рис. 2). Процесс пропитки идет до тех пор, пока связующее не заполнит все свободное пространство формы. Сигналом для прекращения пропитки является заполнение связующим (без пузырей воздуха) выходных трубок дренажной системы. После пропитки форму помещают в печь или пресс, где происходит отверждение детали. В случае использования в качестве связующего композиций холодного отверждения процесс проходит при нормальной температуре.
К преимуществам такого способа можно отнести отсутствие необходимости в дорогостоящем оборудовании, хорошие условия труда (отсутствует непосредственный контакт человека со связующим), возможность изготовления деталей сложной формы, возможность использования трехосно-армированных наполнителей, относительно невысокая стоимость процесса.
Рассмотренные технологические процессы имеют свои особенности, преимущества и недостатки, но каждый возможно применять в зависимости от конструкции и технических требований изготавливаемой детали, технологических возможностей предприятий.
Рисунок 2. Схема процесса пропитки под давлением (технология RTM)
Наряду с преимуществами, у процесса пропитки под давлением есть недостатки, основными из которых являются длительность процесса и зависимость качества детали от правильности расположения трубок дренажной системы, а также, конструктивная сложность и высокая стоимость оснастки.
Однако, несмотря на это, способ пропитки под давлением широко применяется в авиакосмической технике для изготовления таких деталей, как лопасти винто-вентиляторных двигателей, лопатки турбореактивных двигателей, монолитные обтекатели, элементы механизации крыла, различные детали сложной формы и т.д. [2].
Согласно мировым тенденциям традиционные технологии изготовления деталей из ПКМ, использующие, в том числе, ручные методы формования, все чаще замещаются новыми автоматизированными технологиями, например, такими, как автоматизированная выкладка ленты, автоматизированная выкладка волокна и др.
Высокая потребность в автоматизации обусловлена повышением требований к механическим и точностным характеристикам изделий. Востребованность, в частности, безавтоклавных технологий объясняется меньшей себестоимостью готового изделия и меньшей трудоемкостью, так как автоклавные технологии являются дорогостоящими из-за высокой цены оборудования, а технологическое время (нормочасы) на изготовление детали напрямую зависит от времени отверждения полимера.
Для реализации безавтоклавной технологии – автоматизированной выкладки деталей из ТПКМ — существуют роботизированные комплексы, позволяющие получать прецизионные изделия с высокими механическими характеристиками при минимальном участии в этом процессе человека [3].
Автоматизированная выкладка (Automated Tape Placement) — это процесс выкладки ленты ТПКМ на формообразующую оснастку (преформу), обеспечивающий получение изделий с различной структурой армирования. Физика процесса заключается в подводе тепловой энергии, необходимой для расплавления связующего ленты ТПКМ с её дальнейшим прессованием роликом, что приводит к формообразованию готовой детали (рис. 3).
Рисунок 3. Схема процесса автоматизированной выкладки ТПКМ
Технология автоматизированной выкладки имеет высокий потенциал развития и высокую конкурентоспособность в области технологий по изготовлению прецизионных и высокопрочных деталей из ТПКМ вследствие возможности сократить трудоемкость процесса, повысить степень его автоматизации.
