Конструктивные мероприятия по защите от абразивного износа элементов дымососов
Секция: Технические науки
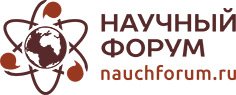
XXXVIII Студенческая международная заочная научно-практическая конференция «Молодежный научный форум: технические и математические науки»
Конструктивные мероприятия по защите от абразивного износа элементов дымососов
В настоящее время тягодутьевые машины эксплуатируются на тепловых электростанциях, в металлургическом производстве, в химической промышленности, в производстве строительных материалов, в установках газоочистки и пылеулавливания на промышленных предприятиях, в различных отраслях промышленности.
Основным видом повреждения рабочих колес и кожухов дымососов является абразивный износ при транспортировке запыленной среды из-за больших скоростей и высокой концентрации золы в дымовых газах. Этот износ имеет газоабразивный характер, который вызывается механическим действием твердых частиц, перемещаемых потоком газа. В этом случае разрушение металла происходит в результате срезания, выкрашивания, выбивания и многократного пластического деформирования его поверхностных микрообъемов. Износ лопаток и дисков роторов дымососов зависит от сорта сжигаемого топлива и качества работы золоулавливающих установок.
КОНСТРУКТИВНЫЕ МЕРОПРИЯТИЯ ПО ЗАЩИТЕ ОТ ИЗНОСА
В результате износа рабочего колеса возникает разбаланс, нарушающий нормальную работу машины. Для его устранения приходится останавливать машину и выполнять балансировку. При неудовлетворительной очистке дымовых газов от золы нередки случаи, когда рабочие колеса приходится менять через 10–20 дней.
Однако на основании опыта эксплуатации дымососов четко выявливается зависимость абразивного износа не от окружной скорости, а от числа оборотов машины. Эту зависимость следует понимать так, что для заданных показателей машины по производительности и давлению при тяжелых условиях работы по износу ее следует выполнять по такой аэродинамической схеме, которая обеспечит необходимые показатели при относительно небольшом числе оборотов. Так, например, применявшиеся ранее дымососы типа Д-190, создававшие давление 400 кгс/м2 при производительности 300 000 м3/ч, по условиям износа оказались непригодными в эксплуатации вследствие высокого числа оборотов (960 в минуту). Окружная скорость рабочего колеса этих дымососов при d=1560 мм составляла всего 78 м/с.
Эти дымососы были заменены машинами типа Д 300/400 с рабочим колесом d=2200 мм которые обеспечивали примерно те же показатели при 730 об/мин, а окружная скорость составляла при этом 85 м/с. Эти дымососы показали удовлетворительную работу в условиях золового износа.
Причина заключается в том, что в машине Д 300/400 вследствие более низкого числа оборотов, рабочее колесо имеет большие размеры (d=2200 мм), поэтому работа трения золовых частиц распределяется на большую площадь элементов рабочего колеса и улитки. Вместе с тем, очевидно, что при одинаковом типе лопаток колеса и прочих равных условиях, т. е. при одинаковом числе оборотов, одинаковой производительности, концентрации и физических свойствах твердых частиц, высоконапорная машина будет изнашиваться интенсивнее, чем низконапорная, и в этом смысле износ будет определяться величиной окружной скорости рабочего колеса.
Износу подвержены детали рабочего колеса и кожуха машины. Абразивные частицы, проходя через рабочее колесо, отклоняются к основному диску. Поэтому износ захватывает меньшую часть входной кромки лопатки и большую часть ее выходной кромки (рис. 1).
Рисунок 1. Износ лопаток и основного диска рабочего колеса
Изнашивается также и основной диск в местах примыкания к нему лопаток.
В кожухе наибольшему износу подвержена улитка и в меньшей степени изнашиваются боковые листы.Карманы дымососов и всасывающие воронки практически не подвержены износу, так как скорости газового потока в них относительно невелики.
Нерациональная компоновка может привести к усиленному износу даже в тех частях машины, которые обычно почти не изнашиваются. В качестве примера на рисунке 2 показана крайне неудачная компоновка дымососа с изломом линии тракта при входе в карман. Вследствие изменения направления газового потока зола отклоняется к стенке кармана, вызывая его износ.
При более правильной компоновке (рис. 3) износ карманов почти отсутствует.
Рисунок 2. Неправильная компоновка дымососа, при которой зола изнашивает всасывающие карманы
Рисунок 3. Правильная компоновка дымососа
В автореферате Путиловой И.В. «Абразивный износ трубопроводов пневмотранспортных установок систем золошлакоудаления и пылеприготовления ТЭС» по результатам исследования приведены оптимальные данные по форме и углам поворота трубопроводов тягодутьевой машины, позволяющие существенно снизить абразивный износ и уменьшить аэродинамические потери [6, с.6].
Для защиты от абразивного износа в конструкции машин обычно предусматривают специальные меры. Иногда для защиты лопаток и основного диска рабочего колеса от износа идут на увеличение их толщины. При этом утяжеляется рабочее колесо, растет нагрузка на вал и опоры и не достигается в достаточной степени преследуемая цель.
Более правильной и распространенной мерой борьбы с износом является защита изнашиваемой поверхности при помощи накладок или наплавки. Защитные накладки не привились в конструкциях рабочих колес и получили преимущественное распространение в улитках в виде броневых листов, выполняемых из стали или чугуна. Выбор конкретного материала для защиты осуществляется на основе его устойчивости к износу по различным признакам. Определить нужный материал можно используя данные из автореферата Беговой А.Н. «Разработка метода определения абразивной износостойкости сталей по механическим признакам» [1, с.14].
В отдельных случаях защита кожуха от абразивного износа выполняется путем бетонирования его внутренней поверхности слоем толщиной 20–30 мм.
Для лопаток широкое применение нашла наплавка рабочих поверхностей твердым сплавом, который накладывается слоем от 2 до 4 мм. Наплавка выполняется при помощи электродов марки Т-590, имеющих следующий состав обмазки: 90% феррохрома, 5% карбида бора, 5% графита серебристого. Обмазка наносится на проволоку марки 08НЗ, которая имеет следующий состав:0,08% С; 0,17–0,35%Si; 0,4–0,65%Мп; <0,025%S; < 0,03%Р; 3–3,6%Ni.Во избежание выгорания легирующих элементов покрытия сварку следует вести при токе 220А электродами d–4 мм и 220–240А электродами d–5 мм. Твердость поверхности, наплавленной электродами Т-590, составляет 52–58Rc [3]. При наплавке значительно повышается срок службы рабочего колеса (по данным в 2–4 раза). Несмотря на трудоемкость выполнения наплавки в условиях эксплуатации, она вполне окупается.
При выборе толщины наплавляемых лопаток, помимо вопросов прочности, следует учитывать также необходимую устойчивость лопаток от коробления при наплавке, что достигается толщиной лопаток в пределах 6–8 мм.
Также был разработан метод полуавтоматической наплавки при помощи плоских электродов. Этот метод в основном применяется в заводских условиях. На рис. 4. Показана лопатка дымососа типа 25х2Ш, которая после наплавки подвергнута горячей штамповке.
Рисунок 4. Лопатка дымососа Д 25 x 2Ш, где 1 – слой твердого сплава Т-620 толщиной 2–3 мм, направленный полуавтоматическим способом на заготовку лопатки
Полуавтоматическая наплавка дает возможность получить равномерный слой твердого слоя на заготовке, который прочно удерживается и позволяет осуществлять последующую горячую штамповку лопаток. Сравнительнос ручным способом полуавтоматическая наплавка дает существенное повышение производительности труда при одновременном улучшении качества, так как наплавленная поверхность получается плотной, и достаточно гладкой, а благодаря значительному выделению тепла уменьшается количество трещин. Кроме того, благодаря сравнительно малой глубине проплавления достигается более сильное легирование наплавленного металла.
Защита дисков в месте примыкания к ним лопаток осуществляется специальными защитными козырьками, которые привариваются к среднему диску и лопаткам, как это показано на рис.5.
Рисунок 5. Защита от износа основного диска рабочего колеса дымососа Д20X2.1 – основной диск; 2 – лопатки; 5 – защитные козырьки
Защитные козырьки применяются как при наплавленных, так и при ненаплавленных лопатках. В первом случае на лопатке оставляется ненаплавленная полоска, необходимая для наложения сварного шва. Накладывать шов по наплавке недопустимо, так как качество его будет чрезвычайно низким вследствие легирования примесями, содержащимися в наплавленном слое [5, c.67].
Защита улитки и боковых листов от износа осуществляется обычно при помощи накладок—броневых листов. Броневые листы выполняются обычно из стали, но для тяжелых условий работы рационально выполнять их литыми из чугуна толщиной около 40 мм.Большей частью защищают только торцовый лист. Наиболее распространенный способ крепления броневых листов - приварка, но при этом затруднена смена изношенных листов. Более правильно выполнять крепление броневых листов при помощи специальных болтов (рис 6).
Рисунок 6. Защита боковых и торцового листа улитки дымососа броней, прикрепленной на болтах
Также для защиты от износа используются композитные и полимерные материалы. Вопросы их использования, а также интенсивность износа при эксплуатации рассматривается в статье Ищенко А.А., Дашко Е.В. «Определение интенсивности абразивного износа защитного полимерного покрытия» [4, с.86].
Таким образом, борьба с абразивным износом тягодутьевых машин является весьма актуальной задачей. Игнорирование вопросов износа может привести к невозможности нормальной работы установки, так как нередки случаи, когда рабочие колеса приходится заменять ежемесячно, а иногда и чаще.
Предохранение машин от износа до некоторойстепени зависит от конструктора, так как припроектировании он должен предусмотреть необходимые меры защиты. Однако наиболее эффективным способом борьбы с износом является рациональная компоновка и особенно тщательная очистка газов от твердых абразивных фракций. На электростанциях, где этот вопрос решен удовлетворительно, рабочие органы дымососов практически не требуют ремонта, так как они почти не изнашиваются [2].
Учитывая перспективы все большего применения в качестве энергетического топлива мазута и газа, а также возрастающие требования к эффективности работы золоулавливающих устройств можно считать оправданным выпуск заводами-изготовителями дымососов с ограниченной защитой от износа, т. е. без наплавки лопаток.
Необходимо предъявлять более жесткие требования к золоулавливающим установкам электростанций с тем, чтобы они обеспечивали эффективную очистку газов. Единовременные затраты на установку эффективно действующих золоуловителей вполне окупятся экономией на ремонте дымососов, не говоря уже о санитарных условиях.В настоящее время ведется тема №16059В «Исследование инновационного газоочистного оборудования», в которой рассматривается как новый тип золоуловителя, так и борьба с возможным абразивным износом элементов проточной части установки. Теоретически, методика борьбы с абразивным износом может быть применена и к золоулавливающей установке, что в ближайшем времени планируется рассчитать на компьютере по соответствующим программам.
