Определение параметров качества поверхностного слоя тонкостенных алюминиевых деталей после обработки точением инструментом с покрытием
Секция: Технические науки
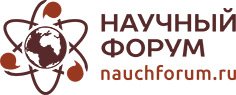
XXX Студенческая международная научно-практическая конференция «Технические и математические науки. Студенческий научный форум»
Определение параметров качества поверхностного слоя тонкостенных алюминиевых деталей после обработки точением инструментом с покрытием
В статье [1 и 2] рассмотрена проблема подбора технологических условий для обработки тонкостенных деталей из алюминиевых сплавов. Показано, что возникающие остаточные напряжения при получении заготовок и их дальнейшей механической обработке приводят к нежелательным и недопустимым изменениям размеров и формы деталей. Поэтому целесообразно использовать оптимальные режимы резания, на которых значение сил резания минимально, а значит и минимальны остаточные напряжения и деформации деталей. Получено уравнение обрабатываемости, позволяющее расчетным путем определять оптимальную скорость резания. Определены поправочные коэффициенты для учета в расчетах оптимальной скорости особенностей современных режущих инструментов с износостойкими покрытиями и сложной передней поверхностью инструмента.
В данной работе выполнено экспериментальное определение параметров качества поверхностного слоя деталей из алюминиевых сплавов после обработки точением на оптимальных режимах и заводских, взятых из действующей технологии производства.
На двух кольцевых заготовках (рисунок 1), обработанных на оптимальной (5,6 м/с) и базовой скорости резания (4,4 м/с) твердосплавным инструментом из сплава IC907 при прочих равных условиях (см. таблицу 1), проводили измерение твердости и шероховатости обработанных поверхностей. Шероховатость поверхностей определяли на приборе TR-200 фирмы TIME GROUP Inc. Твердость поверхности определяли на микротвердомере DuraScan 10 фирмы ЕМКО-TEST при нагрузке на алмазный индентор в форме пирамиды Виккерса 25г. Результаты измерений представлены в таблицах 1 и 2.
Рисунок 1. Обрабатываемая кольцевая заготовка
Таблица 1.
Результаты измерений шероховатости обработанной поверхности
№ измерения |
Результаты измерений шероховатости поверхности заготовки, обработанной на заводских режимах (v = 4,4 м/с) |
Результаты измерений шероховатости поверхности заготовки, обработанной на предлагаемых режимах (vО = 5,6 м/с) |
||
Шероховатость Ra, мкм |
Среднее значение шероховатости Ra, мкм |
Шероховатость Ra, мкм |
Среднее значение шероховатости Ra, мкм |
|
1 |
0,73 |
0,85 |
0,82 |
0,87 |
2 |
0,79 |
0,84 |
||
3 |
0,73 |
1,16 |
||
4 |
0,98 |
0,83 |
||
5 |
1,00 |
0,69 |
Как видно из полученных данных, шероховатость поверхности обработанных образцов практически одинакова, разница средних значений параметра шероховатости поверхности соответствует статистической погрешности метода измерения и прибора.
Таблица 2.
Результаты измерений твердости обработанной поверхности
№ измерения |
Результаты измерений твердости поверхности заготовки, обработанной на заводских режимах (v = 4,4 м/с) |
Результаты измерений твердости поверхности заготовки, обработанной на предлагаемых режимах (vО = 5,6 м/с) |
||
Твердость, НV |
Среднее значение твердости, НV |
Твердость, НV |
Среднее значение твердости, НV |
|
1 |
101 |
107 |
122 |
125 |
2 |
112 |
114 |
||
3 |
108 |
138 |
Как видно из полученных результатов, микротвердость поверхности второго образца, обработанного на оптимальных режимах, выше примерно на 15%, что говорит о влиянии теплового фактора на повышение наклепа.
Расчетное определение остаточных напряжений в поверхностном слое заготовки
Определение тангенциальных остаточных напряжений по величине и глубине залегания выполнялось расчетным методом по программе для ПК, разработанной на кафедре ТАДиОМ РГАТУ имени П. А. Соловьева. Для расчетов использовались формулы, приведенные в работе [3].
Исходные условия расчета и некоторые промежуточные результаты расчета:
Обрабатываемый материал – Д16Т, инструментальный материал – ВК8.
1) Заготовка, обработанная на заводских режимах: подача S = 0,1 мм/об, скорость резания v = 4,4 м/с, глубина резания t = 0,5 мм, температура в зоне резания θ = 403,1 °С, сила резания Pz = 31,7 Н.
2) Заготовка, обработанная на оптимальныех режимах: подача S = 0,1 мм/об, скорость резания v = 5,6 м/с, глубина резания t = 0,5 мм, температура в зоне резания θ = 406,1 °С, сила резания Pz = 30,4 Н.
По результатам расчетов построим график распределения тангенциальных остаточных напряжений в поверхностном слое заготовки (рисунок 2).
Рисунок 2. График остаточных напряжений
Как видно из полученных результатов, обработка образца на оптимальных режимах способствует снижению уровня остаточных напряжений, что в целом будет способствовать снижению коробления детали после механической обработки. Полученное уравнение обрабатываемости позволит расчетным путем определять оптимальные режимы резания, при которых в детали будет формироваться минимальный уровень остаточных напряжений.
Выводы
1. Обработка заготовки на оптимальных режимах резания практически не повлияла на шероховатость обработанной поверхности по сравнению с обработкой на исходной скорости резания, однако повлияла на микротвердость обработанной поверхности, которая повысилась на 15%, что говорит о влиянии температурного и силового фактора на наклеп.
2. Из полученного графика зависимости расчетных тангенциальных остаточных напряжений можно увидеть, что, обработка образца на предлагаемых оптимальных режимах способствует снижению уровня остаточных напряжений, что в целом будет способствовать снижению коробления детали.
