ТЕХНОЛОГИИ ИЗГОТОВЛЕНИЯ ПОРОШКОВЫХ КОМПОЗИЦИОННЫХ МАТЕРИАЛОВ
Конференция: CCLXVIII Студенческая международная научно-практическая конференция «Молодежный научные форум»
Секция: Технические науки
лауреатов
участников
лауреатов


участников


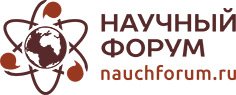
CCLXVIII Студенческая международная научно-практическая конференция «Молодежный научные форум»
ТЕХНОЛОГИИ ИЗГОТОВЛЕНИЯ ПОРОШКОВЫХ КОМПОЗИЦИОННЫХ МАТЕРИАЛОВ
Введение
Используемые в порошковой металлургии металлические и керамические порошки должны обладать определенными техническими и технологическими свойствами. Одним из таких свойств является сыпучесть, от которой зависит, например, производительность используемых технологических линий. Крупные порошки (>40 мкм) даже осколочного типа, как правило, обладают удовлетворительной сыпучестью. Чем мельче порошок, тем хуже его сыпучесть.
В различных отраслях промышленности, в частности при производстве пресс-порошков для изготовления твердых сплавов, для повышения сыпучести порошковых материалов давно разработаны и используются различные способы агломерации порошков. Данное исследование посвящено выбору способа агломерации/компактирования порошковых композитов, содержащих карбиды кремния и бориды циркония, предназначенных для использования при изготовлении сверхзвуковых аппаратов по аддитивным технологиям и технологиям порошковой металлургии.
Грануляцией называют промышленный процесс, при котором мелкие частицы связываются вместе в большие гранулы. Гранулированные продукты во многих случаях имеют преимущества перед порошкообразными: низкое пылеобразование, удобство транспортирования, высокие удельная поверхность и пористость, сохранение сыпучести с течением времени.
Применение сверхвысокотемпературных керамических материалов
С 2021 года ведущие мировые державы, такие как США и Россия, продолжают разрабатывать гиперзвуковые аппараты и связанные с ними технологии и методы испытаний (рисунок 1).
Рисунок 1. Российский гиперзвуковой летательный аппарат – Ю-71
При создании будущих гиперзвуковых аппаратов, которые эксплуатируются при высоких числах Маха, возникает задача разработки материала элементов корпуса, способного претерпевать тепловые нагрузки более чем в 2000°С, а так же иметь стойкость к ударной волне, возникающей в следствие диссоциации воздуха в слое контакта. Из условий эксплуатации летательных аппаратов нового поколения формулируются требования к материалу наиболее теплонагруженных элементов корпуса.
Основными являются: термическая и окислительная стойкость. Термическая стойкость – это способность керамического изделия выдерживать без разрушения резкие смены температуры. Окислительная стойкость – разновидность химической стойкости – способность материала противостоять воздействию окислительной среды (в данном случае в газообразном состоянии).
Керамика на основе нитрида кремния не может быть использована при температуре более 2000°С, т.к. нитрид кремния разлагается при 1900°С на конденсированный кремний и газообразный азот.
Распространенным примером соединения на основе боридов могут служить композиты с матричным компонентом в виде боридов циркония или гафния, дисперсноупрочненные включениями из частиц карбида кремния и других тугоплавких соединений (силицидов, карбидов, нитридов). Композиция 80об.% ZrB2-20об.% SiC зарекомендовала себя в качестве оптимального состава, способного обеспечивать высокую окислительную стойкость [1].
Рисунок 2. СЭМ-снимки шлифов композитов, полученных с использованием различных керамических наполнителей: 80 об. % ZrB2 – 20об.% SiC (а), 20 об. % ZrB2 – 80 об. % SiC (б)
Классификация методов грануляции
При анализе литературы установлено, что для укрупнения тонкодисперсных порошков возможно применение крупнотоннажных технологий, таких как [2]:
• агломерация ПК в аппаратах кипящего слоя (КС);
• гранулирование ПК окатыванием;
•гранулирование окатыванием с предварительным формованием увлажненной тукосмеси ПК.
Наиболее удачным вариантом, в силу сравнительно низкой себестоимости и качеством полученных порошков, является гранулирование окатыванием с предварительным формованием. Исходную порошкообразную смесь смешивают со связующим веществом и увлажняют. Полученную увлажненную тукосмесь формуют через перфорированные приспособления с заданными размерами ячеек. Непрерывное движение гранулируемой смеси способствует зародышеобразованию и росту гранул, а также разрушению наименее прочных из них. Классическая схема окатывания: порошок, орошаемый связующим, подают во вращающийся аппарат, который установлен горизонтально или с небольшим наклоном. Смоченные частицы агломерируются и, окатываясь, приобретают необходимые плотности и размеры. [3].
При выборе способа гранулирования и вида установки следует учесть, что гранулирование связанно с изменениями агрегатного состояния, формы и свойств гранулята. Гранулирование разделяют по следующим признакам:
1. Из жидкой фазы, диспергированием ее на капли с последующей кристаллизацией растворенного вещества при обезвоживании или охлаждения этой фазы.
2. Из твердой фазы, прессованием с последующем дроблением брикетов до гранул требуемого размера.
3. Из смеси жидкой и твёрдой фаз, агломерацией порошков с последующей окутыванием агломератов и упрочнением связей между частицами при удалении жидкой фазы.
4. Из газообразной фазы, конденсацией (десублимацией) с образованием твердых гранул
5. Из смеси жидкой и газообразной фазы при протекании химической реакции
6. Из смеси жидкой, твердой и газообразной фазы при протекании химической реакции.
В работе [4] Лобовиковым Д. В. с коллегами выполнялись исследования процесса гранулирования композиционного материала с различной пористостью и физико-механическими свойствами. Размер получаемых гранул составляет около 1 мм и с течением времени увеличивается до 2-3 мм. Данный факт говорит о невозможности непосредственного получения ПК требуемой фракции (40-90 мкм), однако получаемые гранулы 1-2 мм удобно протирать в установки типа «сито протирочное».
В работе [5] рассмотрено два варианта агломерации. Исследования проводили на примере порошка карбида титана, плакированного хромом, железом и титаном в матрице из смеси наноразмерных и ультрадисперсных порошков хрома, никеля и титана. Были получены композитные порошки гранулометрического состава 40-125 мкм и 40-160 мкм.
Технология №1 «брикетирование – размол – рассев – спекание»
Этапы:
Подготовка связующего. Связующее состоит из четырех массовых долей карбоксилметилцеллюлозы (КМЦ), растворенных в дистиллированной воде. Время до полного растворения КМЦ при комнатной температуре составляло 15-30 минут.
Получение порошкового компакта (брикетирование) В исходную порошковую смесь добавляли 30 массовых долей приготовленного связующего (итоговая концентрация КМЦ – 1,7% по массе) и механически перемешивали до однородного состояния. После этого полученную смесь сушили при температуре 120°С.
Получение гранулированных частиц размером 80-125 μm (размол – рассев). Полученный компакт подвергался механическому ударно-сдвиговому разрушению (шаровая мельница). В результате механического разрушения образовывались гранулы различного фракционного состава. Используя металлические сита с размерами ячеек 80 и 125 мкм, производили разделение частиц. Крупные частицы подвергались повторному механическому ударно-сдвиговому разрушению и заново просеивались. Гранулированные порошковые частицы с размерами менее 80 мкм повторно проходили стадию брикетирования с единственным отличием: вместо указанного выше связующего, использовалась дистиллированная вода, добавленная в необходимой пропорции.
Спекание. Спекание гранул проводилось в вакуумной печи при температуре 1300 °С.
Рисунок 3. Микрофотографии гранулированной порошковой смеси до спекания: а) гранулированные порошковые частицы; б) морфология отдельных гранул [5]
Технология №2 «окатывание – рассев – спекание».
Порошковые компоненты, просеянные через сито 40 мкм, и взятые в искомых пропорциях, смешивали со связующим веществом и обкатывали до сферической формы необходимого размера. Подготовка связки состоит из следующих шагов. Навеску КМЦ помещали в ёмкость с водой и нагревали до 60 °С. Навеску брали таким образом, чтобы получить 10% раствор КМЦ. После проделанных операций раствор выдерживался в течение суток для полного набухания КМЦ.
Перед введением связки в порошок его увлажняли дистиллированной водой в количестве 6-7% от веса порошка. Затем порошок перемешивали в смесителе типа «пьяная бочка» и постепенно добавляли путем распыления раствор КМЦ из расчёта 5г раствора на 100г готовой смеси порошков (итоговая концентрация КМЦ – около 0,5% по массе), после чего перемешивание продолжали в течение не менее 2-х часов. По окончании процесса порошок рассыпали в противни и подвергали сушке в сушильном шкафу в течение 1-2 часов при температуре не более 80 °С. Далее порошки рассевали на виброситах. Затем в порошки, оставшиеся на сите 160 мкм, добавляли фторопластовые цилиндры размером ф15х15 мм в количестве 100 г. и процесс повторяли до полного рассева. Порошки <40 мкм снова отправляли на грануляцию.
После введения необходимого количества связующего порошковый материал перемешивается в агломераторе, представляющем собой вращающийся бункер для порошка, установленный под углом в 30°, внутри которого вращается вал с лопастями в противоположном направлении. Далее полученный агломерированный порошок заданной влажности протирается через сито с размером ячейки 400 мкм и оправляется на сушку в сушильный шкаф. Температура сушки 80-85 °С, что обеспечивает оптимальную скорость удаления влаги из КМЦ при отсутствии окисления материала. Во время сушки происходит усадка содержащих КМЦ агломератов, таким образом, после сушки большинство агломератов имеет размеры менее 400 мкм, то есть меньше ячейки используемого сита. Далее высушенные агломераты рассеивают на виброгрохоте. Фракция +160 мкм протирается через сито 200 мкм и вновь рассеивается. Фракция 160 – 40 мкм отправляется на дополнительную сушку и дальнейшее спекание. Хвосты от обоих рассевов – фракция - 40 мкм, отправляются на повторную агломерацию.
Выход годного порошка одного такого цикла в среднем не превышает 20-30%, таким образом, для полной агломерации необходимо провести 5-6 таких циклов.
Выводы
Порошковые гранулированные композиты являются основой для создания сверхвысокотемпературной керамики, необходимой для производства гиперзвуковых изделий авиационной техники. Технология создания гранулированных порошков отличается высокой трудоемкостью, являясь, по сути эмпирическим искусством, что говорит о важности накопления опыта, использовании различных технологических приемов и комбинаций оборудования.
